Industrial agitators are essential in many sectors, providing the necessary mixing and blending to achieve consistency, efficiency, and product quality. Their diverse applications span across food and beverage, pharmaceuticals, chemical manufacturing, oil and gas, wastewater treatment, and cosmetics. This article delves deeper into each of these industries, highlighting how industrial agitators contribute to processes and product outcomes.
Industrial Agitators Industry Overview
The industrial agitators market size is expected to reach USD 3.2 billion by 2028 from USD 2.6 billion in 2023, at a CAGR of 4.0 % during the 2023–2028 period. The major factors driving the market growth of the industrial agitators market include increasing demand for homogeneous mixing, growing need for energy efficient mixing equipment in pharmaceutical, chemical and food & beverage industries, and growing adoption of customized agitators for several applications.
Applications of Industrial Agitators
1. Food and Beverage Industry
Mixing Ingredients
In the food and beverage sector, achieving the perfect blend of ingredients is crucial for product consistency and quality. Industrial agitators are employed to mix a variety of components, including solids, liquids, and powders, ensuring that flavors, colors, and textures are uniform throughout the product. For instance, in the production of sauces and dressings, high-shear mixers create stable emulsions that prevent separation, resulting in a smooth, homogeneous product that meets consumer expectations.
Fermentation Processes
Agitation plays a vital role in fermentation processes, particularly in breweries and wineries. Industrial agitators help maintain uniform conditions within fermentation tanks by ensuring even distribution of yeast and nutrients. This uniformity is essential for optimizing fermentation rates and developing consistent flavor profiles. Moreover, by controlling mixing speed and intensity, operators can influence the production of specific flavor compounds, leading to unique and desirable characteristics in the final product.
Heat Transfer
Agitators also facilitate heat transfer in food processes. In applications such as pasteurization or cooking, effective mixing ensures that heat is uniformly distributed throughout the mixture, preventing hot spots that can lead to uneven cooking or spoilage. This is particularly important for maintaining food safety and quality.
2. Pharmaceutical Industry
Drug Formulation
In pharmaceuticals, the precision of mixing is paramount. Industrial agitators ensure that active pharmaceutical ingredients (APIs) are uniformly dispersed in liquid formulations, such as syrups, suspensions, and emulsions. This uniformity not only affects the efficacy of the drug but also its safety, as inconsistent dosages can lead to adverse effects. Agitators equipped with advanced control systems allow for precise adjustments, ensuring the final product meets strict regulatory standards.
Sterile Mixing
In sterile environments, where the risk of contamination is a significant concern, specialized agitators with aseptic designs are crucial. These agitators maintain sterility while effectively mixing ingredients, ensuring that the final pharmaceutical products are safe for patient use. Technologies such as automated clean-in-place (CIP) systems are often integrated with agitators to ensure thorough cleaning between batches, further reducing contamination risks.
Biopharmaceutical Production
The rise of biopharmaceuticals, which rely on biological processes to produce therapeutic agents, has increased the demand for sophisticated mixing technologies. Industrial agitators in bioreactors promote the growth of microorganisms or cell cultures, ensuring optimal conditions for production. Their design allows for controlled oxygen transfer, mixing, and temperature regulation, all of which are critical for maximizing yield and maintaining product quality.
Download PDF Brochure @
https://www.marketsandmarkets.com/pdfdownloadNew.asp?id=59649096
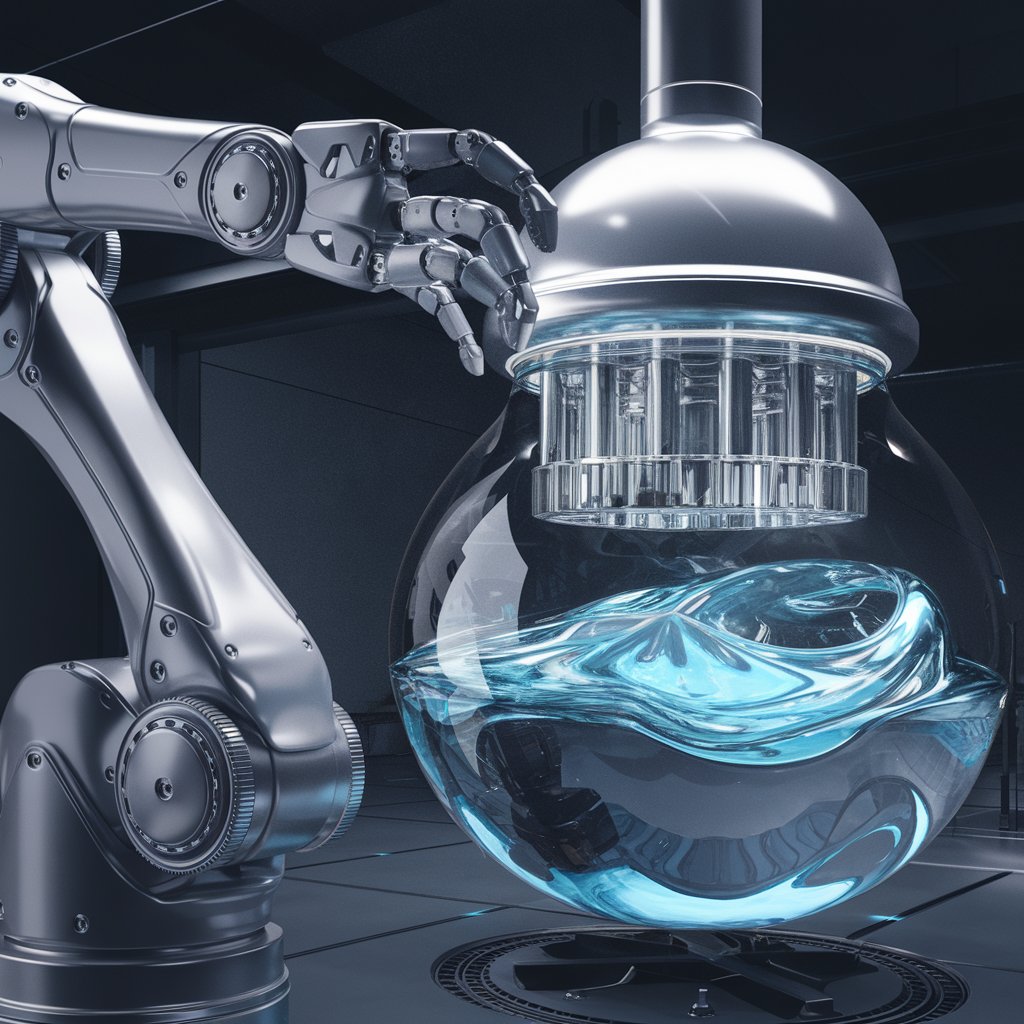
3. Chemical Manufacturing
Reactant Mixing
In the chemical manufacturing process, effective mixing is vital for achieving desired reaction outcomes. Industrial agitators are utilized in reactors to ensure that reactants are thoroughly mixed, promoting uniformity and optimal reaction kinetics. Different types of agitators—such as turbine, anchor, and paddle mixers—are selected based on the physical properties of the materials involved, including viscosity and density. This selection is crucial for optimizing production efficiency and product yield.
Suspension and Dispersion
