The Non-Destructive Testing (NDT) and inspection industry plays a crucial role in ensuring the safety, reliability, and performance of a wide range of assets and structures, from industrial machinery and infrastructure to aerospace components. As industries strive for higher efficiency, accuracy, and cost-effectiveness, the integration of emerging technologies like Artificial Intelligence (AI) and the Internet of Things (IoT) is transforming the way NDT and inspection processes are carried out. These advancements are not only enhancing traditional methods but also driving innovation, offering new opportunities for growth and improved outcomes.
The Role of AI in NDT and Inspection
Artificial Intelligence (AI) has begun revolutionizing the NDT and inspection sector by improving the analysis and interpretation of data collected during inspections. Traditionally, NDT methods such as ultrasonic testing, radiographic testing, and visual inspection relied heavily on human expertise to analyze the results, which often led to challenges such as errors in judgment, slow processing times, and high labor costs.
AI-powered tools, however, have made significant strides in automating the analysis of NDT data. Machine learning (ML) algorithms can now rapidly process large volumes of inspection data, learning to identify patterns, anomalies, and potential defects more accurately than human inspectors. AI systems can also learn from previous inspections, continually improving their diagnostic capabilities over time. For example, AI algorithms can identify and classify materials, detect corrosion, cracks, and other structural issues with greater precision, reducing the risk of human error.
Moreover, AI in conjunction with image recognition technologies is improving visual inspections, enabling systems to automatically detect defects in images from cameras or other sensors. This leads to faster inspection cycles, less downtime, and more accurate results, ultimately contributing to better asset management and maintenance planning.
NDT and inspection industry overview
The NDT and inspection industry is expected to reach USD 18.4 billion by 2029 from 11.6 billion in 2024, at a CAGR of 9.6% during the 2024-2029 period. Various companies are investing in NDT and Inspection which gives an opportunity for growth in the NDT and Inspection industry .
Download PDF Brochure @ https://www.marketsandmarkets.com/pdfdownloadNew.asp?id=882
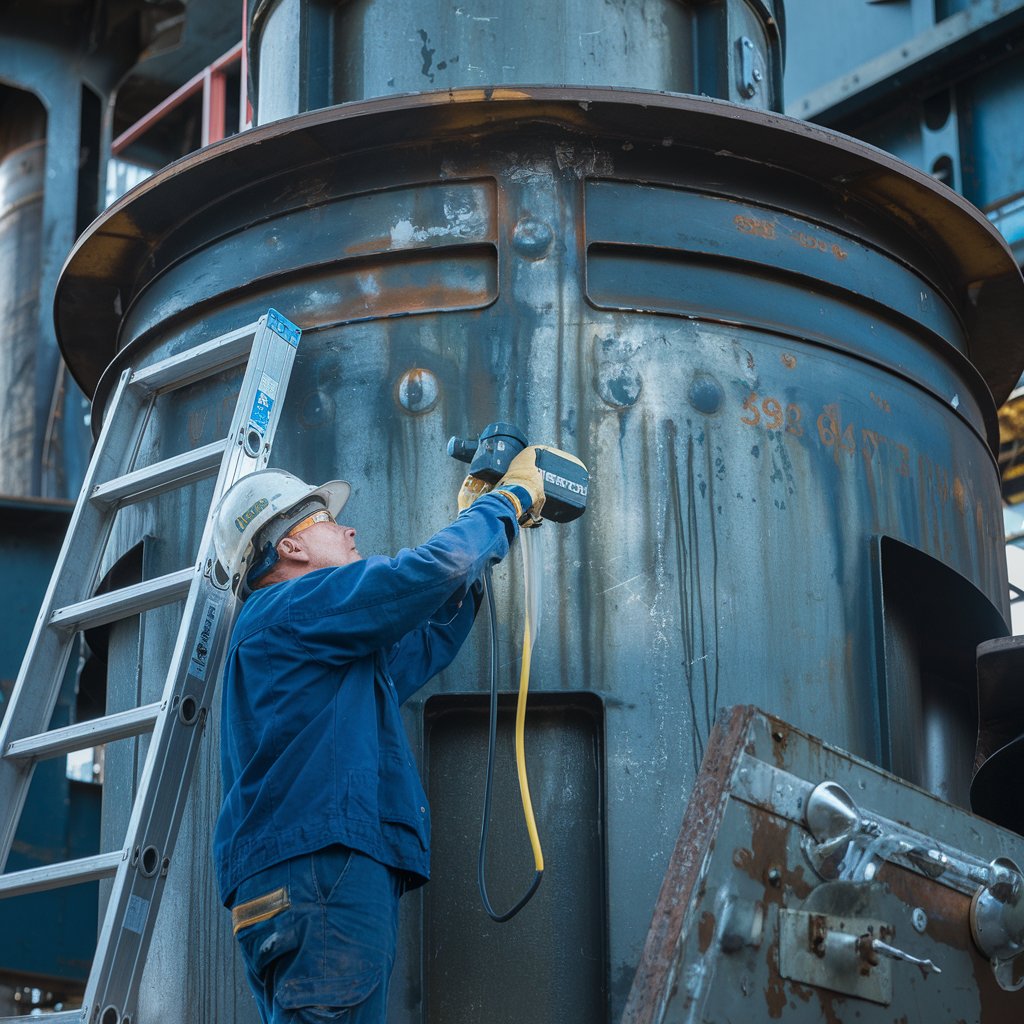
IoT and Its Impact on NDT and Inspection
The integration of the Internet of Things (IoT) with NDT and inspection processes further enhances the efficiency of monitoring and diagnostics. IoT-enabled sensors and devices can be attached to machinery, infrastructure, and equipment to continuously monitor their condition in real time. These sensors can collect critical data, such as temperature, pressure, vibration, and wear levels, and transmit it to cloud-based platforms for analysis.
