In a groundbreaking advancement for industrial operations, the integration of Automated Material Handling Equipment (AMHE) with Internet of Things (IoT) devices is transforming the landscape of manufacturing, warehousing, and logistics. This technological synergy is providing companies with unprecedented capabilities to monitor the performance, status, and condition of their equipment in real-time.
The fusion of automated Material Handling Equipment with IoT devices marks a significant leap forward for industries reliant on material handling. By offering real-time monitoring, predictive maintenance, and enhanced operational efficiency, this integration not only drives productivity but also ensures safer and more reliable operations. As companies continue to adopt and refine these technologies, the future of material handling looks increasingly automated, intelligent, and efficient.
The integration process involves embedding IoT devices such as sensors and actuators within AMHE systems. These devices collect a continuous stream of data, offering insights into various operational metrics. Sensors track parameters such as temperature, vibration, and load, while actuators enable automated adjustments to optimize performance and mitigate potential issues before they escalate.
Download PDF Brochure @
https://www.marketsandmarkets.com/pdfdownloadNew.asp?id=92483121
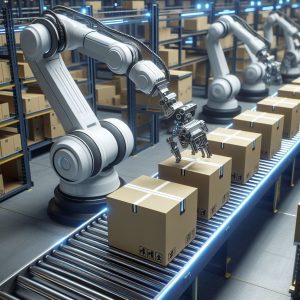
Real-Time Monitoring and Predictive Maintenance
One of the most significant benefits of this integration is the ability to perform real-time monitoring and predictive maintenance. By analyzing the data collected by IoT sensors, companies can anticipate equipment failures and schedule maintenance proactively, thus minimizing downtime and extending the lifespan of the machinery. This predictive approach not only enhances operational efficiency but also significantly reduces maintenance costs.
Enhanced Operational Efficiency
Real-time data collection and analysis allow companies to fine-tune their operations dynamically. For instance, if a conveyor system shows signs of overheating, the system can automatically adjust its speed or shut down parts of the operation to prevent damage. This immediate response capability ensures that equipment operates within optimal parameters, maintaining a steady flow of materials and reducing the risk of bottlenecks.
Improved Safety and Compliance
Safety is another critical area where IoT-integrated AMHE makes a substantial impact. Sensors can detect hazardous conditions such as excessive temperatures or unusual vibrations that might indicate a potential failure. The system can then alert operators or automatically shut down equipment to prevent accidents. Additionally, this constant monitoring helps companies stay compliant with safety regulations by providing detailed records of equipment performance and maintenance activities.
Data-Driven Decision Making
The vast amounts of data generated by IoT-enabled AMHE systems empower companies to make informed, data-driven decisions. Advanced analytics can uncover patterns and trends that were previously invisible, enabling managers to optimize workflows, allocate resources more efficiently, and enhance overall productivity.
Future Prospects
As the technology evolves, the integration of AMHE with IoT is expected to become even more sophisticated. Innovations such as machine learning and artificial intelligence will further enhance the predictive capabilities of these systems, leading to smarter, more autonomous operations.
Automated Material Handling Market Ecosystem
Daifuku Co, Ltd. (Japan), KION GROUP AG (Germany), SSI SCHAEFER (Germany), TOYOTA INDUSTRIES CORPORATION (Japan) and HONEYWELL INTERNATIONAL INC. (US) are the key players in the Automated