The global Collaborative Robots (Cobots) Industry is at a transformative juncture, marked by unprecedented technological advancements and increasing adoption across industries. Once seen as a niche solution, collaborative robots are now playing a pivotal role in modernizing manufacturing, logistics, healthcare, and beyond. With the integration of cutting-edge technologies like Artificial Intelligence (AI), enhanced safety features, and greater flexibility in their operations, cobots are revolutionizing how businesses approach automation and human-robot collaboration.
In this article, we will explore the latest trends and technological advancements driving the global collaborative robots industry, particularly how AI, safety innovations, and flexible solutions are shaping the future of industrial automation.
The Rise of Collaborative Robots
Collaborative robots are designed to work alongside human operators in shared workspaces, performing tasks such as assembly, inspection, material handling, and packaging. Unlike traditional industrial robots, which often require barriers or cages for safety, cobots are specifically designed to collaborate with humans safely, allowing for a more dynamic and efficient workflow.
The demand for collaborative robots has surged over the past decade, driven by the need for more flexible, cost-effective, and adaptable automation solutions. As industries move toward Industry 4.0, cobots have become key enablers of smarter, more agile production systems.
According to a report , The Global Collaborative Robot industry size is projected to grow from USD 1.9 billion in 2024 and is estimated to reach USD 11.8 billion by 2030; it is expected to grow at a Compound Annual Growth Rate (CAGR) of 35.2% from 2024 to 2030. The growth of the Collaborative Robot industry is driven by higher return on investment than traditional industrial robotic systems; increased demand in e-commerce and logistics sectors; significant benefits in businesses of all sizes; easy programming of cobots
AI-Driven Advancements in Collaborative Robots
One of the most significant technological breakthroughs driving the growth of collaborative robots is the integration of Artificial Intelligence (AI). AI-enabled cobots are more than just robotic arms performing repetitive tasks; they are becoming smarter, more adaptable, and capable of learning from their environment.
1. AI-Powered Vision Systems: Enhancing Precision and Flexibility
AI-driven vision systems are revolutionizing how cobots interact with their environment. With AI-enhanced cameras and sensors, cobots can identify and manipulate objects with precision, even in unstructured environments. For instance, cobots are now capable of performing complex tasks such as quality inspection and pick-and-place operations, where they can visually identify defects in products or adapt to changes in the layout of an assembly line. This level of precision allows cobots to carry out tasks that previously required human expertise, improving accuracy while reducing the risk of errors.
Moreover, AI enables cobots to adapt in real-time to different scenarios, learning from their experiences to enhance operational efficiency. Whether it’s adjusting for variations in product sizes or modifying actions based on feedback from sensors, AI-powered cobots can ensure continuous optimization of production processes.
2. Machine Learning for Autonomous Decision Making
Machine learning algorithms are enabling cobots to make decisions on their own, based on historical data and real-time inputs. For instance, in packaging operations, a cobot can analyze data on production rates, environmental conditions, and inventory levels, making autonomous decisions to optimize workflow and energy usage. This capacity for autonomous decision-making is crucial for industries with dynamic production needs, such as electronics and consumer goods manufacturing.
Safety Innovations Driving Cobot Adoption
One of the key factors in the rapid adoption of collaborative robots is the continuous improvement in their safety features. Traditional industrial robots typically require safety cages or barriers to protect human workers, which can impede workflow efficiency. Cobots, on the other hand, are specifically designed to operate safely in close proximity to human operators, eliminating the need for physical barriers and enabling smoother human-robot collaboration.
1. Force-Limiting Technology: Ensuring Safe Interaction
Collaborative robots are equipped with force-limiting technology that ensures that they stop or slow down if they come into contact with a human worker. This is especially important in applications where the robot and the human are working in the same space, such as in assembly lines or logistics operations. By automatically adjusting the robot’s speed or stopping completely when a force threshold is exceeded, the risk of injury to human workers is significantly reduced.
2. Advanced Sensors and Vision Systems
AI-powered sensors and vision systems also play a crucial role in improving cobot safety. These systems allow cobots to detect the presence of human workers, objects, and obstacles in real-time, adjusting their movements accordingly. For example, in a warehouse, a cobot can recognize the presence of a worker and adjust its path to avoid a collision. This level of real-time interaction ensures that cobots can work safely in environments where humans and machines share space.
3. Compliance with International Safety Standards
As the cobot market expands, safety standards have become a critical focus. Many cobots now comply with international safety standards such as ISO/TS 15066, which specifically addresses the safety requirements for collaborative robots. Compliance with such standards ensures that cobots can be safely integrated into a variety of industries, boosting their widespread adoption across diverse sectors.
