The compressed air filter and dryer industry in North America plays a pivotal role in ensuring the efficiency, reliability, and quality of compressed air systems across various industries. From manufacturing plants to food and beverage processing facilities, compressed air systems are integral to numerous operations. As a result, the demand for high-quality compressed air filters and dryers has surged, leading to significant growth in the industry. With innovations in technology and an increasing focus on energy efficiency, the North American market is poised for further expansion. This article explores the key growth drivers, emerging trends, and innovations shaping the compressed air filter and dryer industry in North America.
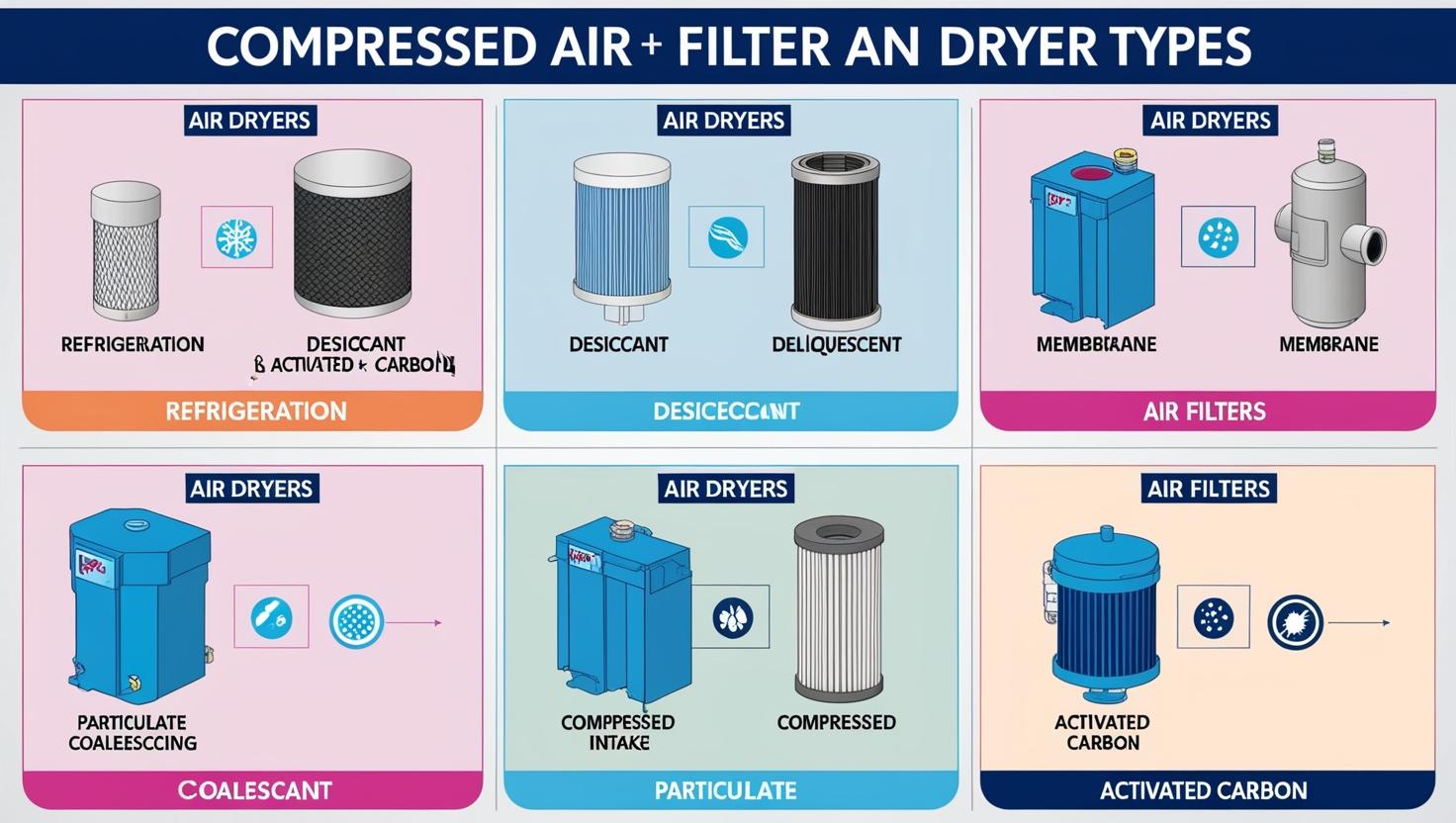
Understanding Compressed Air Filters and Dryers
Before diving into the industry trends and innovations, it’s important to understand the core functions of compressed air filters and dryers.