Industrial agitators are essential in creating stable suspensions and dispersions in industries such as paint, coatings, and polymers. These applications often require the mixing of solids into liquids to form consistent products. For instance, in paint production, agitators ensure that pigments are evenly distributed, preventing sedimentation and ensuring color consistency. This is particularly important in a competitive market where product appearance and quality are key differentiators.
Safety and Environmental Considerations
Chemical manufacturing often involves hazardous materials, making safety a top priority. Industrial agitators are designed to minimize the risk of spills and accidents during mixing operations. Additionally, modern agitator systems are being developed with environmental considerations in mind, focusing on reducing energy consumption and waste generation while maximizing efficiency.
4. Oil and Gas Industry
Enhanced Oil Recovery
In the oil and gas sector, industrial agitators play a critical role in enhanced oil recovery (EOR) methods. These methods often involve the injection of water, chemicals, or steam into oil reservoirs to improve extraction efficiency. Agitators help mix these substances uniformly before injection, enhancing the overall effectiveness of the EOR process. By optimizing the mixing of various fluids, operators can achieve higher oil recovery rates, reducing operational costs and maximizing resource utilization.
Emulsion Breaking
Agitators are also employed in the oil and gas industry for breaking emulsions—mixtures of oil and water that can complicate refining processes. In separation units, future of industrial agitators promote the coalescence of small droplets, facilitating their separation. This is vital for ensuring the purity of the final product and optimizing refining efficiency. By employing the right agitator design and operational parameters, refineries can significantly improve their throughput and reduce waste.
5. Wastewater Treatment
Sludge Mixing
In wastewater treatment facilities, effective mixing is crucial for optimizing anaerobic digestion processes. Industrial agitators are used to mix sludge in digesters, ensuring that the organic matter is uniformly distributed. This uniformity enhances microbial activity, which is essential for breaking down waste and producing biogas. By improving the mixing process, operators can increase biogas production and overall treatment efficiency, contributing to sustainable waste management.
Chemical Dosing
Agitators are also employed in the chemical dosing process within wastewater treatment. They help ensure that coagulants and flocculants are evenly distributed throughout the wastewater, which is essential for effective pollutant removal. The ability to control mixing parameters allows operators to fine-tune chemical dosages based on real-time water quality assessments, optimizing treatment outcomes while minimizing chemical use.
6. Cosmetics and Personal Care
Emulsion Creation
In the cosmetics industry, emulsions are a fundamental part of many products, such as creams, lotions, and serums. Industrial agitators facilitate the creation of stable emulsions by thoroughly mixing oil and water phases. The uniformity achieved through effective agitation ensures that products maintain their desired consistency and effectiveness. High-shear mixers are particularly valuable in this process, as they can create fine emulsions that enhance product texture and application.
Homogenization
Agitators also play a crucial role in the homogenization of cosmetic formulations. This process ensures that active ingredients, such as vitamins and botanicals, are evenly distributed throughout the product. Consistent homogenization is essential for delivering effective results and meeting consumer expectations in a competitive market. Additionally, improved product stability extends shelf life and enhances the overall consumer experience.
Industrial agitators are indispensable tools across a wide range of applications, from food and pharmaceuticals to chemical manufacturing and wastewater treatment. Their ability to ensure uniform mixing and improve process efficiency not only enhances product quality but also supports compliance with industry regulations. As technology continues to advance, the role of industrial agitators will only become more critical in driving innovation and efficiency. By understanding their diverse applications, businesses can leverage industrial agitators to optimize processes, enhance product quality, and achieve operational success.
The report profiles key players such as
- SPX Flow, Inc. (US),
- Xylem Inc. (US),
- Ekato Group (Germany),
- Sulzer Ltd. (Switzerland) and NOV Inc (US).