As the manufacturing world continues to evolve, the next phase in industrial advancement is upon us: Industry 5.0. Building on the automation and connectivity of Industry 4.0, Industry 5.0 introduces a new paradigm focused on the collaboration between humans and machines. This innovative approach enhances productivity, creativity, and sustainability by combining the precision of advanced technologies with the ingenuity and decision-making abilities of human workers.
Explore the key Industry 5.0 technologies driving the transformation across industries, from manufacturing to aerospace, automotive, and healthcare. These technologies not only improve operational efficiency but also enable manufacturers to create highly personalized products, adapt quickly to market demands, and embrace sustainable practices.
The global industry 5.0 Industry is expected to be valued at USD 65.8 billion in 2024 and is projected to reach USD 255.7 billion by 2029; it is expected to grow at a CAGR of 31.2 % from 2024 to 2029. Several factors are propelling the growth of the Industry 5.0 Industry across diverse industries, including rapid technological advancements in artificial intelligence, robotics, the Internet of Things (IoT), and industrial 3d printing. This evolution responds to the increasing demand for customized products and personalized experiences, fostering a human-centric approach to manufacturing that empowers workers with advanced tools and technologies
1. Collaborative Robots (Cobots)
One of the cornerstones of Industry 5.0 is the introduction of collaborative robots (or cobots). Unlike traditional robots, which typically operate independently or in isolated environments, cobots are designed to work alongside humans in a shared workspace. Cobots are safe, flexible, and easy to program, allowing human operators to focus on tasks that require creativity and problem-solving, while the robots handle repetitive, physically demanding, or hazardous activities.
In manufacturing settings, cobots assist in tasks like assembly, packaging, quality control, and material handling. By working alongside workers, they increase efficiency and reduce the risk of workplace injuries. Cobots can easily adapt to different roles and are valuable in high-mix, low-volume production environments, where flexibility is key.
2. Artificial Intelligence (AI) and Machine Learning
Artificial Intelligence (AI) and Machine Learning (ML) are at the heart of Industry 5.0, enabling machines and systems to make smarter, real-time decisions that were once only possible with human intervention. These technologies improve data analytics, predictive maintenance, process optimization, and decision-making.
- Predictive Maintenance: AI algorithms analyze equipment data and predict failures before they occur, minimizing downtime and reducing costly repairs. This improves overall equipment effectiveness (OEE) and extends the lifespan of machinery.
- AI-Driven Quality Control: AI-powered visual inspection systems can identify defects in products faster and more accurately than human inspectors, ensuring higher product quality and reducing the cost of rework.
- Product Design and Customization: AI and ML also enable mass customization, allowing manufacturers to create highly personalized products. AI-driven design tools can rapidly adapt product specifications, incorporating customer preferences into the production process without compromising efficiency.
3. Internet of Things (IoT) and Smart Sensors
The Internet of Things (IoT) connects devices, machines, and products in a network, allowing for seamless communication and data exchange. In Industry 5.0, IoT is a key enabler for real-time monitoring, asset management, and enhanced decision-making.
- Smart Sensors: These sensors monitor various parameters, such as temperature, pressure, vibration, and humidity, and transmit data to central systems for analysis. In manufacturing, smart sensors help monitor equipment health, detect anomalies, and ensure that machines operate at optimal levels.
- Real-Time Data Analytics: By gathering data from connected devices, IoT systems enable manufacturers to make real-time decisions that improve production efficiency, reduce waste, and enhance product quality. IoT-enabled systems also play a crucial role in inventory management, optimizing stock levels and minimizing the need for manual intervention.
- Digital Twins: IoT data is also used to create digital twins—virtual representations of physical assets or production lines. These digital twins allow manufacturers to simulate and analyze processes, identify inefficiencies, and predict future outcomes. The result is more accurate forecasting and improved operational performance.
Download PDF Brochure @
https://www.marketsandmarkets.com/pdfdownloadNew.asp?id=35376359
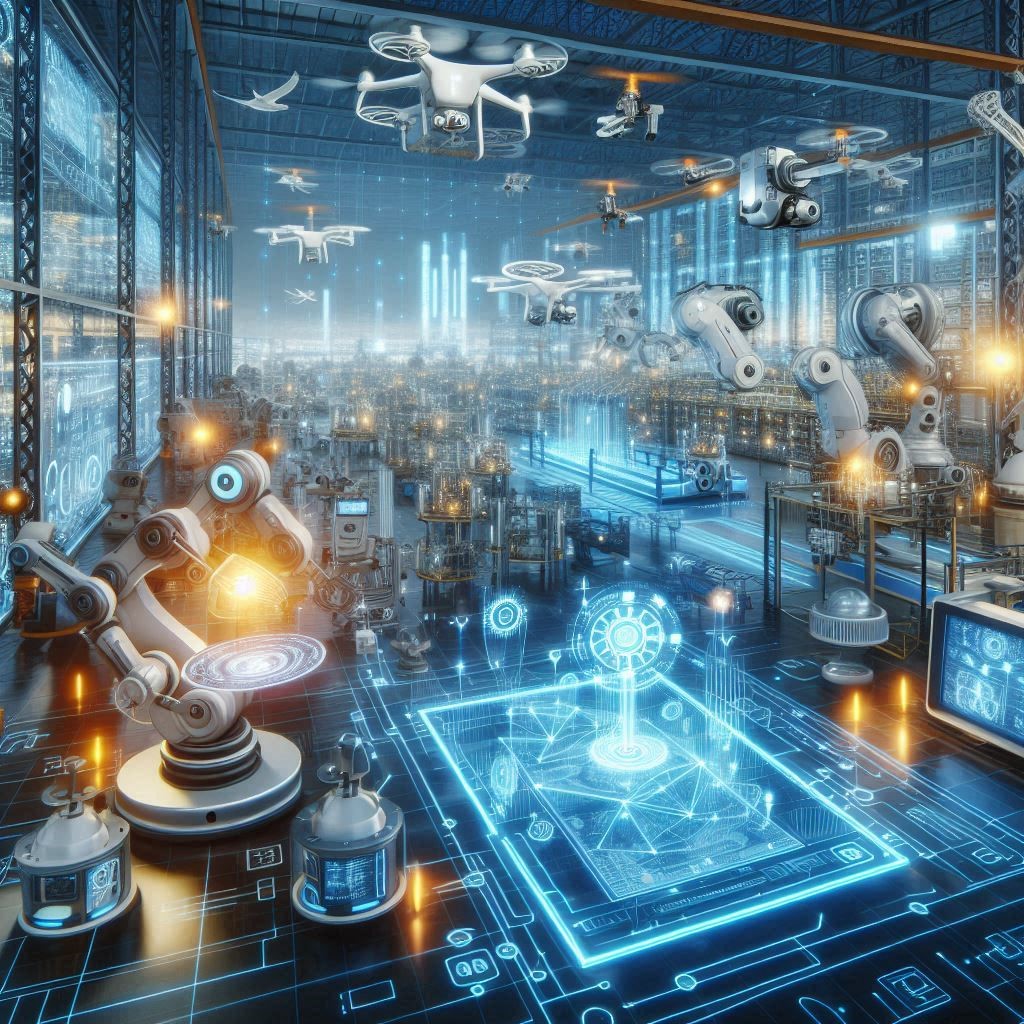
4. 3D Printing and Additive Manufacturing
