Aerospace testing is a critical component of the aerospace industry, ensuring the performance, safety, and reliability of aircraft, spacecraft, and their components. With the increasing complexity of aerospace systems, testing technologies have advanced significantly over the years. Today, state-of-the-art sensors, simulation models, non-destructive testing methods, and data analysis tools are pushing the boundaries of what is possible in aerospace testing. These technologies not only enable more accurate and efficient testing but also contribute to the rapid innovation that defines the aerospace sector.
In this article, we explore the cutting-edge aerospace testing technologies that are transforming the industry, including advanced sensors and measurement systems, computer simulation and modeling, non-destructive testing methods, data analysis and reporting, and automation in aerospace testing.
The global aerospace testing market was valued at USD 5.29 billion in 2024 and is projected to reach USD 6.68 billion by 2029; it is expected to register a CAGR of 4.8% during the forecast period.
Aerospace Testing Technologies Include
1. Advanced Sensors and Measurement Systems
Modern aerospace systems are more complex than ever before, requiring advanced sensor technologies to test and monitor performance accurately. Sensors and measurement systems are essential in aerospace testing to provide real-time data on a wide range of variables, including temperature, pressure, stress, strain, vibration, and acceleration. These sensors help simulate the harsh environments that aircraft and spacecraft experience and are critical in testing everything from engines to structures to electronic systems.
Types of Sensors Used in Aerospace Testing
- Strain Gauges: These are used to measure the deformation or strain of materials in response to applied forces, allowing engineers to evaluate the structural integrity of aircraft and spacecraft components.
- Pressure Sensors: Pressure measurement is critical in aerospace applications, particularly in engine testing, fuel systems, and atmospheric testing. Accurate pressure readings are vital for understanding the performance and safety of these systems under various conditions.
- Accelerometers and Vibration Sensors: These sensors help detect the forces acting on aircraft or spacecraft during flight or in simulated environments. Accelerometers measure changes in velocity (acceleration) that can reveal performance issues or weaknesses in a structure.
- Thermocouples and Temperature Sensors: Aerospace systems must operate in extreme temperatures, and testing ensures they can withstand these conditions. Temperature sensors are critical in evaluating engine performance, material properties, and the thermal stress on components.
- Optical Sensors: Optical sensors, such as fiber-optic sensors, are used to measure strain and temperature without direct electrical contact, making them ideal for high-voltage or radiation-sensitive testing.
Benefits of Advanced Sensors in Aerospace Testing
- Real-Time Monitoring: Sensors allow engineers to collect continuous data in real time, providing valuable insights into the performance and behavior of systems during tests.
- Enhanced Accuracy: With high precision, these sensors provide accurate measurements of key parameters, reducing the margin for error and enhancing the reliability of test results.
- Reduced Risk: Sensors can detect early signs of failure or malfunction, enabling preventative measures and mitigating the risk of catastrophic failure during operations.
2. Computer Simulation and Modeling
As aerospace technology becomes more advanced, testing increasingly involves computer simulation and modeling techniques. Simulation allows engineers to create virtual environments that replicate the conditions and behaviors of physical systems, enabling tests that would be too costly, dangerous, or impractical to perform in real life.
Types of Simulations Used in Aerospace Testing
- Finite Element Analysis (FEA): FEA is a method used to simulate how materials and structures behave under various stresses, forces, and environmental conditions. It helps engineers understand how an aircraft wing, fuselage, or engine component will respond to aerodynamic forces, thermal stress, and vibrational loads.
- Computational Fluid Dynamics (CFD): CFD is used to simulate the airflow around an aircraft or spacecraft, analyzing factors like drag, lift, pressure distribution, and heat transfer. By virtually testing aerodynamic properties, CFD can help optimize designs for greater fuel efficiency and performance.
- Multibody Dynamics (MBD): This simulation tool analyzes how multiple interacting rigid and flexible bodies move in space, providing insights into the behavior of complex systems like landing gear, flight control systems, and mechanical linkages.