Download PDF Brochure @ https://www.marketsandmarkets.com/pdfdownloadNew.asp?id=194541294
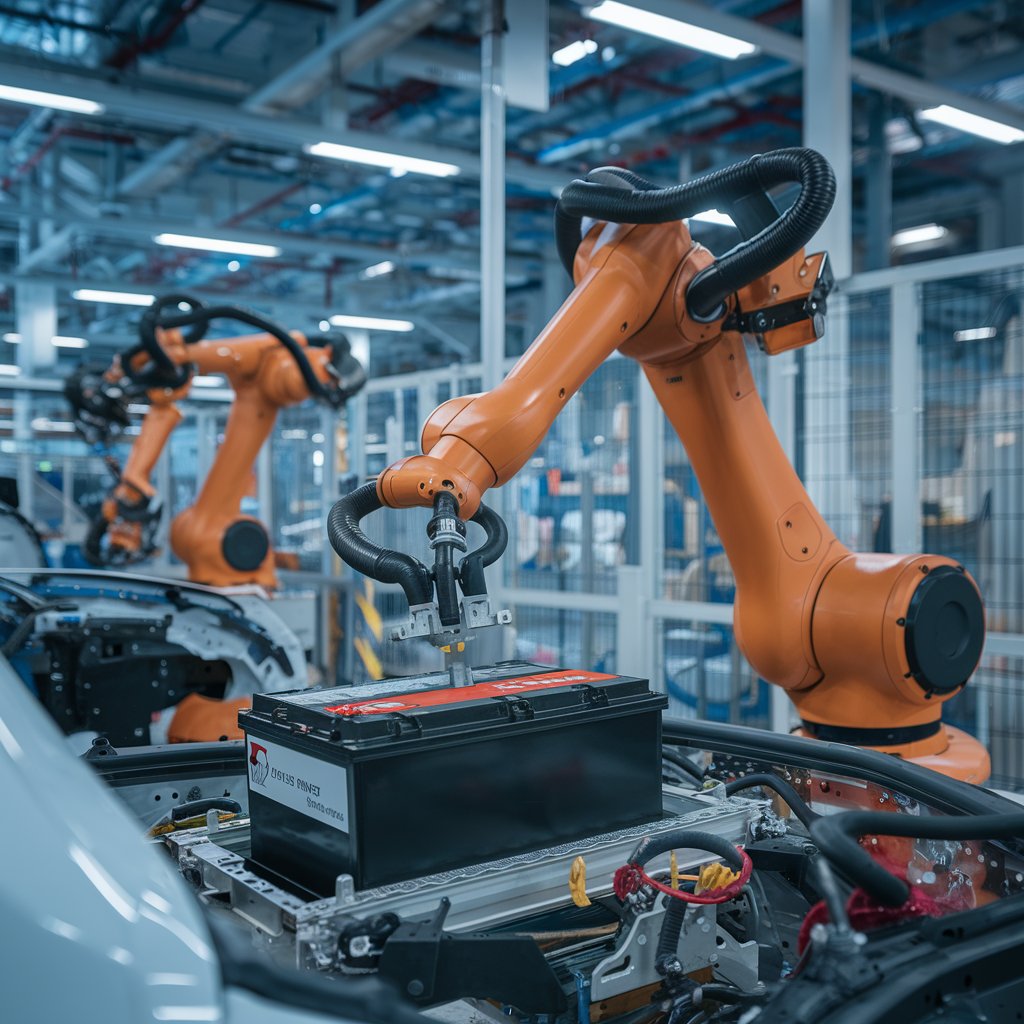
Flexibility in Application: The Key Advantage of Cobots
Flexibility is one of the primary reasons why collaborative robots are gaining traction in the global market. Unlike traditional industrial robots, which are often fixed in one location and designed for a specific task, cobots are mobile, easy to reprogram, and can perform a wide range of applications.
1. Easy Integration into Existing Workflows
One of the key selling points of cobots is their ability to integrate seamlessly into existing production lines without requiring major changes to the layout or equipment. This is particularly valuable for small and medium-sized enterprises (SMEs) that may not have the resources to invest in extensive infrastructure changes. Cobots can be quickly reprogrammed or reconfigured to perform different tasks, allowing businesses to adapt to changing market demands or production schedules with ease.
2. Customizable for a Wide Range of Industries
Cobots are incredibly versatile, making them suitable for a broad spectrum of industries, from automotive manufacturing to electronics assembly, pharmaceutical production, and food processing. Their ability to perform various tasks—such as assembly, inspection, material handling, and packaging—means that businesses across sectors can benefit from cobot deployment.
For example, in the automotive industry, cobots are being used to assist with welding, painting, and assembly tasks, reducing the need for human workers to perform repetitive or hazardous activities. In electronics manufacturing, cobots are utilized for delicate assembly processes, such as placing tiny components onto circuit boards with extreme precision.
3. Scalability for Future Growth
The modular design of cobots allows companies to scale their automation systems as needed. Whether it’s adding more robots to an assembly line or switching out existing tasks for new ones, cobots offer the flexibility to scale up or down according to production requirements. This scalability is essential for businesses aiming to grow or adapt quickly to market demands.
