Industrial agitation technology is a cornerstone of many manufacturing processes, facilitating the mixing of liquids, powders, and various ingredients to achieve uniformity and consistency. This technology is essential across diverse sectors such as food and beverage, pharmaceuticals, and chemical manufacturing, where the quality of the final product heavily relies on effective mixing. However, as industries face increasing pressures to enhance efficiency, reduce costs, and minimize environmental impacts, the traditional approaches to agitators are being challenged. Innovations in agitators technology are emerging as game-changers, offering new solutions that not only streamline processes but also improve product quality and safety. Latest advancements in industrial agitation technology, exploring their implications and benefits for various sectors.
The industrial agitators market is expected to reach USD 3.2 billion by 2028 from USD 2.6 billion in 2023, at a CAGR of 4.0 % during the 2023–2028 period. The major factors driving the market growth of the industrial agitators market include increasing demand for homogeneous mixing, growing need for energy efficient mixing equipment in pharmaceutical, chemical and food & beverage industries, and growing adoption of customized agitators for several applications.
The Evolution of Agitators Technology
Historically, industrial mixing was dominated by mechanical agitators that, while functional, often operated at fixed speeds, leading to inefficiencies and excessive energy consumption. These systems were also prone to mechanical wear and contamination, posing challenges in maintaining product integrity. The advent of new materials and the rapid advancement of digital technologies have spurred significant changes in this field. Modern agitators technology focuses on achieving higher efficiency, reliability, and safety while addressing the growing demand for sustainable practices. The emergence of smart technologies and automation has transformed how mixing processes are designed and executed, paving the way for more intelligent and adaptable systems that respond in real time to varying conditions.
Key Innovations
- Smart Agitation Systems
- IoT and Real-Time Monitoring: The integration of Internet of Things (IoT) technology into industrial agitators systems allows for comprehensive monitoring of mixing parameters such as viscosity, temperature, and pressure. Sensors collect data in real time, enabling operators to make informed adjustments on the fly. This capability not only enhances the quality of the final product but also leads to increased operational efficiency. For example, if a mixture’s viscosity changes unexpectedly, the system can automatically adjust the agitators speed to maintain optimal mixing conditions, thus preventing inconsistencies.
- Machine Learning Algorithms: The application of machine learning in agitators technology allows for predictive analytics based on historical mixing data. These algorithms can identify patterns and trends, optimizing the mixing process by suggesting adjustments before issues arise. By utilizing this data-driven approach, manufacturers can minimize waste, enhance quality control, and ultimately improve production efficiency.
- Advanced Mixing Techniques
- Ultrasonic Mixing: Ultrasonic mixing employs high-frequency sound waves to create cavitation bubbles within a liquid medium. As these bubbles collapse, they generate intense localized energy, facilitating the dispersion of solid particles and emulsification of liquids. This method is particularly advantageous in industries such as pharmaceuticals and food production, where achieving fine particle sizes and stable emulsions is crucial. The result is improved homogeneity and reduced processing times, contributing to higher-quality products.
- High-Shear Mixers: High-shear mixers are engineered to create significant shear forces that effectively break down solids in liquids. These mixers excel at dispersing powders and achieving thorough blending quickly, which is particularly beneficial in applications where time efficiency is paramount. By reducing the time needed for mixing, high-shear mixers not only increase productivity but also enhance the final product’s quality, making them indispensable in fast-paced industrial environments.
