The US industrial software industry is at the forefront of a profound transformation in the manufacturing sector. As industries continue to adopt more digital and automated processes, industrial software solutions are playing an essential role in driving innovation, improving operational efficiency, and enhancing productivity. With advancements in technologies such as Artificial Intelligence (AI), Internet of Things (IoT), Big Data, and cloud computing, the scope and application of industrial software have expanded exponentially.
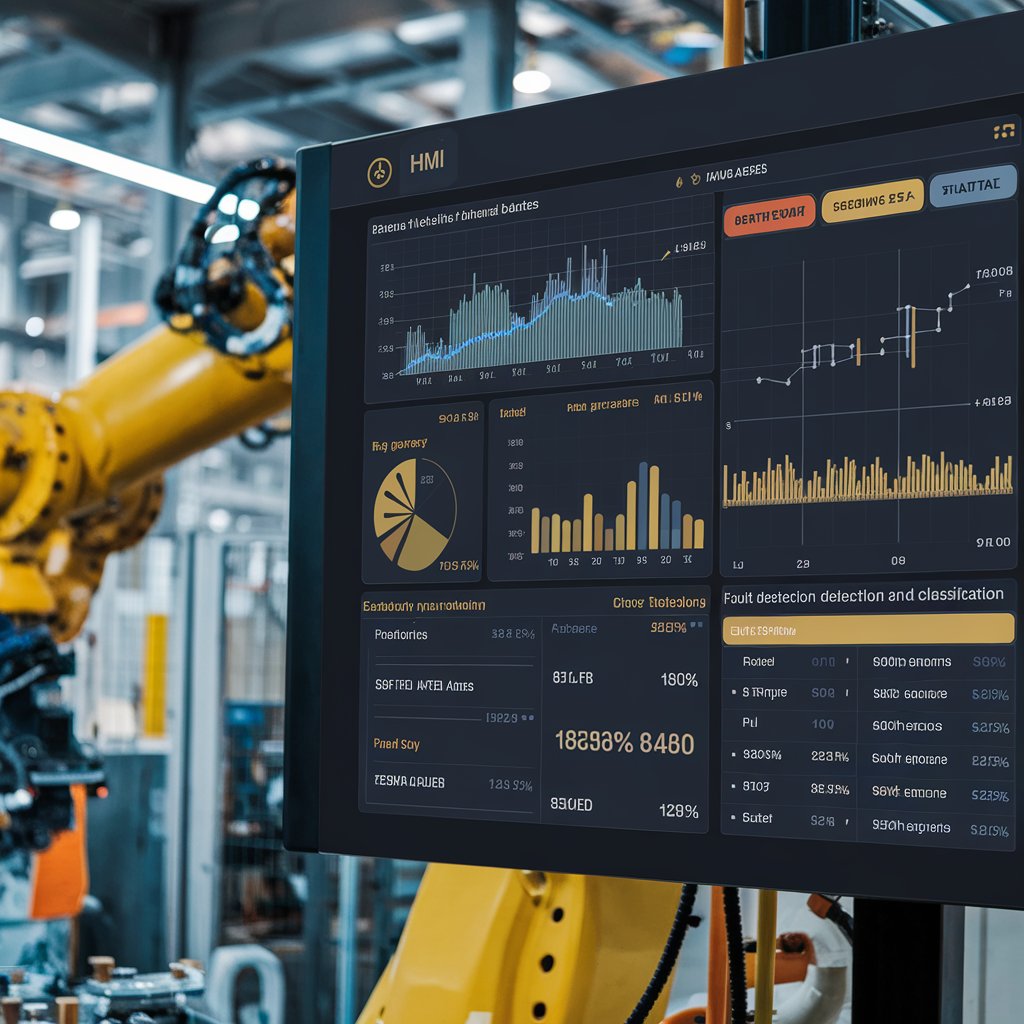
The demand for industrial software has skyrocketed, with businesses increasingly relying on software solutions to optimize production lines, manage assets, predict maintenance, and ensure the smooth operation of their plants and factories. This article explores the key trends, innovations, and the growth of the industrial software industry in the United States and how these cutting-edge solutions are revolutionizing manufacturing.
1. The Role of Industrial Software in the Age of Industry 4.0
Industry 4.0, often referred to as the fourth industrial revolution, is characterized by the integration of smart technologies into manufacturing processes. These include automation, AI, robotics, and cyber-physical systems that interact with each other in real time, enabling unprecedented levels of efficiency and productivity.
Industrial software is the backbone of Industry 4.0, helping manufacturers digitize their operations, improve real-time decision-making, and move towards smart factories. Solutions such as Manufacturing Execution Systems (MES), Enterprise Resource Planning (ERP), Computer-Aided Design (CAD), and Product Lifecycle Management (PLM) allow for integrated control and optimization across all stages of the production process.
