Artificial Intelligence (AI) has ushered in a new era of technological innovation across various industries, and the industrial agitators market is no exception. Industrial agitators play a critical role in sectors such as chemicals, pharmaceuticals, food and beverage, water treatment, and many others, facilitating the mixing, blending, and dispersion of materials. However, these operations have traditionally been limited by mechanical constraints, manual adjustments, and human oversight. With AI’s integration, industrial agitators are experiencing a significant transformation—one that optimizes their performance, enhances efficiency, and improves sustainability across processes.
Industrial Agitators Market Overview
The global industrial agitators market size is expected to be valued at 3.10 billion in 2024 and is projected to reach 3.99 billion by 2029; it is expected to grow at a CAGR of 5.2 % from 2024 to 2029
Improved Operational Efficiency with AI-Powered Agitation
The main objective of industrial agitators is to achieve the perfect blend of ingredients or materials in the most energy-efficient manner. Traditionally, the speed, rotation, and mixing patterns of industrial agitators were adjusted manually or based on predetermined settings. However, this approach often resulted in inefficiencies and variability in the final product.
AI is now revolutionizing this process by enabling real-time adjustments and optimization. With the help of AI-powered algorithms and machine learning models, industrial agitators can adapt to varying parameters, such as material viscosity, temperature, and pressure, to maintain optimal mixing performance at all times. Through the collection of continuous operational data, AI algorithms analyze real-time conditions and fine-tune the agitator’s settings for maximum energy efficiency and minimal material waste. This ensures that every batch produced is consistent, of high quality, and made with fewer resources, leading to significant operational savings.
Predictive Maintenance and Enhanced Asset Longevity
Predictive maintenance is one of the most powerful applications of AI in industrial systems, and industrial agitators are no different. By continuously monitoring equipment health through IoT-enabled sensors, AI can detect early signs of wear, corrosion, or imbalance in agitator components such as motors, blades, seals, and bearings.
AI-powered systems analyze data such as vibration, temperature, and power consumption to assess the condition of individual components. Machine learning algorithms then identify anomalies and predict potential failures before they occur. This allows manufacturers to schedule maintenance at optimal times, reducing the chances of unexpected downtime, costly repairs, and production disruptions. Predictive maintenance not only extends the lifespan of agitators but also helps companies avoid expensive emergency repairs, which can significantly impact overall production schedules.
By anticipating and preventing mechanical failures, AI also ensures that the agitators are always operating at peak performance, further optimizing efficiency.
AI-Driven Process Optimization and Data Analysis
In addition to improving operational performance and maintenance schedules, AI provides businesses with invaluable insights through data analysis. The real-time collection of operational data—from sensors embedded in agitators—generates huge volumes of information. These data points can include pressure, temperature, viscosity, and other relevant parameters of the mixing process.
AI-driven systems can analyze this data using advanced machine learning models to detect patterns and correlations that human operators might miss. This analysis helps operators understand optimal mixing conditions for different materials, improving product quality and reducing wastage.
Furthermore, AI’s ability to continuously monitor and analyze the performance of industrial agitators enables manufacturers to identify inefficiencies. For example, AI can uncover processes where energy consumption is unnecessarily high, material usage is suboptimal, or the mixing process could be more uniform. By highlighting these inefficiencies, AI allows companies to make informed decisions and implement improvements to reduce operational costs while improving the final product quality.
