The US industrial agitator market is experiencing significant growth and transformation, fueled by continuous innovations and technological advancements. Industrial agitators, essential components in many manufacturing processes, are used to mix, blend, and transport materials across various industries, including chemicals, pharmaceuticals, food and beverage, and oil and gas. As the demand for more efficient, sustainable, and cost-effective solutions rises, the market for industrial agitators is evolving to meet the needs of modern industries.
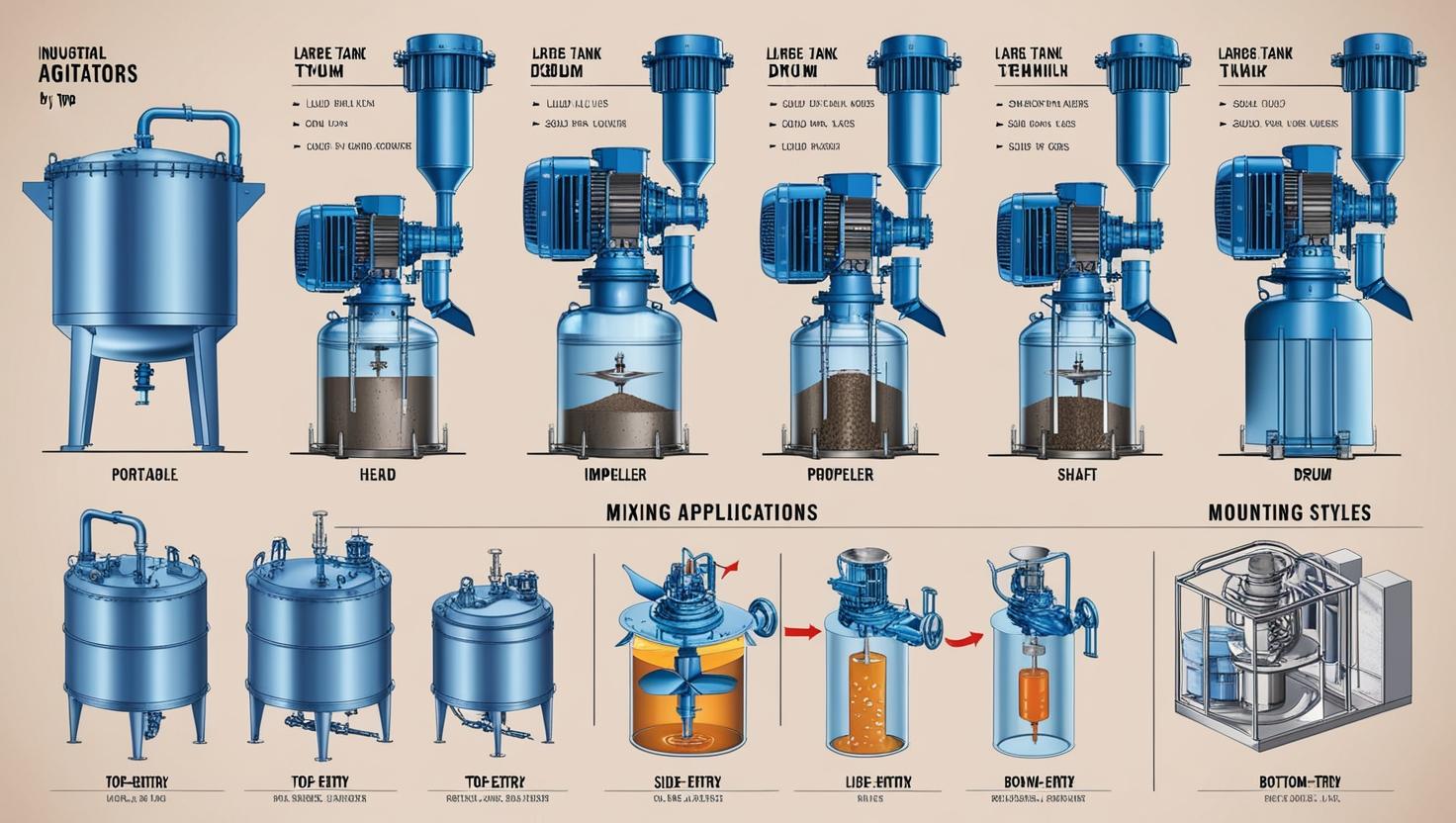
The global industrial agitators industry is expected to be valued at USD 3.10 billion in 2024 and is projected to reach USD 3.99 billion by 2029; it is expected to grow at a CAGR of 5.2 % from 2024 to 2029. Agitators are important in mixing, blending, and homogenizing ingredients during production processes. They also form an essential part in guaranteeing uniform distribution of active pharmaceutical ingredients (APIs), chemical processes, oil & gas, mining, etc. Rise in the demand for homogeneous mixing, increased need for energy efficient mixing equipment or industrial mixer in pharmaceutical, chemical, and food & beverage industries, and growing adoption of customized industrial agitators are some of the major factors driving the industrial agitators market growth globally.
This article explores the key innovations and technological advancements shaping the future of the US industrial agitator market.
