The advent of Industry 4.0 marks a transformative shift in manufacturing and industrial processes, characterized by the integration of digital technologies with physical systems. At the heart of this revolution lies Cyber-Physical Systems (CPS), which connect the physical world with the digital universe, enabling unprecedented levels of automation, efficiency, and intelligence. Explores the role of Cyber-Physical Systems in Industry 4.0, highlighting its applications, benefits, and future prospects.
Understanding Cyber-Physical Systems
Cyber-Physical Systems (CPS) are engineered systems that combine computational elements with physical processes. By utilizing sensors, actuators, and advanced data analytics, CPS enables real-time monitoring and control of physical processes. This fusion of digital and physical realms allows for more intelligent decision-making and operational efficiency, essential components of Industry 4.0.
In the context of Industry 4.0, CPS encompasses various technologies, including the Internet of Things (IoT), artificial intelligence (AI), machine learning, big data analytics, and robotics. Together, these technologies create interconnected, smart systems that adapt to changing conditions and optimize processes, driving innovation and enhancing productivity across industries.
Cyber-Physical Systems Industry outlook
The global cyber-physical systems market is expected to be valued at USD 124.1 billion in 2024 and is projected to reach USD 255.3 billion by 2029; it is expected to grow at a CAGR of 15.5% from 2024 to 2029. Market participants have adeptly addressed rising cyber-physical systems demands in diverse industries, extending their global reach through strategic growth approaches like introducing new products, acquiring assets, forging partnerships, fostering collaborations, establishing alliances, and expanding their operations. The cyber-physical systems market is driven by the integration of technologies such as AI and IoT that enhance system capabilities. Additionally, the revolution of Industry 4.0 promotes smart factories and automation which increasing demand for CPS in various sectors.
Key Applications of CPS in Industry 4.0
1. Smart Manufacturing
Cyber-Physical Systems in Industry 4.0 play a pivotal role in smart manufacturing, where machines, systems, and processes communicate and collaborate in real time. This interconnected environment allows for:
- Real-Time Monitoring: Embedded sensors in machinery provide continuous feedback on performance, enabling manufacturers to monitor operations closely and identify issues before they escalate, ensuring smooth production processes.
- Predictive Maintenance: By analyzing machine data, CPS can predict potential failures, allowing manufacturers to perform proactive maintenance. This approach reduces unplanned downtime and enhances overall operational efficiency.
- Flexible Production Lines: CPS enables quick reconfiguration of production systems to accommodate changing product designs or production volumes, improving responsiveness to market demands and customer preferences.
2. Supply Chain Optimization
The role of Cyber-Physical Systems in Industry 4.0 extends to optimizing supply chain operations by providing end-to-end visibility and control:
- Inventory Management: Real-time tracking of inventory levels allows manufacturers to optimize stock management, reduce excess inventory, and ensure timely replenishment, ultimately minimizing costs.
- Demand Forecasting: Integrated data analytics within CPS can forecast demand patterns more accurately, enabling manufacturers to plan production schedules and resource allocation effectively, reducing waste and increasing profitability.
- Logistics Automation: CPS facilitates automated logistics operations, including warehouse management and transportation optimization, leading to improved efficiency and reduced operational costs throughout the supply chain.
Download PDF Brochure @ https://www.marketsandmarkets.com/pdfdownloadNew.asp?id=150375126
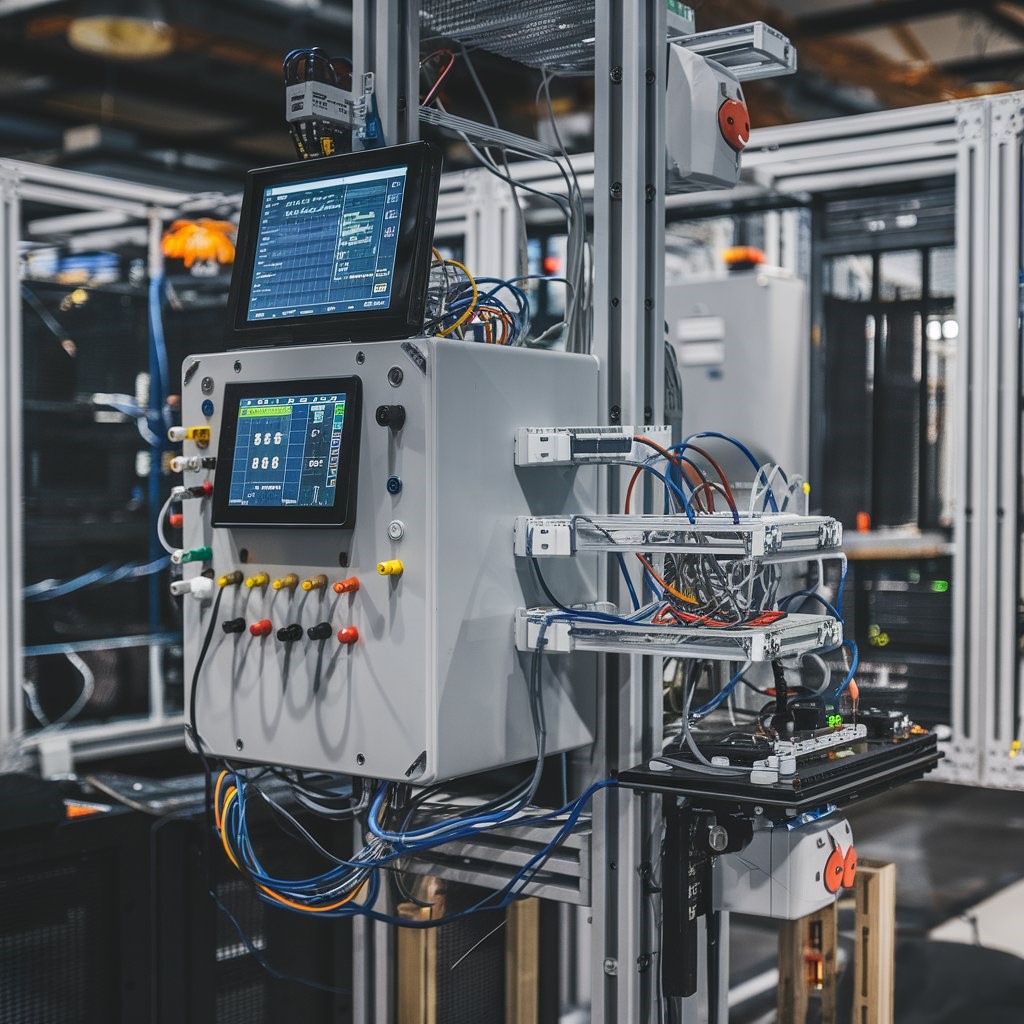
3. Enhanced Product Development
Cyber-Physical Systems in Industry 4.0 significantly enhance product development processes through advanced simulation and prototyping techniques:
- Digital Twins: A digital twin is a virtual representation of a physical object or system. By simulating real-world conditions, manufacturers can optimize designs, test performance, and predict potential issues before physical production begins, leading to faster time-to-market and improved product quality.