Download PDF Brochure @
https://www.marketsandmarkets.com/pdfdownloadNew.asp?id=59649096
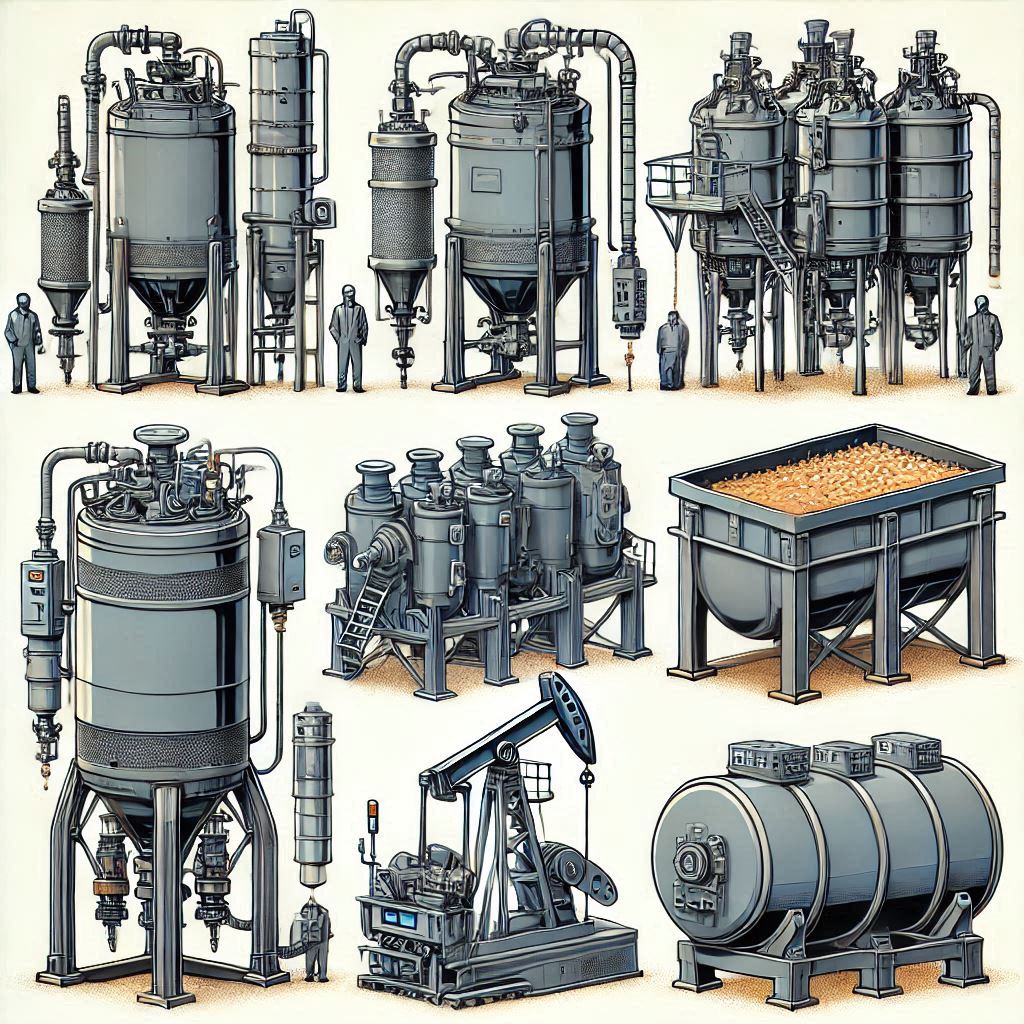
Integration with IoT and Automation for Smarter Operations
The convergence of AI with the Internet of Things (IoT) has accelerated the shift toward fully automated industrial systems, and industrial agitators are a key part of this trend. IoT-enabled sensors placed on agitators gather real-time data on critical parameters, such as viscosity, pressure, motor speed, and flow rates. These sensors then feed the data to AI systems that analyze and make automated adjustments to optimize the agitator’s performance.
By integrating AI with automation, businesses can achieve a level of precision and efficiency in the mixing process that was previously unattainable. For example, if the viscosity of a liquid changes during the process, AI can automatically adjust the speed or torque of the agitator to maintain a uniform mixture. This minimizes the need for manual interventions, reduces human error, and ensures that the process remains consistent and reliable.
AI’s integration with automation also offers scalability for industrial agitators. As manufacturing facilities expand and production volumes increase, AI can easily accommodate the growing complexity of operations, adjusting parameters dynamically and ensuring smooth operation without the need for additional manual input.
Driving Sustainability in Industrial Agitation
Sustainability is becoming a significant focus for businesses across the industrial sector, and AI is helping to make industrial agitators more environmentally friendly and energy-efficient. One of the main ways AI contributes to sustainability is by optimizing energy consumption. Traditionally, agitators run at fixed speeds regardless of the conditions in the tank. This leads to wasted energy when mixing is unnecessary or when the material properties change.
With AI, industrial agitators can adjust their energy usage based on real-time conditions. For instance, if the material being mixed has lower viscosity, the agitator can automatically reduce speed, resulting in energy savings. AI can also analyze the entire production process and provide suggestions for improving energy efficiency and reducing waste, helping companies minimize their carbon footprint.
Moreover, AI-driven systems ensure more precise mixing, reducing the amount of material wasted during the process. This improved precision leads to higher yields, reducing the need for additional raw materials and contributing to a more sustainable production model.
