The Fault Detection and Classification (FDC) market is witnessing substantial growth, driven by the increasing adoption of artificial intelligence (AI) technology. AI-powered FDC systems are transforming the manufacturing landscape by offering advanced solutions for identifying and addressing faults, enhancing quality control, and optimizing production processes. This article explores the market size of AI-based FDC systems, their growing influence, and the benefits they provide to various industries.
Fault detection and classification market size overview
The global fault detection and classification market size was valued at USD 4.4 billion in 2022 and is projected to reach USD 7.4 billion by 2028; it is expected to register a CAGR of 8.9% during the forecast period. Stringent health and safety measures imposed by governments and standards organizations on global manufacturing firms and Strong focus of manufacturers on automating quality control and quality assurance processes are among the factors driving the growth of fault detection and classification market.
Impact of AI Technology on Fault Detection and Classification
- Enhanced Accuracy and Efficiency
AI technology significantly improves the accuracy and efficiency of fault detection and classification. Machine learning algorithms and advanced analytics enable AI systems to identify subtle anomalies and defects with high precision. This enhanced capability reduces the likelihood of errors that may occur with manual inspection, ensuring higher product quality and reliability.
Example: In the semiconductor industry, AI-based systems use deep learning to analyze complex patterns in chip production, identifying defects with greater accuracy than traditional methods and ensuring high yield rates.
- Real-Time Monitoring and Early Detection
AI-powered FDC systems provide real-time monitoring and early detection of faults. These systems continuously analyze data from production processes, allowing for immediate identification of anomalies and swift intervention. Early detection helps prevent defective products from progressing further down the production line, reducing waste and minimizing the risk of costly recalls.
Example: In the automotive industry, AI-driven visual inspection systems detect minute defects in components during assembly, enabling timely corrective actions and preventing potential issues in finished vehicles.
Download PDF Brochure @
https://www.marketsandmarkets.com/pdfdownloadNew.asp?id=15954762
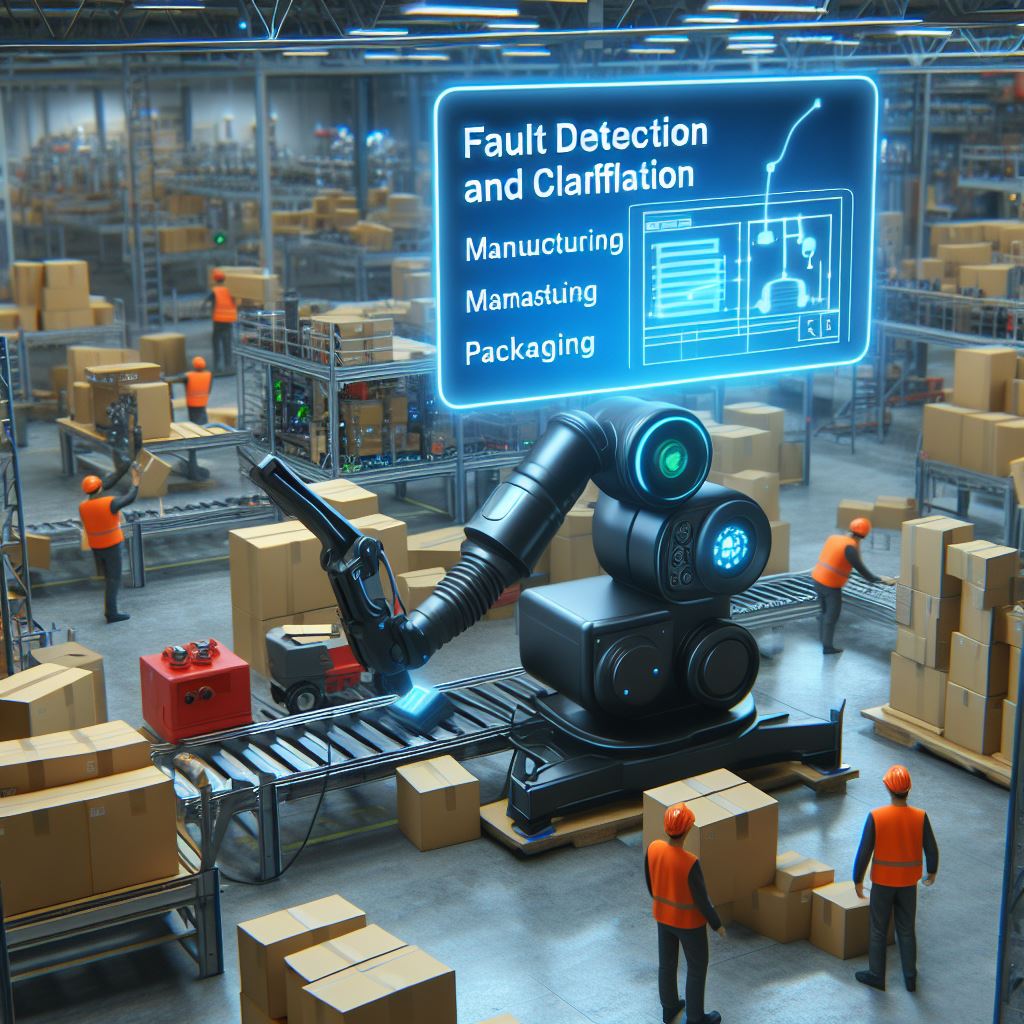
- Data-Driven Insights for Continuous Improvement
AI systems excel in collecting and analyzing large volumes of data, providing valuable insights for continuous improvement. By tracking historical data and identifying patterns, manufacturers can address recurring issues and enhance their quality control processes. This data-driven approach supports informed decision-making and process optimization.