Benefits of Simulation and Modeling in Aerospace Testing
- Cost Savings: Computer simulations significantly reduce the need for physical prototypes and extensive field testing, saving both time and resources.
- Increased Accuracy: Simulations allow for more precise predictions of how systems will behave under a variety of conditions, helping to optimize designs and identify potential problems early in the development process.
- Faster Iterations: Engineers can test a wide range of designs and parameters virtually, speeding up the prototyping and testing phases of product development.
3. Non-Destructive Testing Methods
Non-destructive testing (NDT) refers to techniques that allow engineers to assess the integrity of materials or components without damaging or altering their structure. In aerospace, where component reliability is paramount, NDT is widely used for inspecting metal alloys, composite materials, welds, and joints for signs of stress, fatigue, or cracks.
Common NDT Techniques in Aerospace
- Ultrasonic Testing (UT): Ultrasonic waves are used to detect internal flaws such as cracks, voids, or material degradation. UT is commonly used for inspecting aircraft fuselages, engine parts, and turbine blades.
- X-ray and Computed Tomography (CT): These techniques are used to create detailed images of a component’s internal structure. CT scans can provide high-resolution, three-dimensional images, helping detect internal cracks or delaminations in composite materials.
- Magnetic Particle Inspection (MPI): MPI is used for detecting surface and near-surface cracks in ferromagnetic materials. It’s often employed in the inspection of engine components and landing gear.
- Eddy Current Testing (ECT): Eddy current testing uses electromagnetic fields to detect surface and sub-surface defects in conductive materials, commonly used for inspecting aircraft wings and engine parts.
- Dye Penetrant Testing (DPT): This method is used to detect surface-breaking defects, often used on metallic and non-metallic surfaces.
Benefits of Non-Destructive Testing
- Safety Assurance: NDT ensures that components meet safety standards and are free from critical defects that could compromise performance or cause failure.
- Cost-Effective: Unlike destructive testing methods, NDT doesn’t damage components, allowing them to be reused and minimizing material waste.
- Early Detection: NDT can identify small flaws or weaknesses before they become critical issues, enabling early repairs and avoiding costly downtime or catastrophic failures.
Download PDF Brochure @ https://www.marketsandmarkets.com/pdfdownloadNew.asp?id=32924426
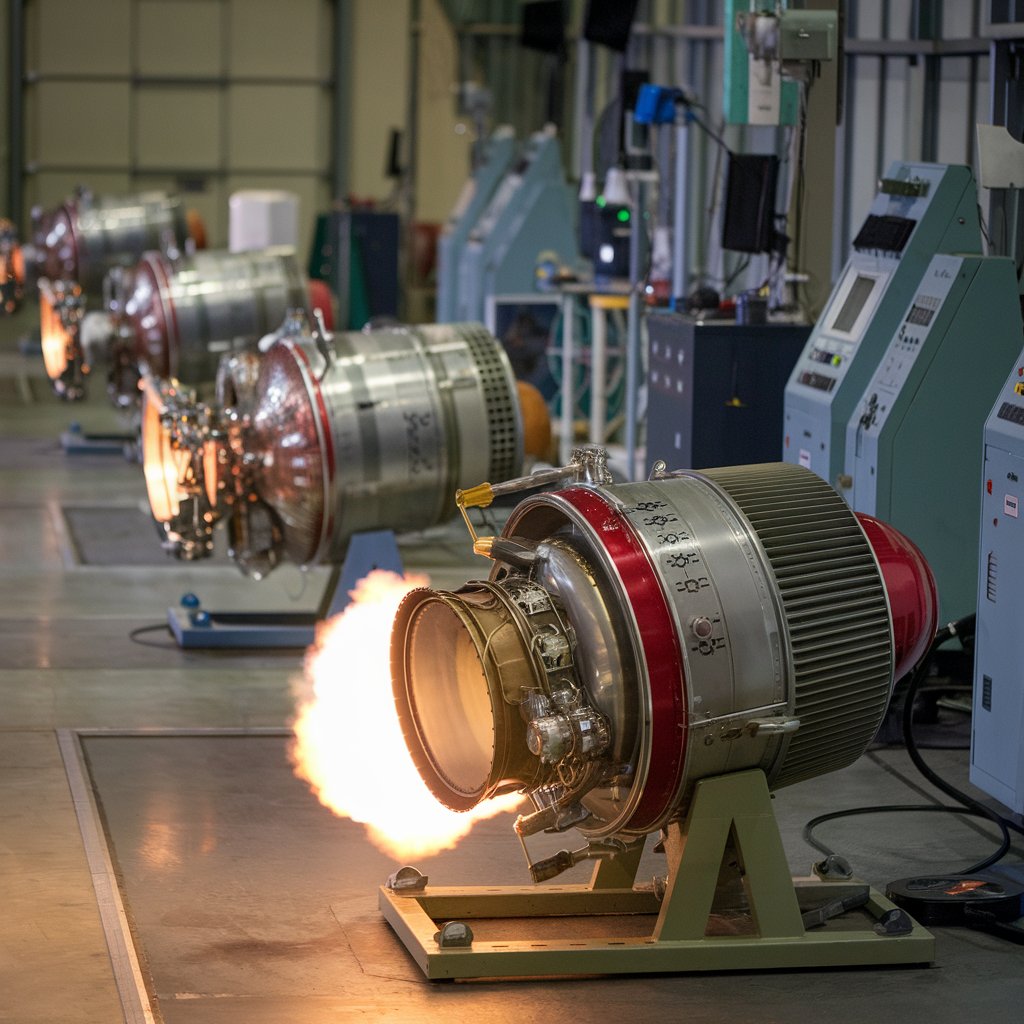
4. Data Analysis and Reporting in Aerospace Testing