-
Compressed air filters are designed to remove contaminants like dirt, dust, water, and oil from the air before it enters pneumatic equipment. These filters ensure that compressed air remains clean and free from particles that could damage machinery or compromise product quality.
-
Compressed air dryers are essential for removing moisture from the compressed air, preventing the formation of water droplets, which can lead to corrosion, freezing, and equipment failure. Air dryers use technologies like refrigeration or desiccant materials to dry the air before it is sent through the system.
Together, these components help to maintain the optimal performance and lifespan of compressed air systems, reduce energy consumption, and ensure the safety and efficiency of industrial operations.
Download PDF Brochure @
https://www.marketsandmarkets.com/pdfdownloadNew.asp?id=132465753
Key Growth Drivers of the North American Market
- Increased Demand for Energy Efficiency and Sustainability
With rising energy costs and a growing emphasis on sustainability, industries across North America are increasingly focusing on energy-efficient solutions. Compressed air systems are known to be one of the most energy-intensive operations within industrial facilities. As a result, businesses are looking to invest in advanced compressed air filters and dryers that minimize energy consumption while maintaining optimal air quality. Innovations such as smart monitoring systems and variable-speed drives for air compressors are helping companies reduce their overall energy usage, making energy-efficient filters and dryers more in demand.
- Expansion of Manufacturing and Industrial Automation
The continued expansion of manufacturing facilities and the rise of industrial automation in North America have significantly boosted the demand for compressed air systems. As manufacturers adopt more automated systems that rely on compressed air for operations such as assembly, packaging, and robotics, the need for clean and dry compressed air becomes even more critical. As industries evolve, especially in sectors like automotive, electronics, and food and beverage, the demand for high-performance air filters and dryers is also increasing.
- Strict Regulatory Standards and Quality Control
In North America, industries such as pharmaceuticals, food processing, and electronics manufacturing are subject to stringent regulatory standards. These industries require high-quality compressed air systems to meet specific cleanliness and dryness standards. For instance, in the food and beverage sector, contamination risks from moisture and particulates can severely impact product quality, making compressed air filters and dryers essential for compliance. As regulations continue to tighten, businesses are investing in state-of-the-art filtration and drying technologies to ensure compliance with industry standards and avoid costly fines.
- Growing Adoption of Renewable Energy Technologies
With an increasing focus on renewable energy and green technology, many industries are turning to compressed air systems that integrate with solar, wind, and other renewable energy sources. These systems demand high-quality air filters and dryers to ensure efficient operation in environmentally-conscious facilities. The push towards cleaner energy solutions is driving the demand for energy-efficient compressed air solutions.
