Surface Mount Technology (SMT) has transformed the landscape of electronics manufacturing, offering numerous benefits that significantly enhance productivity, efficiency, and product performance. As the demand for smaller, more powerful electronic devices grows, SMT has become a preferred choice for manufacturers across various industries.
The surface mount technology (SMT) market size is projected to grow from USD 5.8 billion in 2023 to USD 8.4 billion by 2028; it is expected to grow at a CAGR of 7.8% during the forecast period. The growing adoption of electric vehicles is one of the major drivers of the market.
Explores the key advantages of using SMT in manufacturing.
1. Space Efficiency
One of the most significant advantages of SMT is its ability to maximize space on printed circuit boards (PCBs). Unlike traditional through-hole technology, where components must be inserted into drilled holes, SMT allows components to be mounted directly onto the surface of the PCB. This facilitates a denser arrangement of components, leading to smaller circuit boards.
Benefits:
Compact Designs: The reduction in PCB size enables the creation of more compact and lightweight electronic devices. This is particularly advantageous in sectors such as consumer electronics, automotive, and telecommunications, where space is at a premium. For example, smartphones and wearables benefit greatly from this miniaturization, as it allows for additional features without increasing size.
Enhanced Functionality: By fitting more components onto a smaller board, manufacturers can incorporate complex functionalities without enlarging the device. This is crucial for applications like Internet of Things (IoT) devices, which require multiple sensors and connectivity options in limited space.
2. Improved Performance
SMT components generally offer superior performance compared to their through-hole counterparts. This improvement is largely due to shorter electrical paths and reduced parasitic inductance and capacitance, which result in better signal integrity and faster operational speeds.
High-Speed Applications: Enhanced performance characteristics make SMT ideal for high-speed and high-frequency applications, such as radio frequency (RF) and microwave technologies. For instance, devices in telecommunications can operate more effectively due to the reduced signal loss associated with SMT components.
Lower Signal Loss: Improved signal integrity translates into lower signal loss, which is essential for maintaining the performance of sophisticated electronic systems. This reliability is critical in applications like data centers, where performance consistency is paramount.
3. Enhanced Manufacturing Efficiency
SMT processes are highly automated, resulting in increased production efficiency. Automated pick-and-place machines can quickly and accurately position components onto PCBs, minimizing the time and labor needed for assembly.
Faster Production Rates: The automation of the assembly process allows for rapid production cycles, enabling manufacturers to meet high demand with shorter lead times. This speed is essential in industries like consumer electronics, where product life cycles are short and speed-to-market is crucial.
Reduced Labor Costs: With fewer manual assembly tasks, labor costs are significantly minimized. Additionally, the training and onboarding of staff are simplified, as automated systems require less human intervention, allowing manufacturers to allocate resources more efficiently.
4. Cost-Effectiveness
While the initial setup costs for SMT equipment can be high, the long-term savings often outweigh these expenses. The increased production efficiency and reduced material waste contribute to a lower overall cost per unit.
Bulk Production Savings: High-volume production runs lead to significant economies of scale. As manufacturers produce larger quantities of products, the cost per unit decreases, enhancing profitability.
Less Material Waste: The precision of SMT processes reduces material wastage during assembly. This efficiency not only lowers costs but also supports sustainability initiatives by minimizing the environmental impact of production.
5. Reliability and Durability
SMT components are generally more reliable and durable than through-hole components. The solder joints formed during SMT assembly tend to be more resistant to mechanical stress and environmental factors.
Greater Resistance to Vibration: SMT components are less likely to suffer from failures caused by vibration, making them particularly suitable for applications in automotive and aerospace industries, where equipment often endures harsh conditions.
Longer Lifespan: Enhanced reliability results in longer-lasting products, reducing the frequency of repairs and replacements. This durability is essential in mission-critical applications, such as medical devices, where reliability is non-negotiable.
6. Design Flexibility
The use of SMT allows for greater design flexibility, enabling engineers to experiment with innovative layouts and configurations. This flexibility is crucial in the fast-evolving electronics market, where rapid design iterations are often necessary.
Creative Freedom: Designers can explore unconventional layouts and multi-layer designs without the constraints imposed by traditional assembly methods. This freedom fosters innovation, allowing for the development of next-generation products.
