The U.S. Industrial Control and Factory Automation market is experiencing a significant transformation, driven by advancements in smart technologies such as Artificial Intelligence (AI), the Internet of Things (IoT), robotics, and advanced sensors. As industries continue to evolve, the demand for smarter, more efficient, and more reliable manufacturing solutions has never been greater. The infusion of digital technologies into manufacturing processes is not only enhancing productivity but is also enabling the U.S. to maintain its competitive edge in the global market. From the rise of smart factories to the integration of machine learning in production lines, the U.S. industrial control and automation market is poised for robust growth.
The Rise of Smart Factories and Industry 4.0
One of the most significant trends in the U.S. industrial control and factory automation market is the widespread adoption of Industry 4.0, a term that describes the next phase of the industrial revolution. Industry 4.0 leverages interconnected smart devices, advanced data analytics, machine learning, and AI to create “smart factories” where machines can communicate with each other, self-optimize, and make decisions based on real-time data.
Smart factories are changing the way products are designed, produced, and maintained. With the help of sensors and IoT devices, manufacturers can monitor every aspect of their operations—from inventory levels to machine health and supply chain status. This real-time data allows for predictive maintenance, reducing downtime and minimizing the cost of repairs. Additionally, the increased automation and connected devices streamline production lines, enhancing efficiency and reducing human error.
Robotics and AI Integration
Robotics and AI play a central role in the transformation of industrial control and factory automation. Robots are no longer confined to simple tasks; they are becoming highly versatile, capable of handling complex assembly operations, product testing, and quality control. AI algorithms allow robots to learn from their environment and adapt to changes in the production process.
For instance, in the automotive industry, robots equipped with AI and machine vision systems can perform intricate tasks such as painting, welding, and inspection with precision and speed that far surpasses human capabilities. This automation not only increases production efficiency but also enhances product quality, reducing defects and waste.
AI-powered systems also enable predictive analytics, allowing manufacturers to forecast production demands, optimize supply chains, and improve decision-making. By analyzing vast amounts of data from multiple sources, AI can detect inefficiencies or potential issues before they become problems, further boosting productivity and operational efficiency.
Download PDF Brochure @ https://www.marketsandmarkets.com/pdfdownloadNew.asp?id=541
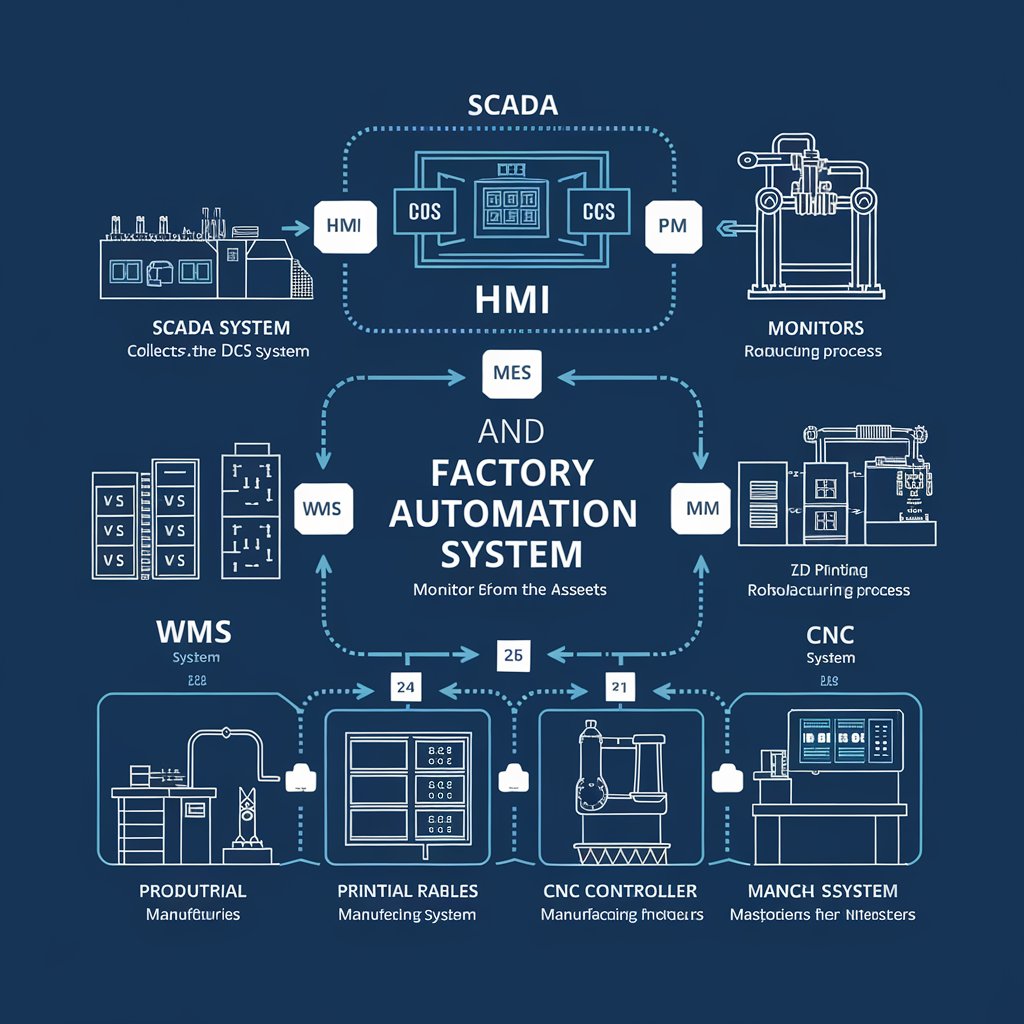
IoT and Real-Time Monitoring
The integration of IoT devices in industrial control systems has opened up new possibilities for real-time monitoring and remote management. IoT sensors are embedded in machines and equipment, allowing operators to monitor their status, performance, and environmental conditions remotely. These sensors can detect vibrations, temperature fluctuations, pressure levels, and more, alerting operators to potential problems before they lead to costly downtime.