Download PDF Brochure @
https://www.marketsandmarkets.com/pdfdownloadNew.asp?id=59649096
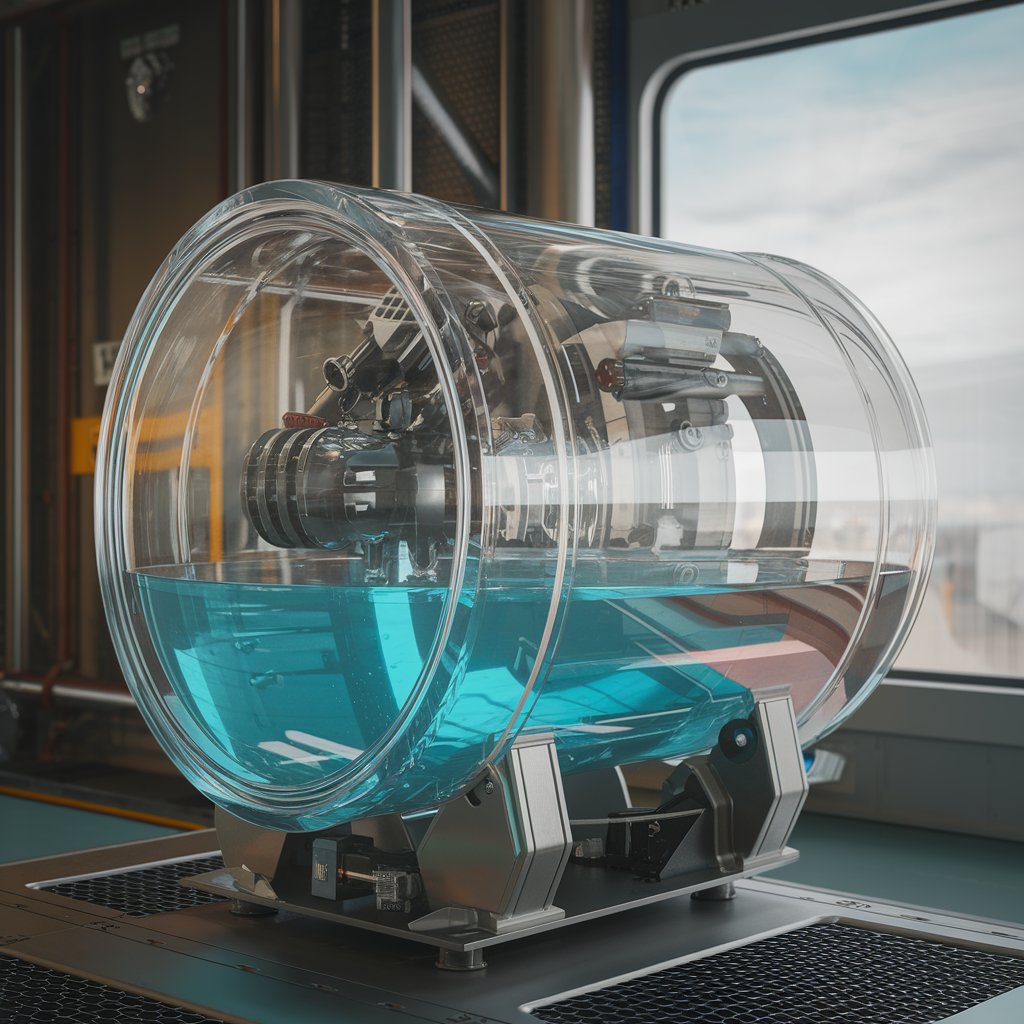
- Energy Efficiency and Sustainability
- Variable Frequency Drives (VFDs): VFD technology enables the precise control of motor speeds, allowing agitators systems to adjust based on real-time operational demands. This flexibility leads to significant energy savings, as motors operate only at the required capacity rather than running continuously at a fixed speed. By optimizing energy use, manufacturers can reduce operational costs and decrease their carbon footprint, aligning with global sustainability initiatives and enhancing their corporate social responsibility profile.
- Eco-friendly Materials: The push for sustainability has led to the development of biodegradable and recyclable materials for mixer construction. These innovations reduce the environmental impact of industrial processes, supporting manufacturers’ goals to lower waste and resource consumption. By incorporating eco-friendly materials, companies not only comply with environmental regulations but also cater to increasingly eco-conscious consumers, enhancing their market appeal.