In modern aerospace testing, the sheer volume of data collected from sensors, simulations, and NDT procedures can be overwhelming. As a result, data analysis and reporting tools play an increasingly important role in ensuring that engineers and stakeholders can extract actionable insights from complex test data.
Advanced Data Analytics Techniques
- Big Data Analytics: The application of machine learning and artificial intelligence (AI) to analyze large datasets helps to identify trends, predict potential failures, and improve overall testing processes. By analyzing historical test data, engineers can develop predictive models to improve the design and testing of new aerospace systems.
- Data Fusion: Data fusion combines information from multiple sources (e.g., sensor data, simulation models, and NDT results) to provide a more comprehensive view of the performance and condition of aerospace systems.
- Automated Reporting: With sophisticated data processing and visualization tools, test results can be automatically compiled into clear, concise reports, ensuring that decision-makers have accurate information at their fingertips.
Benefits of Data Analysis in Aerospace Testing
- Improved Decision-Making: Advanced data analysis helps engineers make informed decisions based on accurate, real-time insights into system performance.
- Optimized Testing: By analyzing past test data, aerospace manufacturers can refine testing strategies, reduce unnecessary tests, and improve testing efficiency.
- Predictive Maintenance: By analyzing trends and patterns in test data, predictive maintenance models can be developed, helping predict potential issues before they occur and reducing unexpected failures.
5. Automation in Aerospace Testing
The aerospace testing industry is increasingly embracing automation in testing to improve accuracy, speed, and consistency. Automated systems can perform repetitive testing tasks, process large amounts of data, and ensure high-quality results with minimal human intervention.
Examples of Automation in Aerospace Testing
- Automated Test Benches: These systems automatically conduct tests on various components, such as engines and avionics, without requiring constant human oversight. They ensure that components are tested under the same conditions each time, improving consistency and reliability.
- Robotic Systems: In aerospace NDT, robots equipped with sensors and imaging equipment can perform inspections in hard-to-reach areas, such as aircraft wings or turbine blades, without the need for human intervention.
- Automated Data Collection and Analysis: Automated systems can continuously monitor and record test data, reducing human error and enabling faster data processing and analysis.