Rapid Prototyping: The ability to quickly iterate on designs facilitates faster prototyping, enabling companies to bring products to market more efficiently. This agility is vital for staying competitive in dynamic markets, where consumer preferences can shift rapidly.
7. Environmental Considerations
As sustainability becomes increasingly important, SMT processes can contribute to more environmentally friendly manufacturing practices. The reduced material waste and the potential for using lead-free solder align with growing environmental regulations.
Regulatory Compliance: Companies that prioritize sustainability can better meet environmental regulations such as RoHS (Restriction of Hazardous Substances), which is vital for accessing global markets. Compliance not only avoids potential penalties but also enhances a company’s reputation.
Reduced Energy Consumption: Automated SMT processes often consume less energy than traditional methods, further enhancing their sustainability profile. This reduction in energy use contributes to lower operational costs and a smaller carbon footprint.
Download PDF Brochure @
https://www.marketsandmarkets.com/pdfdownloadNew.asp?id=99662691
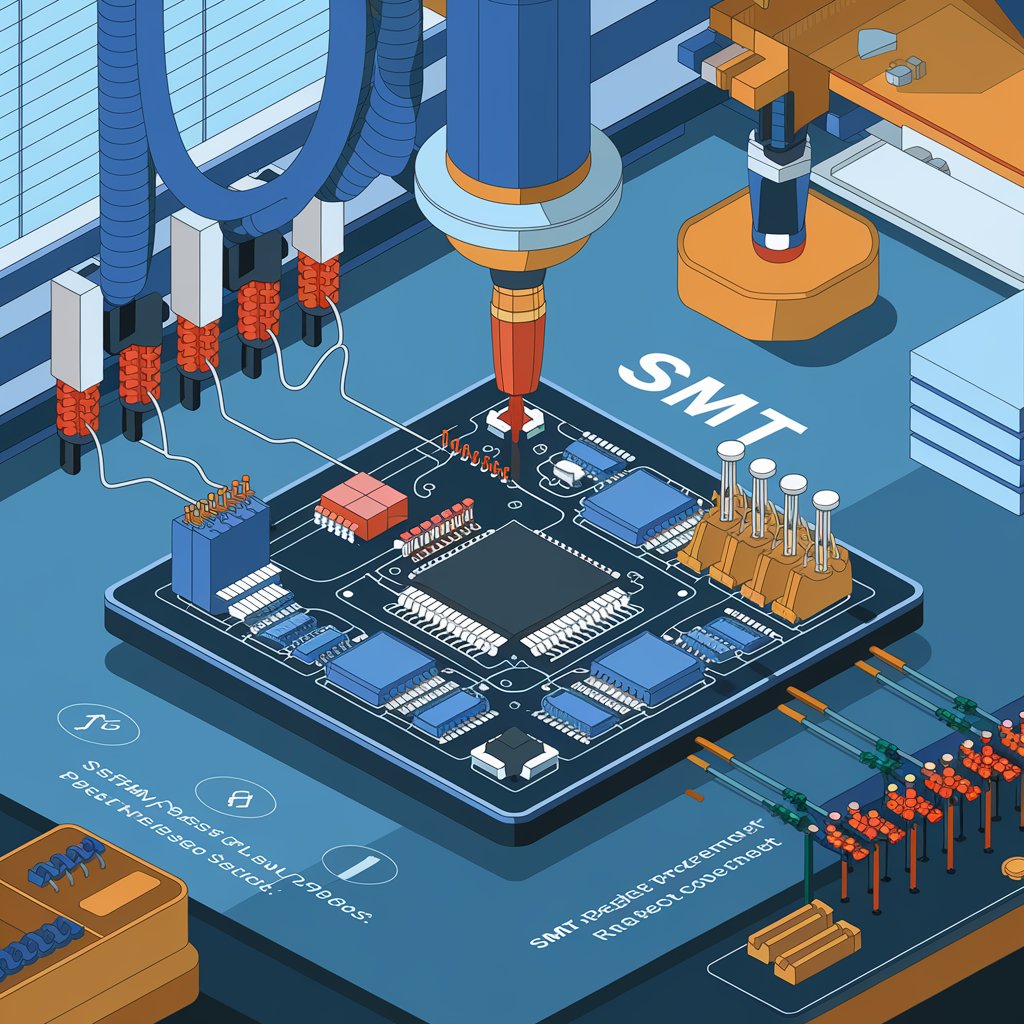
Impact of Industry 4.0 on Surface Mount Technology (SMT)
The introduction of Industry 4.0 has revolutionized various manufacturing sectors, including Surface Mount Technology (SMT). This fourth industrial revolution focuses on the integration of digital technologies, automation, and data exchange, significantly transforming how SMT is approached and executed. Here’s a closer look at the impact of Industry 4.0 on SMT.
