The U.S. tariffs imposed during the Trump administration created significant disruptions across various industries, including industrial control and factory automation. These tariffs, particularly those targeting Chinese goods, affected supply chains, increased component costs, and forced manufacturers to rethink their global operations. However, every disruption presents an opportunity, and the industrial automation sector is no exception. As the market adapts to the post-tariff world, companies in this space can harness innovation, strategic shifts, and emerging technologies to not only recover but thrive.
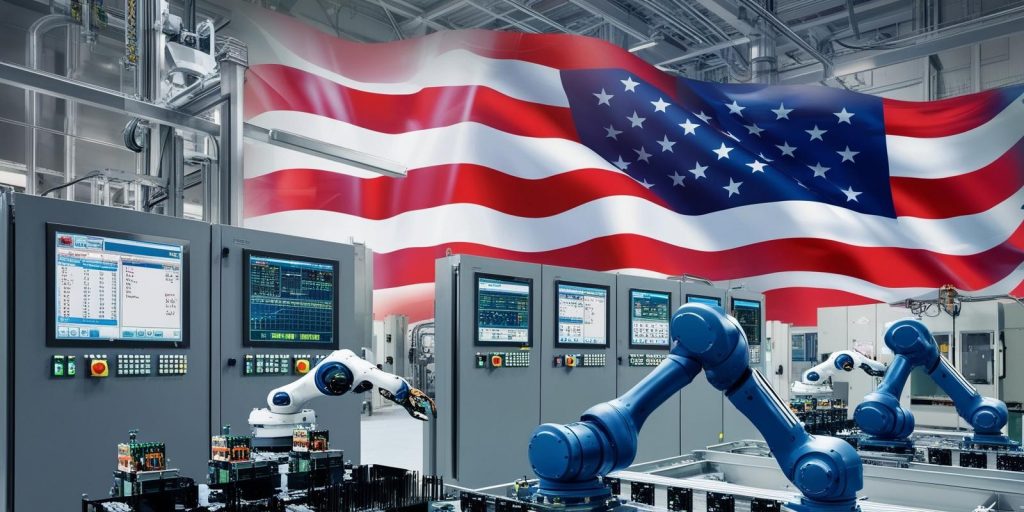
The Impact of Trump Tariffs on Industrial Control and Factory Automation
Impact of Trump Tariffs on Industrial Control and Factory Automation, The tariffs, which imposed taxes on a range of electronic components, parts, and systems from China, caused immediate and long-term effects on the industrial automation sector. Some of the most notable impacts included:
-
Increased Costs of Components: Many essential components for industrial control systems, such as microchips, sensors, and programmable logic controllers (PLCs), were subject to higher tariffs. This led to rising costs for manufacturers of factory automation systems.
-
Supply Chain Disruptions: Manufacturers who relied heavily on China for sourcing components or finished products faced delays, shortages, and increased lead times. This disrupted production schedules and heightened risks in global supply chains.
-
Shifts in Global Sourcing: In response to tariffs, companies started reevaluating their supply chains, with many moving operations to other regions such as Southeast Asia, Mexico, and Eastern Europe to mitigate tariff exposure.
While these challenges were significant, they also prompted necessary adjustments and created opportunities for companies to innovate, adapt, and find new ways of operating.
Request U.S. tariffs impact analysis now @ https://www.marketsandmarkets.com/pdfdownloadNew.asp?id=541
The Path Forward: Strategic Moves for Industrial Control & Factory Automation Players
In the wake of the tariff disruptions, companies in the industrial control and factory automation market can take proactive steps to reposition themselves for success. The following strategic recommendations offer a clear path forward:
1. Reshoring and Nearshoring to Strengthen Supply Chains
The tariffs highlighted the vulnerability of long, complex supply chains, particularly those reliant on a single source like China. In response, many companies are reshoring or nearshoring their manufacturing operations closer to home. This shift can mitigate the risk of future tariffs and trade disruptions.
Action: Invest in local manufacturing capabilities or move production to nearby countries with lower tariff rates and stable trade relations, such as Mexico or Canada. This reduces exposure to unpredictable global trade tensions and strengthens control over production and supply timelines.
Benefit: Shorter supply chains reduce lead times, lower transportation costs, and improve supply chain resilience. Additionally, reshoring can support job creation in local economies, improving a company’s brand image.
2. Diversification of Supply Chains
Tariffs underscored the importance of supply chain diversification. Relying heavily on one region or supplier for key components increases risk. The key to resilience in an unpredictable global market is a diversified supply chain that spans multiple regions.
Action: Look beyond China and explore sourcing from other regions such as Southeast Asia, India, Eastern Europe, or Latin America. This can help mitigate tariff impacts and reduce dependence on a single region.
Benefit: Diversifying suppliers allows for greater flexibility and reduces the risk of disruptions. It enables companies to navigate fluctuations in tariffs or supply shortages more effectively.
3. Embrace Automation and Digital Transformation
The rise in costs due to tariffs is pushing companies to seek ways to improve efficiency. This is where automation and digital transformation technologies come into play. Industry 4.0 technologies such as AI, IoT, and robotics are becoming increasingly important in streamlining manufacturing processes.
Action: Invest in automation systems and digital technologies that enhance operational efficiency, reduce costs, and drive productivity. Incorporating AI, predictive maintenance, and real-time monitoring into factory automation systems can improve reliability while minimizing downtime.