Benefits of Automation in Aerospace Testing
- Increased Efficiency: Automation speeds up testing processes, allowing more tests to be performed in less time.
- Reduced Human Error: Automation minimizes the potential for errors during testing, ensuring that results are accurate and consistent.
- Cost Reduction: Automated testing systems can operate around the clock, leading to faster turnaround times and reduced labor costs.
Aerospace testing technologies are evolving rapidly, incorporating advanced sensors, computer simulations, non-destructive testing methods, data analytics
Major Aerospace Testing companies include:
- Element Materials Technology (UK)
- SGS SA (Switzerland)
- Intertek Group plc (UK)
- Applus+ (Spain)
- TÜV SÜD (Germany)
- TÜV Rheinland (Germany)
- TÜV NORD Group (Germany)
- Rohde & Schwarz (Germany)
- Eurofins Scientific (Luxembourg)
- The Boeing Company (US)
- Airbus (Netherlands)
- MISTRAS Group (US)
- Lockheed Martin Corporation (US)
- Bureau Veritas (France)
- DEKRA (Germany)
1. What is aerospace testing and why is it important?
Aerospace testing involves evaluating the safety, performance, and reliability of aircraft, spacecraft, and their components. It includes tests for structural integrity, system functionality, environmental durability, and more. Testing is critical to ensure that aerospace systems can perform as intended under extreme conditions, avoid catastrophic failures, meet safety standards, and comply with regulatory requirements.
2. What are the different types of aerospace testing technologies?
Aerospace testing technologies include a range of techniques that provide crucial data for system performance, safety, and durability. Some of the most Importance of Aerospace Testing include:
- Advanced Sensors and Measurement Systems: Devices that measure variables like strain, temperature, pressure, and vibration in real-time.
- Computer Simulation and Modeling: Virtual tools such as Finite Element Analysis (FEA), Computational Fluid Dynamics (CFD), and Multibody Dynamics (MBD) that simulate how systems will behave under various conditions.
- Non-Destructive Testing (NDT): Methods like ultrasonic testing, x-ray inspection, magnetic particle testing, and eddy current testing that allow engineers to detect defects in materials without damaging them.
- Data Analysis and Reporting: Advanced analytics, machine learning, and automated reporting tools that help process and interpret vast amounts of test data.
- Automation in Testing: Automated systems for testing, data collection, and analysis, improving speed, consistency, and accuracy in aerospace testing.
3. How do advanced sensors enhance aerospace testing?
Advanced sensors play a critical role in aerospace testing by enabling real-time monitoring of various physical properties such as strain, temperature, pressure, and vibration. These sensors provide accurate data that helps engineers assess the performance and durability of components during tests. They ensure that aerospace systems can handle extreme environmental conditions like high altitudes, rapid acceleration, and temperature fluctuations, ultimately improving system safety and performance.
4. What is the role of computer simulation in aerospace testing?
Computer simulation allows aerospace engineers to model complex systems and test how they will behave under different conditions without physical prototypes. Techniques like Finite Element Analysis (FEA) and Computational Fluid Dynamics (CFD) simulate real-world forces on structures and airflow around aircraft, respectively. Simulation saves both time and money by reducing the need for physical prototypes and by helping engineers refine designs before physical testing, ultimately improving performance and reducing risks.
5. How does non-destructive testing (NDT) work?
Non-destructive testing (NDT) involves techniques that inspect and evaluate the condition of materials or components without causing any damage. For example:
- Ultrasonic Testing (UT) uses sound waves to detect internal flaws such as cracks in metal or composite materials.
- X-ray and CT Scanning provide detailed images of the internal structure of components, helping identify hidden defects.
- Magnetic Particle Inspection (MPI) detects surface or near-surface cracks in ferromagnetic materials.
NDT is essential in ensuring that critical components, like turbine blades, engine parts, and aircraft fuselages, meet safety standards without being damaged during the testing process.