1. Shift Towards Energy Efficiency and Sustainability
As industries are becoming more focused on sustainability and reducing their carbon footprints, energy efficiency is a primary concern in the industrial agitator market. Traditional agitators often consume a substantial amount of energy, and optimizing energy use has become a significant priority.
Advanced Motor Technologies: New motor technologies, such as permanent magnet motors and high-efficiency variable frequency drives (VFDs), are being integrated into agitators to enhance energy efficiency. These motors help reduce energy consumption by adjusting the speed and torque depending on the load, which optimizes power usage and reduces operational costs.
Improved Sealing and Bearings: Another innovation contributing to energy efficiency is the development of better sealing and bearing technologies. These components reduce friction, energy loss, and wear and tear on agitator systems, leading to longer operational lifespans and lower maintenance costs.
Sustainable Materials: Manufacturers are also focusing on the use of sustainable materials in agitator components. Innovations in corrosion-resistant coatings and environmentally friendly materials are not only helping reduce environmental impacts but also improving the durability and longevity of agitators.
2. Integration of Smart Technologies and Automation
The industrial agitator market is increasingly adopting smart technologies and automation, making systems more efficient and easier to control. The integration of automation, data analytics, and IoT (Internet of Things) is transforming traditional agitators into highly intelligent, self-regulating systems that provide enhanced performance, real-time monitoring, and predictive maintenance capabilities.
IoT Connectivity and Data Analytics: Industrial agitators are being equipped with IoT sensors that allow operators to collect real-time data on key parameters like speed, torque, temperature, and vibration. This data can be sent to a centralized system where it can be analyzed to optimize performance, identify potential issues, and improve overall system efficiency. By harnessing data analytics, manufacturers can make data-driven decisions that result in more precise and reliable mixing processes.
Predictive Maintenance: The integration of AI and machine learning algorithms is enabling predictive maintenance for industrial agitators. Sensors monitor the health of agitator components and provide alerts when wear or malfunction is detected, allowing for timely maintenance and preventing unplanned downtime. This predictive capability helps manufacturers reduce maintenance costs and improve operational reliability.
Remote Monitoring and Control: Remote monitoring and control systems are becoming increasingly popular in the US industrial agitator market. These systems allow operators to manage and adjust agitator performance from anywhere, ensuring that operations run smoothly even in remote or hazardous locations. This level of control increases operational flexibility and improves overall process efficiency.
Download PDF Brochure @
https://www.marketsandmarkets.com/pdfdownloadNew.asp?id=59649096
3. Customization and Flexible Designs
As industries continue to diversify their needs and processes, the demand for customized and flexible agitator designs is growing. In response to this demand, manufacturers are innovating to offer more versatile solutions that can be tailored to specific applications.
Modular Agitator Systems: Modular agitator designs, which allow for easy customization and reconfiguration, are gaining popularity. These systems offer increased flexibility, enabling manufacturers to quickly adapt to changing production requirements or switch between different mixing processes without significant downtime.
Improved Impeller Designs: The design and material of impellers, the key components responsible for mixing, are evolving to meet the growing demands for more efficient and effective mixing. Advanced impeller designs, such as high-shear and dual-stage impellers, are being developed to handle more complex applications and enhance performance in industries such as pharmaceuticals and food processing.