Challenges to Overcome
While the integration of AI into industrial agitators brings immense benefits, there are certain challenges that must be addressed. For instance, the initial cost of implementing AI-powered systems can be high, especially for small and medium-sized enterprises (SMEs). However, this upfront investment is often offset by the long-term savings in energy, maintenance costs, and operational efficiencies.
There are also challenges related to the complexity of integrating AI with existing systems. Manufacturers must invest in necessary infrastructure such as IoT sensors, data management platforms, and AI software to fully leverage AI’s potential. Furthermore, operators must be trained to understand and use these AI systems, which may require an initial learning curve.
The Future of AI in Industrial Agitators
The potential for AI in industrial agitators is still being explored. As technology continues to advance, future innovations in AI could include self-learning systems that can continuously improve the mixing process based on historical data and evolving production needs. With the future integration of AI, IoT, and automation, industrial agitators could evolve into fully autonomous, highly efficient systems capable of running with minimal human intervention.
Ultimately, AI is poised to reshape the industrial agitator market, making these systems smarter, more efficient, and more sustainable. The benefits of reduced operational costs, improved product consistency, enhanced performance, and longer equipment life will drive widespread adoption of AI-powered industrial agitators in the coming years.
AI is revolutionizing the industrial agitators market by enhancing operational efficiency, enabling predictive maintenance, offering data-driven insights, and supporting sustainability. As AI technology advances, its integration into industrial processes will continue to drive innovation, delivering value to industries that rely on agitation systems for mixing, blending, and dispersing materials. By embracing AI, businesses can future-proof their operations, improve product quality, and achieve higher levels of efficiency—making AI an essential component in the next generation of industrial agitators
Here are some frequently asked questions (FAQ) about the impact of AI on the industrial agitators market:
1. How is AI improving the efficiency of industrial agitators?
AI improves the efficiency of industrial agitators by enabling real-time adjustments to parameters such as speed, rotation, and mixing patterns. AI algorithms analyze data like viscosity, temperature, and pressure, allowing agitators to adapt to changing material properties and ensuring optimal performance while minimizing energy consumption and material waste.
2. What is predictive maintenance, and how does AI contribute to it?
Predictive maintenance is a strategy that uses AI to monitor equipment health in real time and predict potential failures before they occur. Through sensors, AI collects data on agitator components, such as motors and blades, analyzing signs of wear or imbalance. This allows operators to schedule maintenance before critical failures happen, reducing downtime and avoiding costly repairs.
3. Can AI optimize energy usage in industrial agitators?
Yes, AI can optimize energy usage by dynamically adjusting the agitator’s speed and power consumption based on the specific conditions of the material being processed. For example, if the viscosity of the material decreases, the AI system can reduce the speed, leading to significant energy savings and reduced operational costs.
4. How does AI enhance product quality in the mixing process?
AI enhances product quality by constantly monitoring the mixing process, ensuring that the materials are blended consistently and according to the desired specifications. By analyzing real-time data from sensors, AI can make adjustments to improve uniformity and eliminate inconsistencies in the final product, which is crucial for industries like food, chemicals, and pharmaceuticals.
5. What industries benefit from AI-powered industrial agitators?
AI-powered industrial agitators benefit a wide range of industries, including chemicals, pharmaceuticals, food and beverage, oil and gas, and water treatment. These sectors rely on precise mixing and blending processes to maintain product quality, improve efficiency, and reduce operational costs.
6. What are the potential challenges in integrating AI into industrial agitators?
The main challenges include the high initial investment in AI technology, including sensors, data management platforms, and AI software. Additionally, integrating AI with existing systems can be complex, and workers may need training to understand and use the new technology effectively. However, the long-term benefits, such as reduced downtime, improved efficiency, and better product quality, can justify the initial investment.
7. How does AI help in sustainability for industrial agitators?
AI contributes to sustainability by optimizing energy consumption, reducing material waste, and improving the efficiency of the mixing process. Through AI, agitators can adjust their operations to consume less energy during mixing, especially when the material properties change, resulting in lower environmental impact and cost savings.
8. Can AI-driven industrial agitators work autonomously?
Yes, AI-driven industrial agitators can be integrated with automation systems, making them capable of operating autonomously with minimal human intervention. By continuously adjusting to real-time conditions and processing data, AI systems can ensure that the agitators run at peak efficiency without the need for constant oversight.
9. How will the future of AI in industrial agitators evolve?
As AI technology continues to evolve, industrial agitators will become more self-learning, with systems able to improve their performance based on historical data. The future of AI in industrial agitators will likely involve greater integration with IoT and automation, leading to smarter, more efficient, and highly reliable systems.