- Modular and Scalable Solutions
- Modular Mixing Systems: Modular mixing systems offer manufacturers the flexibility to adapt their mixing setups to changing production needs. These systems can be easily reconfigured, allowing businesses to scale operations up or down without significant capital investment. This adaptability is particularly valuable in industries with fluctuating demand, as it minimizes downtime and maximizes resource utilization, ultimately contributing to increased profitability.
- Process Intensification
- Microfluidics: Microfluidic technology involves manipulating fluids at a microscale, enabling enhanced mixing efficiency and accelerated reaction rates. This approach is particularly useful in the pharmaceutical industry, where precise formulations are critical. By facilitating rapid and uniform mixing at a microscopic level, microfluidics allows for the development of advanced drugs and therapeutics, streamlining the path from research to market.
- Continuous Mixing: Continuous mixing processes represent a shift from traditional batch methods, allowing for a steady flow of materials through the mixing system. This approach enhances efficiency by reducing transition times between batches and maintaining consistent product quality. Continuous systems are especially advantageous in high-volume production settings, where maintaining quality while scaling output is essential.
Applications Across Industries
Food and Beverage
In the food and beverage industry, the ability to achieve precise mixing can significantly impact flavor and texture. Advanced mixing technologies, such as ultrasonic and high-shear mixers, enable manufacturers to create stable emulsions, resulting in uniform products that meet consumer expectations. Additionally, these innovations reduce production times, allowing companies to respond quickly to market demands and minimize operational costs. For instance, improved mixing processes can enhance the flavor profiles of sauces and dressings, leading to higher customer satisfaction and loyalty.
Pharmaceuticals
The pharmaceutical sector stands to gain tremendously from innovations in future agitators technology. Precise and consistent mixing is critical for drug formulations, where even slight variations can affect efficacy and safety. Smart agitation systems that utilize real-time monitoring and machine learning ensure that mixtures are homogeneous, minimizing the risk of contamination and ensuring compliance with regulatory standards. By improving mixing precision, these technologies enhance the reliability of pharmaceutical products, ultimately benefiting patient safety and health outcomes.
Chemical Manufacturing
In chemical processing, the integration of high-shear and ultrasonic mixing techniques has transformed reaction rates and product yields. These advanced methods allow for faster dissolution of solids and better mixing of reactants, leading to more efficient production cycles. Furthermore, the use of smart control systems enables manufacturers to fine-tune mixing conditions in real time, resulting in increased efficiency and reduced waste. As chemical manufacturers seek to optimize their processes and remain competitive, these innovations will play a crucial role in driving growth.
Materials Science
Innovative agitators technologies are also making significant contributions to materials science. Improved mixing techniques enhance the properties of composite materials by ensuring better dispersion of additives, such as fibers or nanoparticles. This level of control allows for the development of advanced materials with tailored characteristics, such as increased strength or improved thermal stability. As industries continue to demand higher-performance materials, the ability to achieve precise mixing will be essential in meeting these challenges.
Challenges and Future Directions
Despite the significant advancements in agitators technology, several challenges persist. Integrating new technologies into existing systems can be complex and may require substantial investment. Additionally, many organizations face a skills gap, as the workforce must be trained to effectively operate and maintain these advanced systems. As industries increasingly prioritize sustainability, the development of greener technologies will remain a critical focus, driving further research and innovation. Manufacturers will need to embrace these changes to stay competitive and meet evolving consumer demands.
The landscape of industrial agitators technology is undergoing a remarkable transformation, driven by advancements that enhance efficiency, reduce costs, and improve product quality across various sectors. By embracing innovations such as smart systems, advanced mixing techniques, and sustainable practices, manufacturers can position themselves for success in an increasingly competitive market. As the industry continues to evolve, staying informed about these innovations and their applications will be essential for businesses aiming to maintain a competitive edge and meet the demands of the future.