The Asia-Pacific (APAC) region has long been a global hub for industrial growth, with booming manufacturing sectors in countries like China, India, Japan, and South Korea. As industries continue to expand, the demand for efficient and advanced equipment is surging, particularly in the realm of industrial agitators. Industrial agitators are vital components in processes such as mixing, blending, and homogenizing materials across various sectors, including chemicals, pharmaceuticals, food and beverage, and mining. With increasing pressures to enhance operational efficiency, minimize energy consumption, and improve production quality, the Asia-Pacific industrial agitator market is poised for transformative changes.
This article explores the key advancements in efficiency and automation that are shaping the future of the market.
1. Push Toward Energy Efficiency and Sustainable Solutions
As industries in the APAC region aim to become more sustainable, energy efficiency has become a primary focus in the development of industrial agitators. The region’s rapid industrialization has led to higher energy consumption, and governments are now imposing stricter regulations to limit carbon emissions and promote energy savings.
Energy-Efficient Motors: One of the most significant advancements in industrial agitators is the integration of energy-efficient motors. These motors consume less power, reducing overall energy costs for manufacturers. Variable frequency drives (VFDs) are also playing an essential role in this shift, allowing agitators to adjust their speed according to the load, optimizing energy consumption and enhancing the overall operational efficiency of the system.
Sustainable Materials: Manufacturers are also turning to sustainable and corrosion-resistant materials for agitator components. These materials not only help improve the longevity of the equipment but also reduce the environmental impact of manufacturing processes. For example, the use of high-grade stainless steel and advanced coatings helps improve durability while meeting industry demands for more environmentally responsible solutions.
Reducing Water and Waste Use: In industries like food and beverage processing, reducing water consumption and minimizing waste are major priorities. Innovations in agitator design, such as more efficient mixing mechanisms, enable manufacturers to reduce water and ingredient wastage while improving output, contributing to both cost savings and environmental sustainability.
2. Automation and Integration of Smart Technologies
Automation is the driving force behind much of the transformation in the industrial agitator market. As the APAC region continues to embrace Industry 4.0, the integration of smart technologies into manufacturing processes is essential for improving productivity and streamlining operations.
IoT and Real-Time Monitoring: The Internet of Things (IoT) is revolutionizing the way industrial agitators operate. By incorporating IoT sensors into agitators, manufacturers can gather real-time data on performance parameters such as speed, torque, vibration, temperature, and pressure. This data is sent to a central monitoring system, allowing operators to oversee and control agitator performance remotely. With IoT-enabled agitators, manufacturers can gain a comprehensive understanding of equipment status, making it easier to detect anomalies, monitor equipment health, and optimize performance.
Predictive Maintenance: Predictive maintenance is one of the most valuable applications of automation in the industrial agitator market. AI and machine learning algorithms, integrated with real-time data from sensors, help predict when agitator components are likely to fail or need maintenance. This enables manufacturers to perform maintenance proactively, reducing costly downtime and extending the lifespan of the equipment. Predictive maintenance also minimizes the need for routine maintenance, lowering operational costs and improving overall efficiency.
Remote Operation and Control: With the advent of remote operation systems, operators can control and adjust agitator parameters from a distance, reducing the need for manual intervention and enhancing operational flexibility. This is especially beneficial for large-scale operations with multiple production lines, where remote monitoring allows for quick adjustments without disrupting the entire system.
Download PDF Brochure @
https://www.marketsandmarkets.com/pdfdownloadNew.asp?id=59649096
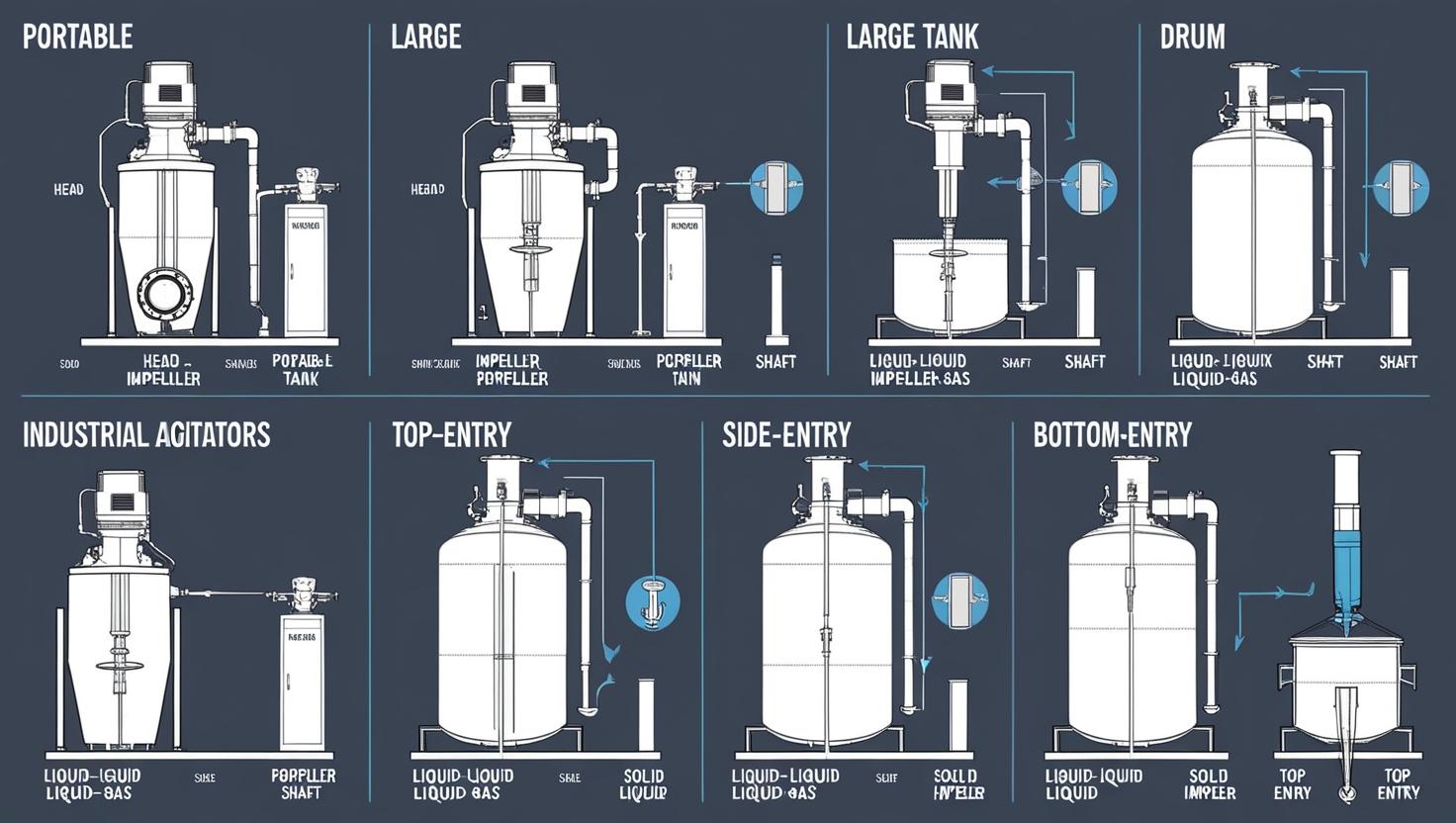
3. Customization and Flexibility in Agitator Design