Real-time monitoring powered by IoT enables manufacturers to identify inefficiencies in the production process and make data-driven decisions to optimize workflows. For example, IoT-enabled equipment can provide immediate feedback on the performance of machines, enabling quick adjustments to improve output and reduce waste. This constant flow of information enhances both operational visibility and control, making it easier to manage production schedules, inventory, and maintenance activities.
The Role of Advanced Sensors
Advanced sensors are at the heart of many industrial control and factory automation systems. These sensors are crucial for measuring physical parameters such as temperature, pressure, speed, and flow, which are essential for maintaining high-quality standards in manufacturing. The development of more sophisticated and sensitive sensors has greatly improved the accuracy and efficiency of industrial systems.
For example, in the food and beverage industry, sensors are used to monitor the temperature and humidity of storage areas to ensure product quality and safety. Similarly, in the pharmaceutical industry, sensors are essential for maintaining strict environmental conditions during the production and storage of drugs. These sensors enable real-time quality assurance and compliance with regulatory standards, further optimizing production and ensuring consistency in products.
Cloud Computing and Data Analytics
As manufacturing processes become increasingly connected, the amount of data generated is expanding exponentially. Cloud computing has become a vital tool in the management and analysis of this data. By moving data storage and analysis to the cloud, manufacturers can access vast amounts of real-time information from anywhere, enabling more effective decision-making and collaboration across teams.
Cloud-based platforms also enable centralized control of manufacturing operations, allowing operators to monitor multiple production lines from a single dashboard. This integration of data from various sources creates a comprehensive view of the entire manufacturing ecosystem, providing valuable insights into operational performance and helping identify areas for improvement.
Moreover, cloud-based data analytics platforms help manufacturers optimize processes such as supply chain management, inventory control, and resource allocation. By using advanced algorithms and predictive analytics, manufacturers can forecast demand, reduce stockouts, and lower inventory costs while ensuring that production meets customer expectations.
Benefits of Industrial Control and Factory Automation
The adoption of industrial control and factory automation technologies is bringing several key benefits to U.S. manufacturers:
-
Increased Efficiency: Automation and real-time monitoring reduce production downtime, optimize workflows, and streamline operations, resulting in faster turnaround times and higher throughput.
-
Improved Quality and Precision: Robotics, AI, and advanced sensors ensure that products meet the highest standards of quality, with fewer defects and less variation.
-
Cost Savings: Automation and predictive maintenance reduce the need for human labor and prevent costly machine breakdowns, ultimately lowering operational costs.
-
Enhanced Flexibility and Scalability: Automated systems can quickly adapt to changes in demand or production schedules, allowing manufacturers to scale operations efficiently without significant capital investment.
-
Better Data-Driven Decision-Making: The integration of IoT, AI, and cloud computing enables manufacturers to make informed decisions based on real-time data, improving both short-term and long-term strategies.
The U.S. industrial control and factory automation market is undergoing a revolution, fueled by the integration of smart technologies such as AI, IoT, robotics, and advanced sensors. As manufacturers embrace these technologies, they are not only improving productivity and operational efficiency but also gaining a competitive edge in the global marketplace. The future of U.S. manufacturing is closely linked to the continued growth of industrial control and automation systems, and industries that invest in these technologies will be well-positioned to thrive in the digital age. As the market continues to evolve, the potential for even greater innovation and optimization in manufacturing processes is boundless.