-
Manufacturing Execution Systems (MES) help manage and monitor production on the shop floor, improving transparency, traceability, and control.
-
Enterprise Resource Planning (ERP) systems integrate various business functions, such as finance, inventory, human resources, and procurement, providing a holistic view of the operations.
-
Product Lifecycle Management (PLM) systems support the entire lifecycle of a product from conception to design, manufacturing, and after-sales service, allowing businesses to innovate and streamline product development.
The ability of industrial software to collect, process, and analyze vast amounts of data is a game-changer. By using data-driven insights, manufacturers can make faster, more informed decisions that enhance efficiency and reduce costs.
2. Leveraging AI and IoT for Smarter Manufacturing
One of the most transformative aspects of industrial software in recent years is the integration of AI and IoT technologies. These technologies provide a level of connectivity and intelligence that was previously unimaginable in the manufacturing world.
-
IoT enables the connection of machines, sensors, and devices on the shop floor, allowing manufacturers to gather real-time data on production processes, machine health, and environmental conditions. This data can be used to monitor performance, track inventory, and detect potential issues before they lead to costly breakdowns or downtime.
-
AI and Machine Learning (ML) play a crucial role in analyzing the vast amounts of data collected through IoT sensors. AI algorithms can detect patterns, predict maintenance needs, optimize supply chains, and even drive autonomous decision-making in real-time.
The combination of AI and IoT allows manufacturers to implement predictive maintenance, a game-changing capability that minimizes unplanned downtime. By predicting when a machine will fail before it actually does, manufacturers can schedule maintenance during non-peak hours and avoid costly disruptions in production.
Additionally, AI-powered optimization tools can help manufacturers improve production efficiency by fine-tuning operations, reducing waste, and maximizing throughput. The ability to leverage AI to continuously improve processes is a key driver in the adoption of industrial software solutions in the US.
Download PDF Brochure @
https://www.marketsandmarkets.com/pdfdownloadNew.asp?id=27555137
3. Cloud-Based Industrial Software: Scaling Operations with Flexibility
The rise of cloud computing has had a profound impact on industrial software adoption. Cloud-based solutions enable manufacturers to scale their operations without the need for significant upfront capital investment in IT infrastructure. They also provide the flexibility to manage operations remotely, which is increasingly important in today’s interconnected and distributed world.
-
Cloud-based MES, ERP, and PLM systems allow manufacturers to access real-time data, track production processes, and manage inventory from anywhere. This level of flexibility is essential for manufacturers looking to expand operations, streamline their supply chains, or integrate with other business units across various geographies.
-
Cloud computing also enables the development of Software-as-a-Service (SaaS) platforms, which offer subscription-based access to industrial software tools. This model is cost-effective and scalable, making it easier for businesses of all sizes to adopt advanced software solutions.