Benefit: Automation solutions help companies counterbalance higher component costs by improving productivity, reducing labor costs, and enhancing quality control. Moreover, they make businesses more competitive in a cost-sensitive environment.
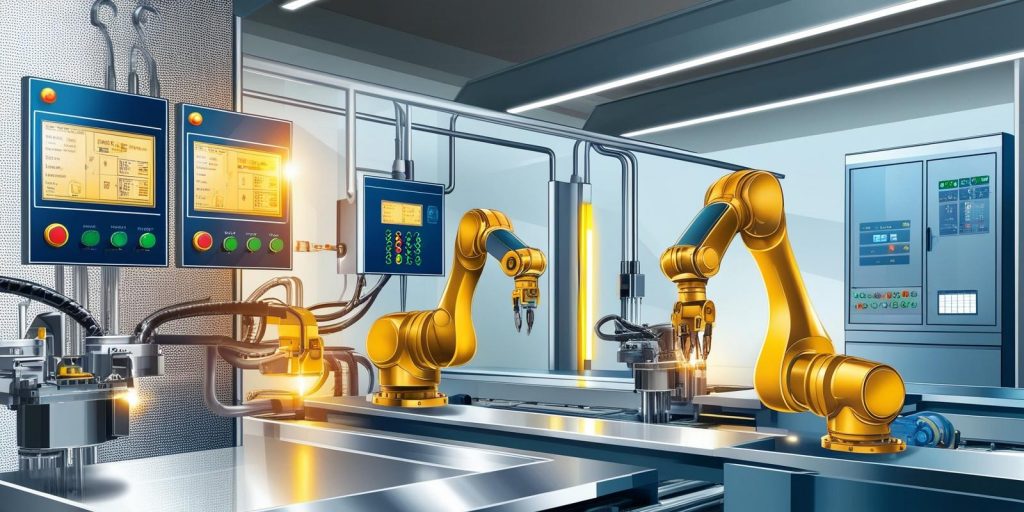
4. Innovation in Product and Process Design
As tariffs raise component costs, innovation becomes crucial. Companies in the industrial control and factory automation market need to focus on developing cost-effective, energy-efficient systems that require fewer expensive parts. By designing modular systems that use interchangeable components, businesses can avoid cost increases tied to specific materials.
Action: Invest in R&D to develop next-generation automation products that are both cost-effective and energy-efficient. Consider modular and integrated designs that reduce reliance on costly components and improve system adaptability.
Benefit: Innovative products that optimize resource usage and integrate more sustainable technologies will meet market demand for affordability and sustainability. This can create a competitive advantage in a rapidly evolving market.
5. Explore Emerging Markets
While the U.S. industrial automation market faces challenges from tariffs, many emerging markets are experiencing rapid growth in demand for automation technologies. Countries in Asia, Latin America, and Africa are undergoing industrialization and digital transformation, creating new opportunities for automation solutions.
Action: Target emerging markets where automation adoption is growing rapidly. Focus on countries with strong economic growth, rising manufacturing sectors, and a need for productivity improvements.
Benefit: Expanding into emerging markets offers new revenue streams and opportunities for growth. As these regions embrace industrial automation, they represent a burgeoning customer base for advanced control systems and robots.
6. Strategic Alliances and Partnerships
Tariffs and global trade uncertainties have led many companies to form strategic alliances to share risks and resources. Collaboration with other automation providers, suppliers, or technology companies can help mitigate some of the costs and complexities associated with tariffs.
Action: Forge partnerships with local manufacturers, technology providers, or other players in the supply chain. Collaborate on joint ventures, co-development of new solutions, or sharing of best practices to tackle supply chain issues and reduce costs.
Benefit: Partnerships enhance market access, reduce research and development costs, and provide shared resources to address the challenges created by tariffs. This can strengthen competitive positioning in both domestic and international markets.
Key Takeaways:
-
Reshoring and Nearshoring: Companies are increasingly relocating manufacturing closer to home or to nearby countries to reduce dependency on regions affected by tariffs and enhance supply chain resilience.
-
Diversification of Supply Chains: Reducing reliance on a single supplier or region, especially China, helps mitigate tariff risks and improves operational flexibility.
-
Digital Transformation: Embracing AI, IoT, and automation technologies boosts efficiency, reduces costs, and enhances competitiveness in the face of higher component prices.
-
Product and Process Innovation: Developing cost-effective, modular, and energy-efficient automation systems is key to maintaining profitability despite rising costs from tariffs.
-
Expansion into Emerging Markets: Targeting regions like Asia, Latin America, and Africa, where demand for automation technologies is increasing, provides new growth opportunities.
-
Strategic Partnerships: Forming alliances with local manufacturers, technology providers, and other stakeholders helps mitigate risks, share resources, and reduce costs.
Conclusion: Turning Disruption into Opportunity
While the Trump-era tariffs brought significant challenges to the industrial control and factory automation sectors, they also opened the door to innovation, strategic shifts, and new market opportunities. Companies that adapt to the new realities of a post-tariff world—through reshoring, diversification, digital transformation, and market expansion—can thrive in this changing landscape.
In the face of disruption, the industrial automation sector has an unprecedented opportunity to evolve, drive efficiencies, and explore new revenue streams. By embracing flexibility, innovation, and strategic foresight, companies can not only recover from the effects of tariffs but emerge stronger and more competitive than ever.