The radiation-hardened electronics industry plays a crucial role in ensuring the reliability and functionality of electronic systems exposed to harsh environments, particularly in space, nuclear facilities, and high-energy physics applications. As the demand for resilient electronics continues to grow, innovative technologies are emerging to enhance the performance and durability of radiation-hardened components. This article delves into the key technologies shaping the radiation-hardened electronics industry and their implications for future applications.
The radiation hardened electronics industry size is expected to grow from USD 1.7 billion in 2024 to USD 2.1 billion by 2029.; it is expected to grow at a CAGR of 4.8% from 2024 to 2029. The use of radiation-hardened electronics industry in military missions is undergoing significant growth; for instance, modern military platforms like fighter jets, tanks, and drones integrate numerous electronic systems. Radiation hardening ensures the reliable operation of these systems within the complex electromagnetic environment of modern warfare.
1. Understanding Radiation Hardening
What is Radiation Hardening?
Radiation hardening refers to the process of designing and manufacturing electronic components that can withstand the damaging effects of ionizing radiation. This is essential for systems deployed in environments where radiation exposure can cause malfunctions, degradation, or complete failure of standard electronic devices.
Types of Radiation
Key types of radiation that impact electronics include gamma rays, neutrons, protons, and heavy ions. Each type poses unique challenges, necessitating specific strategies for hardening electronic components against their effects.
2. Advanced Materials
Use of Wide Bandgap Semiconductors
Wide bandgap semiconductors, such as silicon carbide (SiC) and gallium nitride (GaN), are gaining traction in the radiation-hardened electronics market. These materials offer superior thermal conductivity, higher breakdown voltages, and enhanced radiation tolerance compared to traditional silicon-based components. Their robustness makes them ideal for applications in space and military environments.
Radiation-Resistant Polymers
Innovations in polymer materials are also contributing to the development of radiation-hardened electronics. Specialized radiation-resistant polymers can protect sensitive components from radiation exposure while maintaining electrical integrity, making them valuable in various applications.
Download PDF Brochure @
https://www.marketsandmarkets.com/pdfdownloadNew.asp?id=44047967
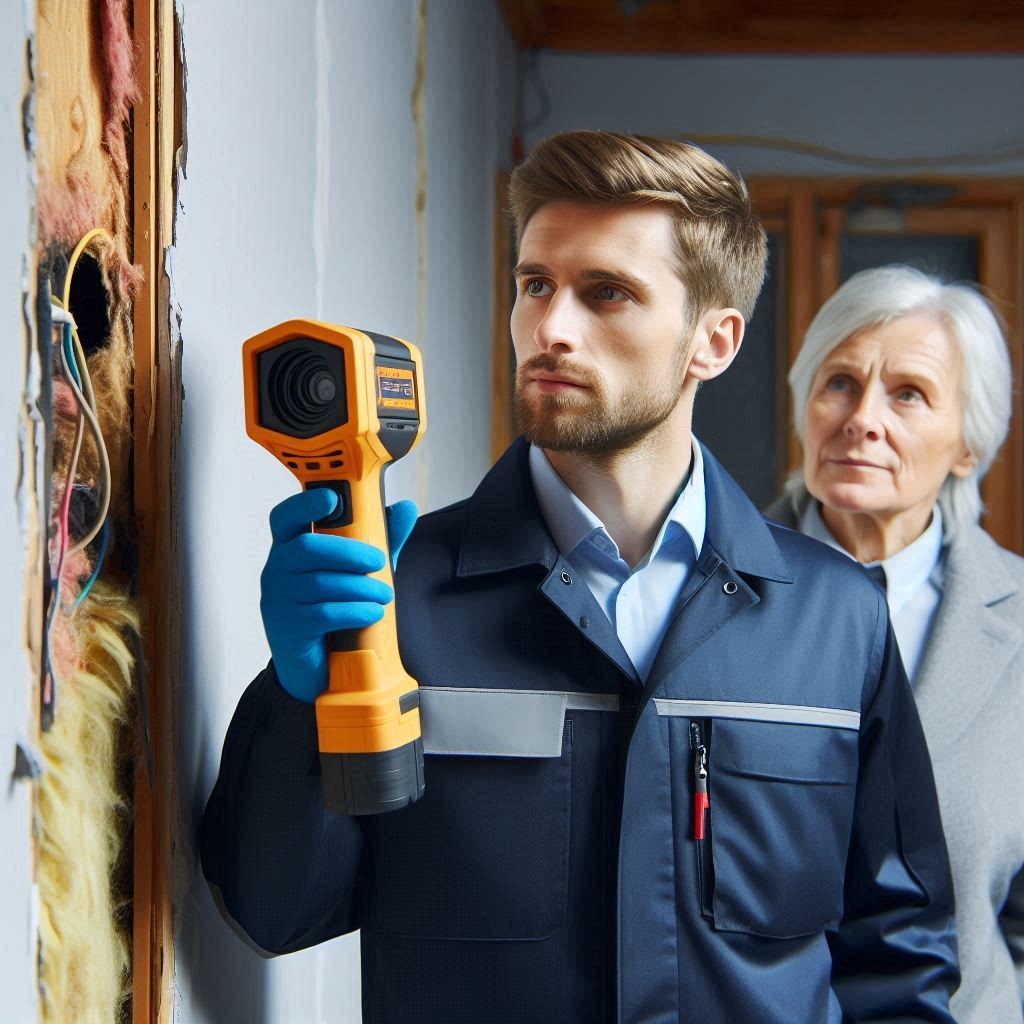
3. Circuit Design Techniques
Redundant Design Approaches
Redundant circuit designs are a popular strategy for enhancing the resilience of radiation-hardened electronics. By incorporating duplicate components or systems, manufacturers can ensure that if one part fails due to radiation exposure, the other can take over, maintaining functionality.