Example: In the aerospace sector, AI-based FDC systems analyze data from aircraft parts manufacturing, helping to identify recurring faults and implement preventive measures to improve overall production quality.
- Streamlined Incoming Material Inspection
Efficient inspection of incoming materials is crucial for maintaining high production standards. AI technology automates this process, ensuring that only materials meeting quality specifications are used in production. This optimization reduces the likelihood of defects caused by substandard raw materials.
Example: In the food and beverage industry, AI systems inspect and classify raw ingredients, ensuring that only high-quality materials are utilized in production, thereby improving the safety and consistency of final products.
- Increased Production Capacity and Quality
AI-based FDC systems enable manufacturers to increase production capacity without compromising quality. By automating fault detection and classification, these systems reduce the need for manual inspection and enable faster, more efficient production processes. This scalability supports higher output while maintaining rigorous quality standards.
Fault detection and classification market size : Future Outlook
The increasing adoption of AI technology in fault detection and classification is set to continue driving market growth. As AI technologies advance and become more accessible, their integration into manufacturing processes will further enhance fault detection capabilities and improve operational efficiency. The focus on AI-driven solutions is expected to expand across various industries, including automotive, aerospace, electronics, and pharmaceuticals, offering significant benefits in quality control and production optimization.
The fault detection and classification market is expanding rapidly, propelled by the growing adoption of AI technologies. AI-based systems offer enhanced accuracy, real-time monitoring, data-driven insights, and streamlined material inspection, leading to improved production quality and efficiency. As industries increasingly leverage AI to address faults and optimize processes, the market for AI-powered FDC systems will continue to grow, shaping the future of manufacturing with innovative solutions and advanced capabilities.
Key Benefits of AI-Based Fault Detection and Classification Systems
- Early Error Detection
AI-based FDC systems excel at early error detection, identifying defects before they progress further down the production line. By continuously monitoring production processes in real-time, these systems can detect anomalies and faults at their inception, preventing defective parts from reaching the final stages of production. This proactive approach helps minimize waste and reduce the risk of costly recalls.
Example: In the automotive industry, AI-based systems can detect minute deviations in parts during assembly, ensuring that only components meeting strict quality standards proceed to the next stage, thus avoiding potential recalls and maintaining high standards.
- Increased Production Volume Without Sacrificing Quality
AI-driven fault detection systems enhance production efficiency by enabling manufacturers to increase their output while maintaining or even improving product quality. These systems optimize the production process by quickly identifying and addressing issues, allowing for faster adjustments and reducing downtime.
Example: In electronics manufacturing, AI-based systems can rapidly analyze and classify defects in circuit boards, allowing for higher throughput without compromising the accuracy or reliability of the finished products.
- Historical Data Tracking for Continuous Improvement
AI-based FDC systems offer valuable insights through historical data tracking. By analyzing past production data, manufacturers can pinpoint recurring issues, understand their root causes, and make informed decisions to improve future production processes. This data-driven approach helps in refining quality control measures and enhancing overall operational efficiency.
Example: In the pharmaceutical industry, historical data analysis can reveal patterns in equipment malfunctions or process deviations, enabling manufacturers to implement preventive measures and improve the consistency of drug production.
- Optimized Incoming Material Inspection
Efficient incoming material inspection is crucial for maintaining high product quality. AI-based FDC systems streamline this process by providing accurate and automated analysis of raw materials. This ensures that only materials meeting specified standards are used in production, reducing the risk of defects caused by substandard inputs.
Example: In the food and beverage industry, AI systems can inspect and classify raw ingredients, ensuring that only high-quality materials are used in production, thus improving the consistency and safety of the final products.
- Reaching and Surpassing Human-Level Accuracy
One of the most compelling advantages of AI-based FDC systems is their ability to achieve, and often surpass, human-level accuracy in fault detection and classification. Advanced machine learning algorithms and computer vision technologies enable these systems to detect and classify defects with high precision, reducing the likelihood of human error and enhancing overall quality control.
Top Fault Detection and Classification (FDC) Companies – Key Market Players:
- Keyence Corporation (Japan),
- Cognex Corporation (US),
- KLA Corporation (US),
- Teledyne Technologies (US),
- OMRON Corporation (Japan),
- Microsoft (US),
- Tokyo Electron Limited (Japan),
- Siemens (Germany),
- Amazon Web Services, Inc. (US),
- Synopsys, Inc. (US) are some of the key players in the fault detection and classification companies.