3D printing (or additive manufacturing) is a revolutionary technology that allows for the creation of complex, customized parts layer by layer. Industry 5.0 leverages 3D printing to achieve mass customization at scale, enabling manufacturers to quickly produce bespoke products without the need for expensive tooling or retooling.
- Rapid Prototyping: 3D printing accelerates product development by allowing for faster prototyping. Manufacturers can test and refine designs before moving to full-scale production, reducing development time and cost.
- On-Demand Production: 3D printing enables on-demand production of spare parts and components, reducing lead times and inventory costs. This is especially valuable in industries like aerospace and automotive, where parts often have long lead times.
- Sustainability: Additive manufacturing is more material-efficient than traditional methods, as it minimizes waste by using only the material needed for each part. Additionally, it allows for the use of recycled materials, further contributing to sustainability.
5. Edge Computing
Edge computing is another pivotal technology within Industry 5.0. It involves processing data closer to the source (i.e., on the factory floor or at the device level) rather than relying on centralized cloud computing systems. This reduces latency and improves the speed of decision-making, making it especially useful in time-sensitive manufacturing operations.
- Real-Time Decision Making: With edge computing, data is analyzed in real-time, allowing machines and operators to respond instantly to changes in the production environment. For instance, edge computing can be used to adjust machine settings or halt production if anomalies are detected.
- Data Security: Edge computing also improves data security by keeping sensitive information within localized systems, reducing the risk of cyberattacks that target centralized cloud platforms.
- Cost Efficiency: By processing data at the edge, companies can reduce the bandwidth required for data transmission and minimize cloud storage costs.
6. 5G Connectivity
The introduction of 5G technology is set to revolutionize Industry 5.0 by providing high-speed, low-latency connectivity. With the ability to transmit vast amounts of data in real-time, 5G supports the seamless integration of IoT devices, enabling faster communication between machines, sensors, and systems.
- Faster Data Transmission: 5G allows for the quick transfer of large datasets, which is essential for real-time analytics and remote monitoring in industrial environments.
- Enhanced Remote Operations: 5G enables remote control of machines and robots, improving safety and enabling operations in hazardous environments without putting workers at risk.
- Smart Factories: 5G supports the creation of smart factories where machines, robots, and humans can work in perfect synchronization. With enhanced connectivity, these factories can quickly adapt to changing conditions and market demands.
7. Augmented Reality (AR) and Virtual Reality (VR)
Augmented Reality (AR) and Virtual Reality (VR) are transforming training, maintenance, and design processes in Industry 5.0. These technologies immerse users in virtual environments, providing real-time guidance and simulations that improve performance and decision-making.
- Training and Simulation: AR and VR enable workers to simulate complex tasks or environments before performing them in the real world, reducing errors and enhancing safety. This is particularly useful in industries like aerospace and automotive, where precision is critical.
- Remote Assistance: AR can be used for remote assistance, where an expert can guide a technician through repairs or complex tasks by overlaying digital information onto the physical world. This reduces downtime and enhances the quality of service.
- Design and Prototyping: VR allows manufacturers to visualize and interact with 3D models of products or production lines, enabling them to make design improvements before committing to physical prototypes.
North America Industry 5.0, particularly the United States and Canada, is at the forefront of Industry 5.0 technologies, driven by a robust manufacturing sector and strong technology ecosystem. The region’s focus on innovation, automation, and sustainability has spurred widespread adoption of technologies such as collaborative robots (cobots), AI, IoT, and edge computing.
The Future of Industry 5.0 Technologies
The technologies that define Industry 5.0 are revolutionizing the manufacturing sector by fostering greater collaboration between humans and machines. These innovations not only improve productivity and efficiency but also empower workers to focus on higher-value tasks, making manufacturing processes more agile, sustainable, and personalized.
As Industry 5.0 technologies continue to mature, they will reshape industries across the globe, from automotive and aerospace to healthcare and electronics. The future of manufacturing is human-centric, and Industry 5.0 is at the forefront of this exciting transformation