Error Correction Codes (ECC)
Error correction codes are essential in radiation-hardened systems, especially in memory devices. ECC can detect and correct data corruption caused by radiation-induced errors, ensuring reliable data storage and retrieval.
4. Packaging and Shielding Technologies
Advanced Packaging Solutions
The packaging of radiation-hardened electronics is critical for protection against environmental hazards. Advanced packaging solutions, such as ceramic and metal enclosures, provide enhanced shielding against radiation while ensuring thermal management and mechanical stability.
Shielding Techniques
Effective shielding techniques involve using materials that absorb or deflect radiation before it reaches sensitive components. Innovations in shielding materials, such as lead-based composites or advanced polymers, enhance the protection of electronic systems deployed in high-radiation environments.
5. Testing and Validation
Comprehensive Radiation Testing
Rigorous testing protocols are essential for validating the performance of radiation-hardened electronics. Testing typically includes exposure to various types of radiation to assess the components’ reliability and functionality under real-world conditions.
Simulation and Modeling
Advancements in simulation and modeling technologies allow manufacturers to predict how electronic components will perform in radiation environments. This capability helps in optimizing designs and materials before physical testing, speeding up the development process.
6. Radiation-hardened Electronics Industry Applications and Future Outlook
Space Exploration
The increasing demand for advanced electronic systems in space exploration drives innovation in radiation-hardened technologies. As missions become more ambitious, the need for reliable components capable of withstanding harsh space environments will only grow.
Nuclear Industry
The nuclear industry also relies heavily on radiation-hardened electronics for monitoring, control systems, and safety mechanisms. As regulations evolve and the demand for nuclear energy increases, the need for robust electronic systems will remain critical.
Advancements in Medical Devices
Radiation-hardened electronics are finding applications in medical devices used in radiation therapy and diagnostic imaging. Ensuring the reliability of these systems is vital for patient safety and treatment efficacy.
The radiation-hardened electronics industry is at the forefront of technological innovation, driven by the need for reliable components in challenging environments. Advances in materials, circuit design, packaging, and testing methodologies are paving the way for the development of next-generation radiation-hardened systems. As industries such as aerospace, nuclear, and healthcare continue to evolve, the importance of these technologies will only increase, shaping the future of reliable electronic systems in the face of radiation challenges.