The future of industrial agitators is characterized by rapid advancements in technology and design that are revolutionizing how materials are mixed and processed across various sectors. As industries seek to enhance efficiency, quality, and sustainability, understanding these trends and innovations is crucial. This article delves deeper into the evolving landscape of industrial agitators, highlighting key innovations, emerging trends, and their applications.
The industrial agitators Industry is expected to reach USD 3.2 billion by 2028 from USD 2.6 billion in 2023, at a CAGR of 4.0 % during the 2023–2028 period. The major factors driving the market growth of the industrial agitators market include increasing demand for homogeneous mixing, growing need for energy efficient mixing equipment in pharmaceutical, chemical and food & beverage industries, and growing adoption of customized agitators for several applications
Key Innovations in the Future of Industrial Agitators
1. Smart Agitation Technology
One of the most significant trends defining the future of industrial agitators is the integration of smart technology. Modern agitators are increasingly equipped with Internet of Things (IoT) sensors that continuously monitor key operational parameters such as viscosity, temperature, and pressure. This real-time data enables automated adjustments to the agitation process, ensuring optimal performance.
Benefits of Smart Technology:
Enhanced Efficiency: Automated adjustments reduce energy consumption and improve mixing consistency.
Predictive Maintenance: Machine learning algorithms analyze data to predict equipment failures, allowing for proactive maintenance and minimizing downtime.
Remote Monitoring: Operators can monitor agitator performance remotely, facilitating real-time decision-making and reducing the need for on-site inspections.
2. Advanced Materials and Designs
The choice of materials and design innovations play a pivotal role in the future of industrial agitators. Manufacturers are increasingly utilizing advanced alloys and composite materials that offer greater durability and resistance to wear and corrosion.
Key Design Innovations:
Aerodynamic and Hydrodynamic Designs: These designs optimize fluid flow, enhancing mixing efficiency and reducing energy consumption.
Customizable Impeller Designs: Advanced impeller designs allow for tailored mixing solutions based on specific applications, improving overall performance.
Wear-Resistant Coatings: The application of specialized coatings can extend the lifespan of agitators, reducing maintenance costs and downtime.
3. Modular Agitator Systems
The move towards modular designs is gaining momentum in the future of industrial agitators. Modular systems enable manufacturers to customize their agitators based on specific production needs, providing flexibility and scalability.
Advantages of Modular Systems:
Cost-Effectiveness: Modular components can be replaced or upgraded without needing to overhaul the entire system, saving time and resources.
Simplified Installation: Modular systems often require less complex installation, reducing setup times and associated costs.
Adaptability: As production demands change, businesses can easily modify their systems to meet new requirements, ensuring they remain competitive.
Download PDF Brochure @
https://www.marketsandmarkets.com/pdfdownloadNew.asp?id=59649096
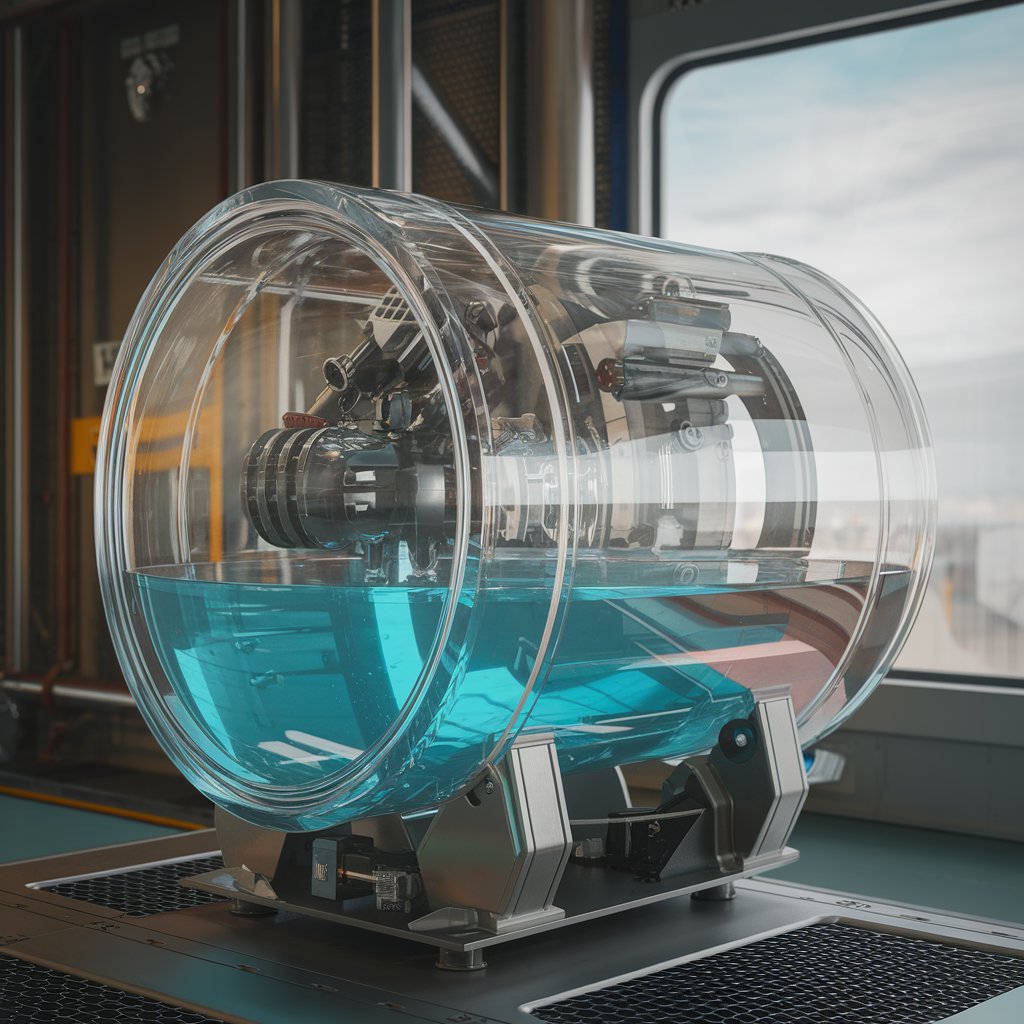
Emerging Trends in Future of Industrial Agitators
1. Sustainability and Energy Efficiency
With increasing global focus on sustainability, the future of industrial agitators is heavily influenced by the need for energy-efficient solutions. Businesses are seeking agitators that minimize environmental impact while maintaining high performance.