Enhanced Automation
One of the most prominent impacts of Industry 4.0 on SMT is the increased level of automation. Advanced robotics and automated assembly systems are now integral to SMT processes, allowing for a more streamlined production line. These automated pick-and-place machines can position components on printed circuit boards (PCBs) with exceptional speed and accuracy, drastically reducing production times. As a result, manufacturers can meet the growing demand for electronic devices more efficiently. Additionally, automation minimizes human error, leading to higher consistency and quality in the assembly processes, which is especially crucial for high-stakes applications.
Data-Driven Decision Making
Industry 4.0 emphasizes the importance of data analytics, and this shift has permeated SMT as well. With real-time data collection and analysis, manufacturers can make informed decisions that enhance operational efficiency. Predictive maintenance becomes feasible, allowing manufacturers to foresee equipment failures and perform maintenance proactively, thus minimizing downtime. Furthermore, real-time monitoring of production metrics enables immediate identification of quality issues, facilitating quick corrective actions and ultimately reducing waste and improving overall product quality.
Integration of IoT Technologies
The Internet of Things (IoT) is a cornerstone of Industry 4.0, and its integration into SMT processes enhances connectivity and operational efficiency. IoT-enabled machines and devices can communicate with one another, providing real-time feedback on production processes. This connectivity supports smart manufacturing practices, where adjustments can be made dynamically based on data insights. Moreover, IoT technologies enable greater supply chain visibility, allowing manufacturers to track components throughout the supply chain and ensure timely delivery, reducing the risk of production delays.
Customization and Flexibility
Industry 4.0 promotes an agile manufacturing environment that allows for rapid customization of products. In SMT, this flexibility is vital as it enables manufacturers to respond swiftly to changing consumer demands. The ability to adapt production lines for different products without significant downtime reduces lead times, which is essential in today’s fast-paced market. Additionally, SMT trends can support mass customization, allowing for small batch sizes tailored to specific customer requirements without sacrificing efficiency.
Sustainability and Resource Efficiency
Sustainability is a key focus of Industry 4.0, and SMT manufacturers are increasingly adopting practices that minimize environmental impact. The use of advanced technologies helps optimize material usage and reduce waste during production. This not only aligns with regulatory compliance but also supports broader sustainability goals. Smart technologies can also monitor energy consumption in real-time, enabling manufacturers to identify inefficiencies and implement measures to conserve energy, further enhancing their sustainability profile.
Workforce Transformation
The implementation of Industry 4.0 in SMT also impacts the workforce. As automation and smart technologies become more prevalent, the skill sets required for employees are evolving. Workers will need to acquire new skills related to operating and maintaining advanced manufacturing technologies. This shift creates opportunities for training and professional development, allowing employees to adapt to the changing landscape. Moreover, with machines taking over routine tasks, the workforce can focus on more strategic roles that require problem-solving and creativity, fostering a more engaged and innovative environment.
The impact of Industry 4.0 on Surface Mount Technology Industry is significant and multifaceted. From enhanced automation and data-driven decision-making to IoT integration and sustainability initiatives, the fourth industrial revolution is reshaping the SMT landscape. Manufacturers who embrace these changes can expect improved efficiency, higher quality products, and a more agile response to market demands. As the industry continues to evolve, the future of SMT will be characterized by smart manufacturing practices that not only optimize production processes but also align with sustainability and innovation goals.
The advantages of using Surface Mount Technology in manufacturing are compelling. From space efficiency and improved performance to enhanced reliability and cost-effectiveness, SMT offers a robust solution for modern electronics production. As the industry continues to evolve, the demand for compact, high-performance devices will only increase, solidifying SMT’s role as a cornerstone of electronics manufacturing. Embracing SMT not only meets current market demands but also prepares manufacturers for the future, where innovation and efficiency will be paramount