Flexible Materials for Aggressive Environments: For industries dealing with corrosive or abrasive materials, the use of high-performance alloys and coatings is becoming more prevalent. Agitators are being designed with specialized materials that can withstand harsh conditions, ensuring long-lasting performance and reducing the risk of failure in extreme environments.
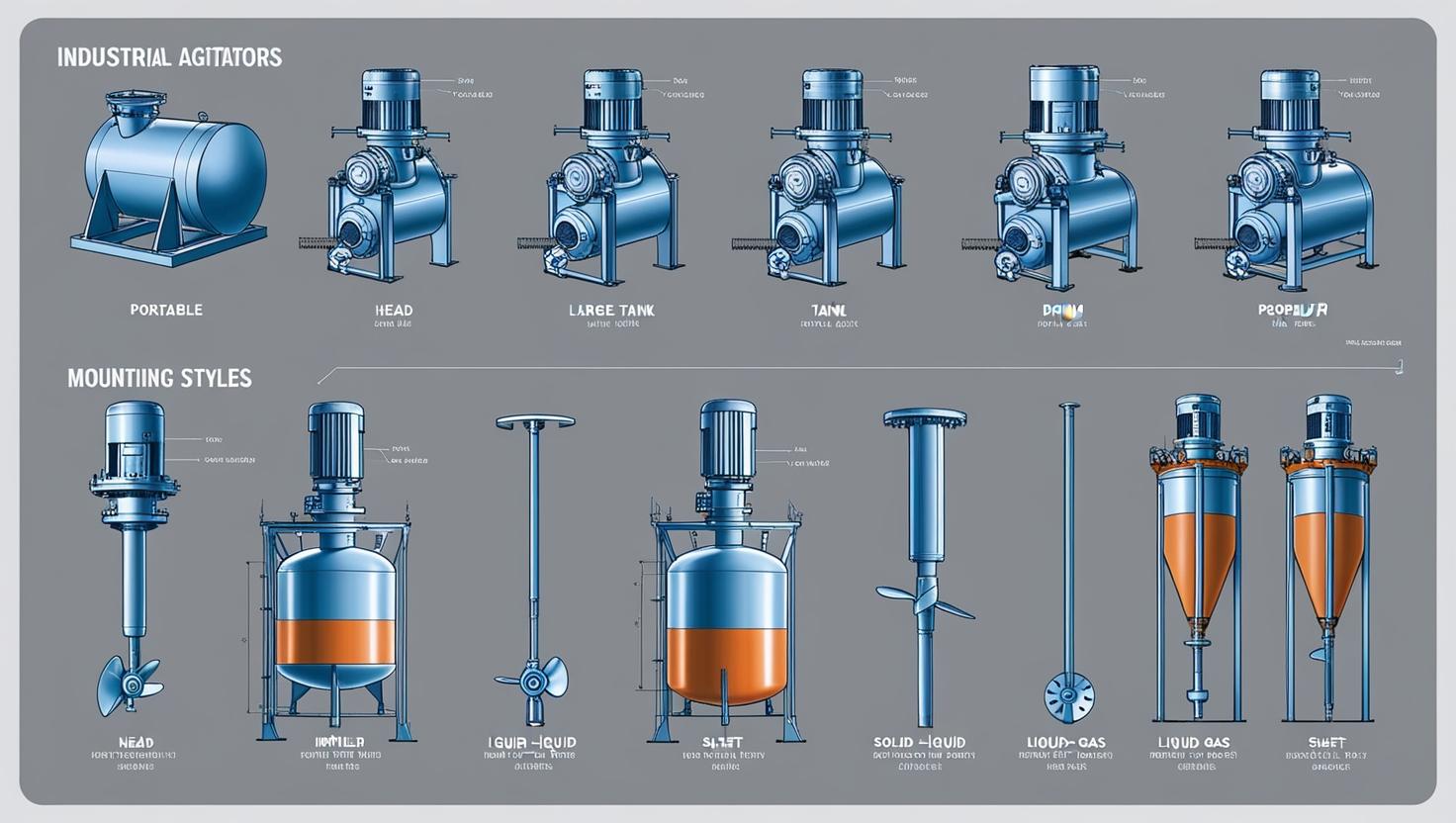
4. Enhanced Safety and Regulatory Compliance
Safety is always a top priority in industrial operations, especially when handling hazardous or volatile materials. The US industrial agitator market is increasingly focusing on innovations that improve safety and ensure compliance with strict regulations.
Explosion-Proof Agitators: Industries such as chemicals and oil and gas often work with highly flammable or explosive substances. Agitators designed for these environments are being engineered with explosion-proof features, including reinforced housings, anti-static components, and other safety mechanisms that prevent accidents and protect workers.
Sanitary and Hygienic Agitators: In industries like food and beverage and pharmaceuticals, where cleanliness and sanitation are critical, agitators are being designed to meet the highest hygiene standards. Sanitary agitators feature smooth surfaces, easy-to-clean designs, and hygienic materials that reduce the risk of contamination and ensure compliance with industry regulations.
Advanced Control Systems: To enhance safety, advanced control systems are being integrated into industrial agitators. These systems provide operators with better oversight of critical processes and include automated shutdown features in case of failure or dangerous conditions, helping minimize risks and ensure regulatory compliance.
5. Industry-Specific Innovations
The versatility of industrial agitators means that they are applied across many sectors, each with its own set of challenges and requirements. As a result, innovations are being tailored to meet the specific needs of different industries.
Chemical Industry Innovations: In the chemical industry, where precise mixing is required for complex formulations, high-shear agitators and specialized mixing technologies are being developed to ensure uniformity and quality. The use of advanced corrosion-resistant materials is also a key innovation, helping to extend the lifespan of agitators in harsh chemical environments.
Pharmaceutical Applications: Pharmaceutical manufacturers rely on agitators for mixing and blending sensitive ingredients. Innovations in this area include the development of agitators with ultra-smooth, non-reactive surfaces to prevent contamination and preserve the integrity of active ingredients. Additionally, innovations in automated control systems ensure the precise mixing of pharmaceutical formulations.
Food and Beverage Industry: In food and beverage manufacturing, agitators need to meet strict food safety standards while also being capable of handling a wide variety of products, from thick pastes to thin liquids. Innovations in hygienic designs, temperature control, and gentle mixing mechanisms are driving the development of agitators tailored for this industry.
Conclusion: A Promising Future for the US Industrial Agitator Market
The US industrial agitator market is evolving rapidly, driven by continuous technological advancements and innovations in energy efficiency, automation, customization, and safety. As industries become more data-driven, sustainable, and precise, the demand for advanced agitators that can meet these evolving needs will continue to rise. From the integration of IoT and predictive maintenance to the development of industry-specific solutions, the future of the industrial agitator market is poised for substantial growth and transformation. Manufacturers that embrace these innovations will be better positioned to improve operational efficiency, reduce costs, and stay ahead in an increasingly