This constant flow of real-time data allows for predictive maintenance, where potential issues can be identified before they cause major failures. For instance, IoT sensors can monitor the structural integrity of bridges or pipelines, sending alerts when there is unusual wear or stress, which can then trigger an automatic inspection or maintenance schedule. This reduces the reliance on periodic manual inspections and allows organizations to respond to issues promptly, saving both time and costs.
Furthermore, IoT in the NDT industry enables remote monitoring and inspections, which is especially valuable for hazardous or hard-to-reach environments, such as offshore oil rigs or deep-sea equipment. Inspectors can access data from anywhere in the world and make informed decisions based on real-time information, improving safety and efficiency.
Synergy Between AI and IoT
The true potential of AI and IoT in NDT and inspection is realized when these technologies work together. AI can process the vast amounts of data generated by IoT sensors, providing real-time insights and predictive analytics to optimize maintenance schedules and asset performance. For example, an IoT-enabled industrial robot performing NDT on a manufacturing line can relay inspection data to an AI system, which then analyzes the data to detect defects and determine necessary actions.
This combination not only enhances the accuracy of inspections but also streamlines the entire process, reducing the need for manual intervention and improving decision-making. Additionally, AI can help in managing the data from multiple IoT sensors by filtering, interpreting, and presenting it in actionable formats, allowing engineers and maintenance teams to focus on high-priority issues.
Industry Growth and Future Prospects
The rapid advancements in AI and IoT technologies are driving the growth of the NDT and inspection industry, as more organizations are adopting these solutions to enhance productivity, safety, and compliance with regulations. Industries such as aerospace, automotive, manufacturing, energy, and infrastructure are leading the way in embracing these technologies, with significant investments in automated inspection systems, smart sensors, and AI-driven analysis tools.
In the coming years, The NDT and inspection industry is expected to reach USD 18.4 billion by 2029 from 11.6 billion in 2024, at a CAGR of 9.6% during the 2024-2029 period. with the integration of AI and IoT playing a pivotal role in this expansion. The demand for more sophisticated, accurate, and efficient inspection methods will continue to increase, creating opportunities for technology providers and service companies to innovate and develop new solutions.
The increasing adoption of Industry 4.0 principles, which include automation, smart manufacturing, and the use of connected devices, will further accelerate the need for AI and IoT integration in the NDT and inspection industry. As industries continue to embrace digital transformation, the market for AI and IoT-powered inspection solutions is set to grow, bringing greater value to stakeholders across the value chain.
The integration of AI and IoT in the NDT and inspection industry is a game-changer, enhancing the accuracy, speed, and efficiency of inspection processes while reducing costs and downtime. As these technologies evolve, the industry is witnessing a shift toward more automated, real-time, and predictive maintenance solutions. Companies that embrace these advancements will not only improve operational efficiency but also stay ahead in a competitive landscape, ensuring long-term sustainability and growth. The future of NDT and inspection lies in the intelligent fusion of AI, IoT, and traditional inspection methods, paving the way for safer, smarter, and more efficient industries across the globe.
The report profiles major players in the NDT and Inspection companies are General Electric (US), MISTRAS Group (US), Olympus Corporation (Japan), Ashtead Technology (Scotland), Nikon Metrology NV (UK), SGS Société Générale De Surveillance SA, (Switzerland), Magnaflux (US), Eddyfi Technologies (Canada), Sonatest (UK), Intertek Group plc (UK), Applus+ (Spain), Bureau Veritas (France), Comet Group (Switzerland), TUV Rheinland (Germany), FISCHER TECHNOLOGY INC. (US), Acuren (US), CREAFORM (Canada), Vidisco Ltd. (Israel), DEKRA (Germany), Team, Inc. (US), Labquip NDT (US), Cygnus Instruments Ltd. (UK), FPrimeC Solutions Inc. (Canada), Carestream Health (US), and Element Materials Technology (UK).
Frequently Asked Questions (FAQ)
1. What is Non-Destructive Testing (NDT)?
NDT is a method used to evaluate the properties or integrity of materials, components, or structures without causing damage to them. It is widely used in industries such as aerospace, manufacturing, energy, and automotive to detect flaws, corrosion, and other defects.
2. How is AI used in NDT and inspection?
AI in NDT is used to automate the analysis of inspection data. Machine learning algorithms can process large amounts of data from various sensors, detect patterns, and identify defects more accurately and faster than traditional methods. AI is particularly beneficial for tasks such as visual inspections, anomaly detection, and predictive maintenance.
3. What role does IoT play in NDT and inspection?
IoT in NDT involves the use of connected sensors embedded in equipment and structures to continuously monitor their condition in real-time. This allows for predictive maintenance, early detection of potential issues, and remote monitoring of assets, reducing the need for manual inspections.
4. How do AI and IoT work together in NDT and inspection?
AI and IoT work together by leveraging real-time data collected from IoT-enabled sensors and using AI algorithms to analyze and interpret that data. This collaboration enables faster, more accurate decision-making, predictive maintenance, and optimization of inspection processes.
5. What industries benefit from AI and IoT in NDT and inspection?
Several industries benefit from AI and IoT advancements in NDT, including aerospace, automotive, energy, manufacturing, construction, and infrastructure. These technologies help enhance safety, reduce downtime, and optimize maintenance processes in critical environments.