- Collaborative Design: CPS enables collaboration among design teams, suppliers, and customers, fostering innovation and ensuring that products meet user needs more effectively. This collaborative approach accelerates the development cycle and enhances competitive advantage.
4. Improved Quality Control
Quality assurance is paramount in manufacturing, and Cyber-Physical Systems in Industry 4.0 contribute significantly to this area:
- Automated Inspection: Advanced imaging and sensor technologies within CPS allow for real-time quality inspection of products on the assembly line, ensuring defects are detected and addressed immediately, thereby maintaining high quality standards.
- Data-Driven Decision Making: By analyzing quality data collected through CPS, manufacturers can identify root causes of defects and implement corrective actions swiftly, improving product quality and customer satisfaction.
Benefits of Cyber-Physical Systems in Industry 4.0
The integration of Cyber-Physical Systems in Industry 4.0 offers numerous benefits, including:
- Increased Efficiency: Automation and real-time monitoring streamline operations, leading to reduced cycle times and improved productivity. CPS ensures optimal resource utilization, minimizing waste.
- Enhanced Flexibility: CPS allows manufacturers to respond swiftly to changing market demands and customer preferences, facilitating customized production that meets specific needs, thereby increasing competitiveness.
- Reduced Costs: By optimizing resource use, minimizing waste, and preventing equipment failures through predictive maintenance, CPS helps lower operational costs and improve profitability for manufacturers.
- Improved Safety: Automated monitoring and control systems enhance workplace safety by reducing human error and ensuring compliance with safety regulations, fostering a safer working environment for employees.
Challenges and Considerations
Despite the significant advantages, the implementation of Cyber-Physical Systems in Industry 4.0 presents challenges:
- Integration Complexity: Combining legacy systems with new technologies can be complex, requiring substantial investment in infrastructure, training, and change management to ensure a seamless transition to CPS-enabled processes.
- Data Security: With increased connectivity comes the risk of cyber threats. Ensuring the security and privacy of data transmitted and stored in CPS is crucial for maintaining trust and protecting sensitive information from malicious attacks.
- Skill Gap: The shift towards digitalization necessitates a workforce skilled in data analytics, AI, and other advanced technologies. Addressing the skill gap through training and development programs will be essential for maximizing the benefits of CPS.
Future Prospects
The future of Cyber-Physical Systems in Industry 4.0 is bright, with continued advancements in technology paving the way for even greater innovations. As CPS evolves, we can expect:
- Greater AI Integration: The incorporation of AI and machine learning will enhance the decision-making capabilities of CPS, enabling more intelligent and autonomous systems that adapt to changing conditions without human intervention.
- Expansion of Digital Twins: The use of digital twins will become more prevalent, allowing for more accurate simulations and better-informed decisions throughout the product lifecycle, ultimately leading to higher-quality products and services.
- Sustainable Practices: As industries focus on sustainability, CPS will play a key role in optimizing resource use, reducing waste, and enhancing energy efficiency, contributing to a more sustainable manufacturing landscape.
Cyber-Physical Systems in Industry 4.0 are revolutionizing manufacturing by creating interconnected, intelligent environments that enhance efficiency, flexibility, and quality. As businesses increasingly adopt CPS technologies, they are better equipped to meet the challenges of the modern marketplace, driving innovation and growth. The future of manufacturing is not only about advanced machinery but also about smart systems that adapt and optimize processes in real time. By embracing the potential of Cyber-Physical Systems companies can pave the way for a more sustainable, innovative, and productive future. The integration of CPS is essential for companies looking to remain competitive and meet the evolving demands of their customers in an increasingly digital world.