As industries in the APAC region evolve and diversify, the demand for customized solutions to meet specific production requirements is on the rise. The industrial agitator market is increasingly moving toward more flexible and adaptable designs that can be tailored to the unique needs of various industries.
Modular Systems: Modular agitator systems are becoming increasingly popular because they allow for easy customization and scalability. These systems can be adjusted or reconfigured based on changing production needs, making them ideal for industries where product formulations or production methods frequently change. For example, modular agitators can be easily adapted to different container sizes or mixing requirements, providing greater operational flexibility.
Advanced Impeller Designs: Impellers are the heart of industrial agitators, and innovative impeller designs are improving mixing efficiency across various applications. High-shear impellers, for instance, are ideal for mixing viscous or dense fluids, while dual-stage impellers allow for the blending of materials with significantly different densities. These advanced impeller designs are tailored to meet the diverse needs of the chemical, pharmaceutical, and food industries in the APAC region.
Industry-Specific Customization: Different industries have specific challenges that demand specialized agitator designs. In the pharmaceutical and food industries, for instance, agitators must meet strict sanitary and hygiene standards. In such cases, designs that facilitate easy cleaning, such as those featuring smooth, crevice-free surfaces, are highly valued. In the chemical industry, agitators may need to be constructed with corrosion-resistant materials to handle aggressive chemicals or high temperatures.
4. Digitalization and Data-Driven Decisions
In the rapidly evolving industrial landscape of the APAC region, data-driven decision-making is becoming a cornerstone of business strategy. The industrial agitator market is embracing digital technologies that allow manufacturers to optimize processes based on data analytics and predictive modeling.
Digital Twins and Simulation Technology: One of the most promising innovations is the use of digital twins – virtual replicas of physical agitators. These digital twins allow manufacturers to simulate real-world conditions and monitor agitator performance in real time. By simulating various scenarios, manufacturers can predict how changes in agitator design or operating conditions will affect performance, providing a powerful tool for process optimization.
Big Data Analytics: The massive amounts of data generated by IoT-enabled agitators are invaluable for improving operational efficiency. By analyzing this data, manufacturers can identify trends, forecast production outcomes, and optimize agitator settings for different types of materials or conditions. Data analytics help ensure that the mixing process is as efficient as possible, contributing to better product quality, consistency, and reduced waste.
Cloud Integration: Cloud-based platforms are enabling manufacturers in the APAC region to access and share data more easily across different locations. This integration ensures that data is stored securely, and operators can access real-time information regardless of their physical location. The cloud also enables remote troubleshooting, support, and collaboration among teams in different geographic regions, streamlining operations and improving overall efficiency.
5. Competitive Landscape and Key Players
The industrial agitator industry in Asia-Pacific is highly competitive, with both global and regional players offering a wide range of solutions. Key manufacturers, such as SPX FLOW, Alfa Laval, and Xylem, are investing heavily in R&D to drive innovation and meet the increasing demand for more efficient, automated, and sustainable solutions. Local companies are also innovating by developing cost-effective solutions suited to regional needs and regulations.
Conclusion: A Bright Future for the Asia-Pacific Industrial Agitator Market
The future of the Asia-Pacific industrial agitator market is bright, driven by advancements in efficiency, automation, and digital technologies. As industries across the region demand smarter, more sustainable, and customizable solutions, the market for industrial agitators will continue to evolve to meet these needs. With the integration of IoT, AI, and advanced materials, the Asia-Pacific region is set to lead the way in innovative industrial mixing solutions, providing businesses with the tools they need to optimize performance, reduce costs, and stay competitive in a rapidly changing marketplace.