The Future of Collaborative Robots
The global collaborative robots industry is poised for continued growth, fueled by advancements in AI, safety innovations, and flexibility in automation. As cobots become smarter, safer, and more adaptable, they will continue to unlock new opportunities for businesses across a variety of sectors. The increasing demand for cost-effective, scalable automation solutions is positioning cobots as a cornerstone of the future of manufacturing and beyond.
As companies strive to enhance productivity, improve worker safety, and meet ever-changing market demands, collaborative robots will undoubtedly play a key role in shaping the future of automation. The ongoing evolution of cobots, along with their ability to integrate seamlessly into human work environments, makes them a transformative force in the global industrial landscape.
With continued innovation in AI, safety, and flexibility, the cobot market is expected to expand rapidly, offering businesses new ways to optimize their operations and stay competitive in an increasingly automated world.
Key companies operating in the Collaborative Robot companies are Universal Robots A/S (Denmark), FANUC CORPORATION (Japan), ABB (Switzerland), TECHMAN ROBOT INC. (Taiwan), and AUBO (BEIJING) ROBOTICS TECHNOLOGY CO., LTD (China), KUKA AG (Germany), Doosan Robotics Inc. (South Korea), Denso Corporation (South Korea), YASKAWA ELECTRIC CORPORATION (Japan), Rethink Robotics GmBH (Germany) among others.
Frequently Asked Questions (FAQ) about the Global Collaborative Robots Industry
1. What are collaborative robots (cobots)?
Collaborative robots, or cobots, are robots designed to work alongside humans in shared workspaces. Unlike traditional industrial robots, cobots are equipped with advanced sensors and safety features that allow them to operate safely in close proximity to human workers, without the need for barriers or cages.
2. How do collaborative robots differ from traditional robots?
The key difference between cobots and traditional industrial robots lies in their design and functionality. Cobots are built for collaboration with humans, making them more flexible, easy to program, and safe to interact with. Traditional robots, on the other hand, are often stationary, require safety barriers, and are typically designed for high-volume, repetitive tasks in isolated environments.
3. What industries are adopting collaborative robots?
Collaborative robots are being adopted across a wide range of industries, including:
- Manufacturing (automotive, electronics, consumer goods)
- Logistics and warehousing
- Healthcare (for surgery, patient care, etc.)
- Pharmaceuticals and food processing
- Agriculture and research
- Education and training
Their versatility allows them to perform tasks such as assembly, inspection, packaging, and material handling across various sectors.
4. What are the benefits of using collaborative robots in manufacturing?
Some of the key benefits of cobots in manufacturing include:
- Increased productivity: Cobots can perform repetitive tasks with high precision, increasing overall output.
- Improved safety: Cobots are designed to work alongside human workers, reducing the need for physical barriers and enhancing workplace safety.
- Cost-effectiveness: Cobots are generally more affordable than traditional robots, offering a faster return on investment (ROI).
- Flexibility: Cobots can be easily reprogrammed and deployed in different tasks, making them suitable for dynamic production environments.
- Enhanced worker satisfaction: By offloading repetitive and physically demanding tasks, cobots allow human workers to focus on more complex and creative jobs.
5. How are AI and machine learning integrated into collaborative robots?
AI and machine learning enhance cobots by enabling them to:
- Adapt to changing environments: With AI-powered vision systems, cobots can identify and manipulate objects with precision, even in unstructured environments.
- Make autonomous decisions: Machine learning algorithms allow cobots to learn from their experiences and optimize their actions, improving efficiency and productivity.
- Recognize and correct errors: AI allows cobots to detect faults or issues in their actions and make real-time corrections, minimizing errors in production processes.
6. Are collaborative robots safe to use around humans?
Yes, cobots are specifically designed with safety in mind. They come equipped with advanced sensors, vision systems, and force-limiting technologies that help ensure safe interaction with humans. If a cobot detects a force greater than a certain threshold, it automatically slows down or stops, reducing the risk of injury to human workers.
Additionally, cobots comply with safety standards such as ISO/TS 15066, ensuring that they meet international safety guidelines for human-robot collaboration.
7. How easy is it to integrate collaborative robots into existing production lines?
One of the main advantages of cobots is their ease of integration into existing production lines. Cobots are highly flexible and can be quickly programmed to perform a variety of tasks. They do not require extensive reengineering of existing infrastructure, making them ideal for small and medium-sized businesses (SMEs) that want to adopt automation without a large upfront investment.
8. What is the future outlook for the global collaborative robots market?
The global collaborative robots market is expected to experience significant growth over the next decade. Driven by advancements in AI, machine learning, and robotics technology, cobots are becoming more adaptable, cost-effective, and capable of performing a broader range of tasks. The demand for cobots will continue to rise across industries such as manufacturing, logistics, healthcare, and more, as companies seek to improve productivity, reduce labor costs, and ensure workplace safety.