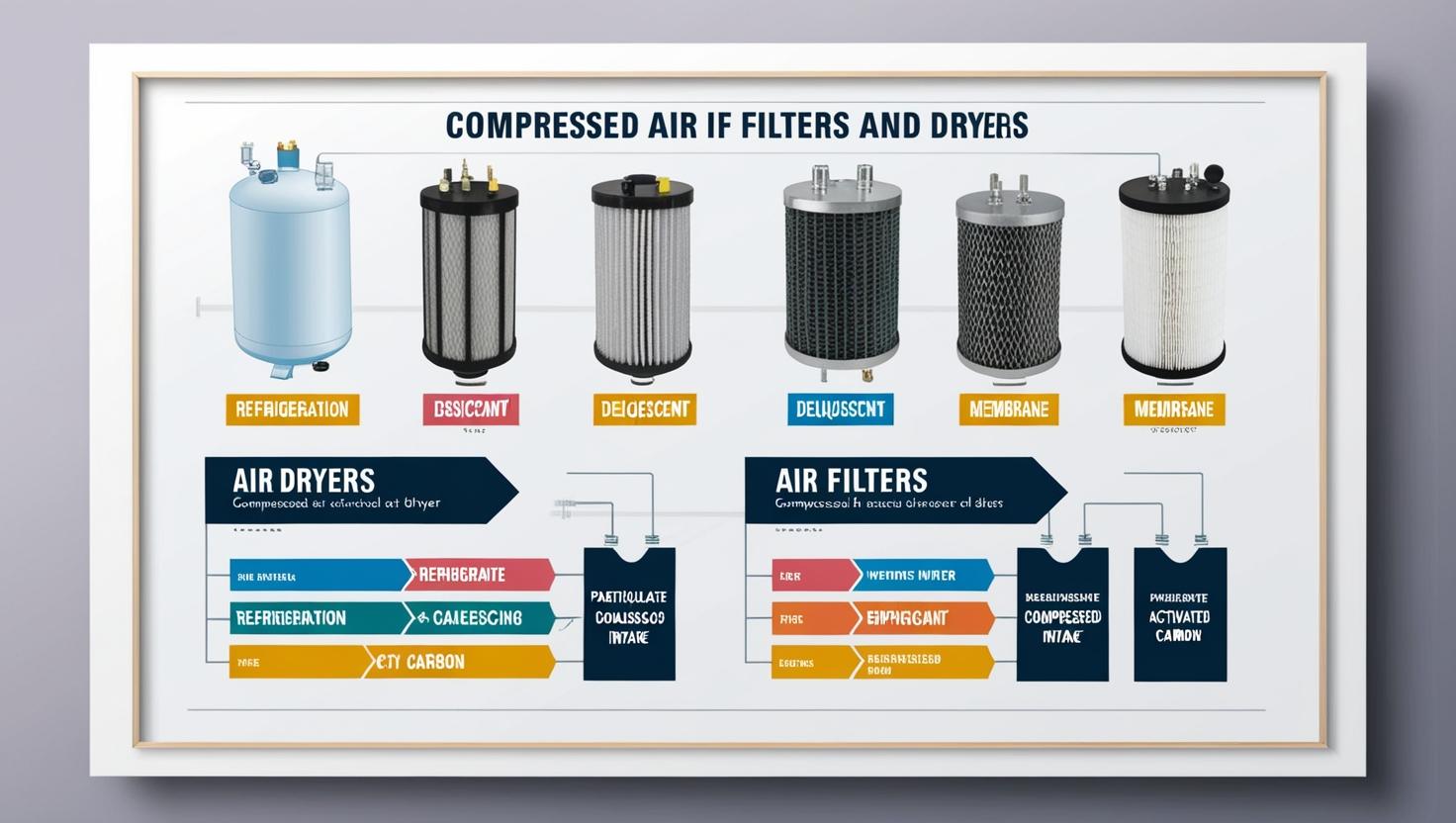
Key Trends in the North American Compressed Air Filter and Dryer Industry
- Shift Toward IoT-Enabled and Smart Systems
One of the most exciting trends in the compressed air filter and dryer market is the integration of Internet of Things (IoT) technology. Smart compressed air systems equipped with IoT sensors are gaining traction in the North American market. These sensors enable real-time monitoring of air quality, pressure, temperature, and humidity, allowing businesses to detect potential issues before they become costly problems. Predictive maintenance and remote monitoring capabilities are also improving system uptime and reducing the need for on-site personnel.
- Growth of Energy-Efficient and Environmentally-Friendly Technologies
The growing emphasis on sustainability is driving innovations in energy-efficient and environmentally-friendly compressed air dryers and filters. Manufacturers are developing products that use less energy, consume fewer resources, and have a lower environmental footprint. For example, refrigerated air dryers are being designed with energy-saving features like heat recovery systems, which can repurpose waste heat to reduce overall energy consumption. Additionally, there is increasing adoption of desiccant dryers, which can operate efficiently at lower temperatures and help save energy in applications requiring ultra-dry air.
- Customization and Modular Solutions
As industries become more specialized, the demand for customized and modular solutions is on the rise. Businesses are looking for compressed air systems that can be tailored to their specific needs. Whether it’s adjusting filtration levels or customizing the size and capacity of air dryers, manufacturers are increasingly offering modular systems that allow for flexibility and scalability. These systems can be easily upgraded or expanded as businesses grow, ensuring that companies can adapt to changing demands without overhauling their entire compressed air infrastructure.