Cloud-based solutions also facilitate collaboration across teams and departments, enabling seamless data sharing, improved communication, and better coordination. As industrial operations become more complex, the ability to collaborate in real time and manage resources more effectively is becoming increasingly valuable.
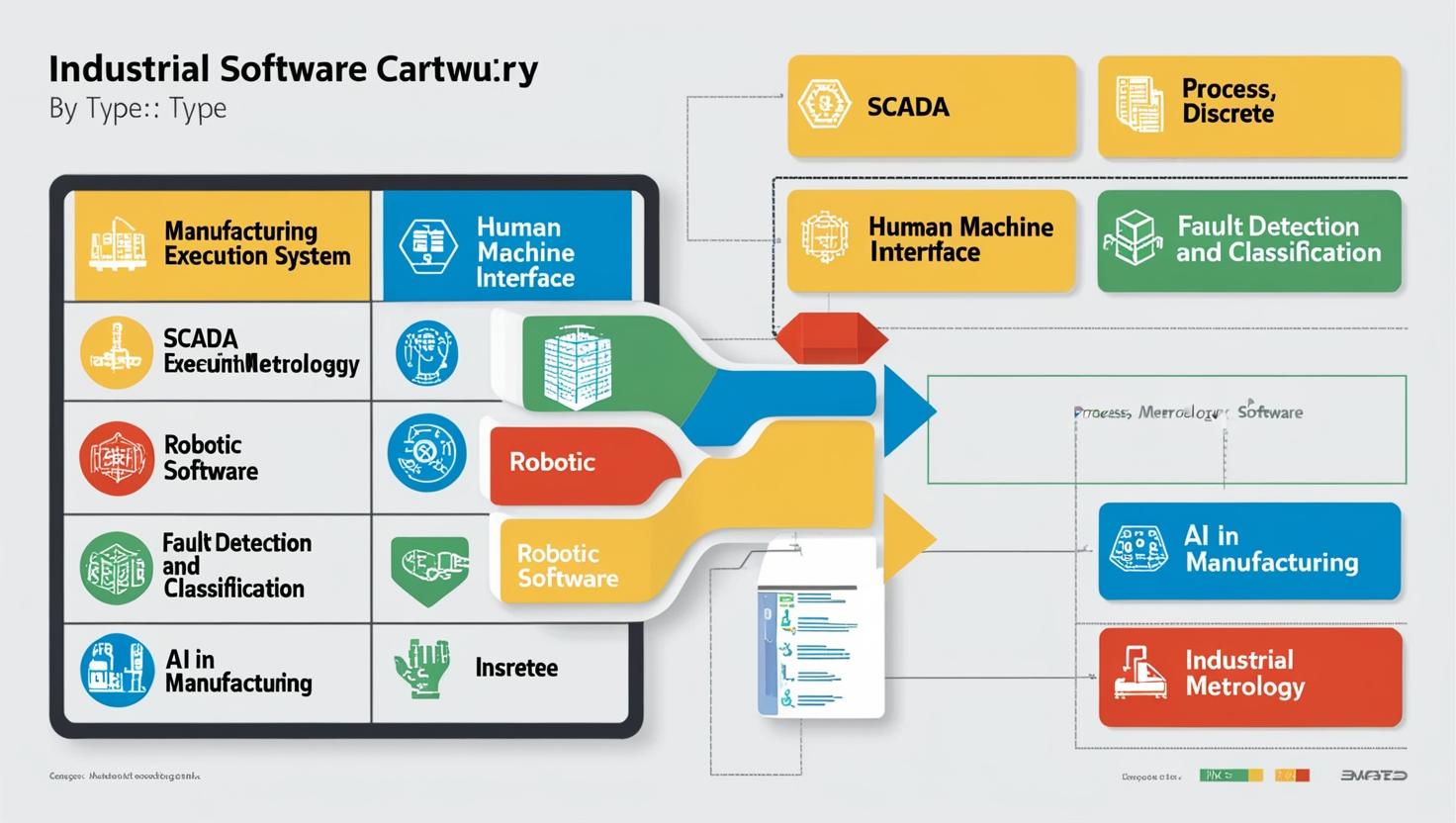
4. The Importance of Cybersecurity in Industrial Software
As manufacturing systems become more digitized and interconnected, cybersecurity has become a critical concern. Industrial software systems are now the prime targets of cyberattacks, with the potential for disruptions to production, data theft, and sabotage. Therefore, manufacturers must invest in robust cybersecurity measures to safeguard their operations.
Modern industrial software platforms are incorporating advanced security protocols, such as encryption, multi-factor authentication, and network segmentation, to protect sensitive data and systems. Regular cybersecurity audits and the use of AI-based threat detection systems help proactively identify vulnerabilities and mitigate risks.
The ability to secure data and manufacturing systems is essential for building trust with customers and stakeholders, as well as complying with industry regulations such as ISO 27001, NIST, and GDPR.
5. Future Trends in the US Industrial Software Industry
The future of industrial software in the US looks promising, with several key trends poised to drive growth:
-
Edge Computing: As more devices become interconnected, edge computing will enable data processing closer to the source, reducing latency and bandwidth requirements. This will enable even faster decision-making and real-time processing at the factory floor level.
-
Digital Twins: The concept of creating a digital replica of physical assets and processes through industrial software will allow manufacturers to simulate, monitor, and optimize operations virtually. Digital twins will play a crucial role in predictive maintenance, quality control, and process optimization.
-
5G Connectivity: The rollout of 5G networks will enable faster data transfer, more reliable communication, and lower latency, making it easier for industrial software to support real-time data analysis and automation on a large scale.
-
Robotics and Automation: With the integration of robotics and automation in industrial operations, software will play a pivotal role in orchestrating robotic systems, ensuring seamless collaboration between machines and humans on the shop floor.
The US industrial software industry is evolving rapidly, driven by technological advancements that are reshaping manufacturing processes across the country. With the growing adoption of AI, IoT, cloud-based solutions, and other cutting-edge technologies, industrial software is enabling manufacturers to operate more efficiently, reduce costs, and improve quality control. As the industry embraces Industry 4.0, software solutions will continue to serve as the backbone of the digital transformation, providing manufacturers with the tools needed to stay competitive in a rapidly changing market.
As we look to the future, the US industrial software market is set for continued growth, driven by innovation, automation, and digitalization. For manufacturers looking to stay ahead of the curve, investing in the latest software technologies will be essential for achieving operational excellence and unlocking new levels of productivity.