Sustainable Innovations:
Energy-Efficient Motors: The incorporation of high-efficiency motors reduces overall energy consumption, aligning with sustainability goals.
Optimized Mixing Processes: Innovations that reduce mixing times and energy requirements contribute to lower operational costs and reduced environmental impact.
Use of Recyclable Materials: Many manufacturers are exploring the use of recyclable and environmentally friendly materials in agitator construction.
2. Automation and Robotics
The rise of automation and robotics is transforming various industrial processes, including agitation. The future of industrial agitators is expected to feature greater integration with robotic systems.
Impact of Automation:
Increased Precision: Robotic systems enhance the precision of mixing processes, leading to improved product consistency and quality.
Labor Cost Reduction: Automation can help reduce labor costs by minimizing the need for manual intervention in mixing operations.
Enhanced Flexibility: Automated systems can be programmed to adapt to varying production requirements, allowing for quick adjustments without significant downtime.
3. Enhanced Safety Features
As the complexity of industrial processes increases, ensuring safety in operations is paramount. The future of industrial agitators will incorporate advanced safety features to protect both operators and the environment.
Safety Innovations:
Automatic Shut-Off Mechanisms: These systems can detect anomalies and automatically shut down operations, preventing accidents.
Ergonomic Designs: Improved ergonomic designs aim to reduce physical strain on operators, contributing to a safer work environment.
Improved Containment Systems: Innovations in containment technology help prevent spills and leaks, enhancing overall safety and compliance with regulations.
Applications Driving the Future of Industrial Agitators
1. Food and Beverage Industry
The future of industrial agitators in the food and beverage sector is increasingly focused on meeting strict quality and safety regulations. Agitators in this industry must ensure thorough mixing without compromising the integrity of sensitive ingredients.
Key Considerations:
Hygienic Design: Future agitators will feature designs that prioritize cleanliness, with smooth surfaces and easy-to-clean components to prevent contamination.
Temperature Control: Agitators equipped with advanced temperature control systems will be crucial for processes requiring precise thermal management.
2. Pharmaceutical Manufacturing
In pharmaceutical manufacturing, precise mixing is critical for product efficacy and safety. The future of industrial agitators in this sector will focus on high accuracy and compliance with stringent regulations.
Innovations to Watch:
Sterile Mixing Technologies: Future agitators will increasingly adopt sterile mixing technologies to ensure product integrity and compliance with regulatory standards.
Real-Time Monitoring Systems: Implementing real-time monitoring systems will enhance quality control, enabling manufacturers to track mixing parameters closely.
3. Wastewater Treatment
As environmental concerns rise, the future of industrial agitators in wastewater treatment will emphasize efficiency and effectiveness in pollutant breakdown.
Focus Areas:
Enhanced Mixing Technologies: Innovations that improve the mixing of chemicals and wastewater will be essential for optimizing treatment processes.
Energy-Efficient Designs: Agitators that reduce energy consumption while maximizing mixing efficiency will become increasingly vital in this sector.
The future of industrial agitators is set for significant advancements driven by technology, sustainability, and evolving industry demands. As smart technologies, modular designs, and enhanced safety features emerge, businesses will be better equipped to meet the challenges of modern manufacturing. By embracing these innovations, industries can enhance operational performance, reduce environmental impact, and ensure a safer working environment. The ongoing evolution of industrial agitators promises to play a crucial role in shaping the efficiency and sustainability of various sectors for years to come.
The report profiles key Industrial agitators Companies such as SPX Flow, Inc. (US), Xylem Inc. (US),Ekato Group (Germany), Sulzer Ltd. (Switzerland) and NOV Inc (US).