- Advancements in Desiccant Dryer Technology
Desiccant air dryers are increasingly becoming the preferred choice for industries requiring high-quality, moisture-free compressed air. These dryers use a desiccant material to absorb moisture from the air, making them ideal for critical applications like pharmaceuticals, electronics, and food processing. Advancements in desiccant technology have led to more efficient dryers with lower energy consumption and longer operational lifespans. Heatless desiccant dryers, which do not require additional energy for regeneration, are particularly popular in industries looking to reduce their energy consumption and operational costs.
- Emphasis on Predictive Maintenance
Predictive maintenance technologies are changing how compressed air systems are managed. By using real-time data and advanced analytics, businesses can monitor the performance of their air filters and dryers and predict when maintenance or replacement will be needed. This proactive approach minimizes downtime, reduces repair costs, and ensures that systems are always operating at peak efficiency.
Innovations Shaping the Industry
-
Integrated Filtration and Drying Systems
Some manufacturers are now offering integrated systems that combine both filtration and drying in one unit, optimizing space and simplifying maintenance. These all-in-one systems are particularly beneficial for industries with limited space or those looking to streamline their compressed air systems. -
Energy Recovery Systems
Energy recovery systems are being integrated into both air filters and dryers to reduce energy costs. These systems allow businesses to reclaim waste energy and reuse it, enhancing overall system efficiency and contributing to sustainability goals. -
Advanced Materials for Filters
Innovative filter materials, such as hydrophobic membranes and nano-fibers, are being developed to increase the efficiency of compressed air filters. These advanced materials provide better filtration with fewer energy requirements, improving the overall performance of compressed air systems.
The North American compressed air filter and dryer industry is evolving rapidly, driven by increasing demand for energy-efficient, high-performance solutions in a variety of sectors. With the expansion of manufacturing, industrial automation, and advancements in technology, the market for these essential components will continue to grow. From smart systems and predictive maintenance to energy-efficient technologies, innovations are shaping the future of the industry, ensuring that businesses can meet their operational needs while reducing costs and enhancing sustainability. As companies continue to focus on efficiency, compliance, and reliability, the compressed air filter and dryer market in North America will remain a vital part of industrial infrastructure in the years to come.
Frequently Asked Questions (FAQ) – North America Compressed Air Filter and Dryer Industry
1. What is a compressed air filter and dryer?
A compressed air filter removes contaminants such as dust, dirt, moisture, and oil from compressed air to ensure it remains clean and free of particles that could damage machinery or affect product quality. A compressed air dryer removes moisture from compressed air, preventing water build-up that could cause corrosion, freezing, or malfunction in equipment.
2. Why is a compressed air filter and dryer necessary?
Compressed air systems are used in numerous industries, and having clean, dry air is critical to maintaining equipment performance and product quality. Filters and dryers are vital to remove impurities and moisture, which could otherwise lead to equipment failure, contamination, or decreased system efficiency.
3. What industries use compressed air filters and dryers?
Compressed air filters and dryers are used across many industries, including:
- Manufacturing (automotive, electronics, machinery)
- Food and Beverage (to ensure product purity and safety)
- Pharmaceuticals (to comply with strict hygiene and contamination standards)
- Oil and Gas (to ensure machinery operates in optimal conditions)
- Automotive (to maintain pneumatic tools and equipment)
- Aerospace (to ensure precision in high-performance systems)
4. What are the main types of compressed air dryers?
There are several types of compressed air dryers, each suited for different applications:
- Refrigerated Air Dryers: Use a refrigeration cycle to cool compressed air, condensing moisture into water that can be drained away. Ideal for general industrial applications.
- Desiccant Dryers: Use materials like silica gel or activated alumina to absorb moisture from the air. Best for applications requiring extremely dry air.
- Membrane Dryers: Use a semi-permeable membrane to separate moisture from the air, suitable for low-flow applications.
5. How do compressed air filters and dryers improve energy efficiency?
Modern energy-efficient filters and dryers help minimize energy consumption by reducing air pressure loss, optimizing airflow, and decreasing the energy required to produce dry air. Features like heat recovery in air dryers and variable-speed drives in air compressors contribute to overall energy savings by capturing and reusing waste energy.