The aerospace and defense industries are constantly evolving, driven by the need for more efficient, reliable, and compact systems. Piezoelectric devices have become an essential technology in these sectors, offering groundbreaking capabilities for energy generation, sensing, and actuation. By converting mechanical stress or vibrations into electrical energy (and vice versa), piezoelectric materials and devices are enabling new levels of performance, efficiency, and sustainability. This article explores how piezoelectric devices are transforming aerospace and defense technologies, enhancing operational capabilities, and contributing to the development of next-generation systems.
What are Piezoelectric Devices?
Piezoelectric devices use materials that generate an electric charge when subjected to mechanical stress. Conversely, they also change shape or deform when an electric field is applied to them. This unique property of piezoelectric materials—such as PZT (lead zirconate titanate), PVDF (polyvinylidene fluoride), and other ceramics and polymers—makes them invaluable in a range of applications that require sensing, actuation, and energy conversion.
In the aerospace and defense sectors, piezoelectric devices can be used for:
- Energy harvesting from vibrations or mechanical motion
- Sensing mechanical stress, strain, or pressure
- Actuation for precise movements in controls or propulsion systems
Piezoelectric Devices Industry Outlook
The piezoelectric devices industry is projected to grow from USD 32.7 billion in 2023 and is projected to reach USD 46.0 billion by 2028; it is expected to grow at a CAGR of 7.0% from 2023 to 2028.Increasing adoption of piezoelectric devices in energy harvesting is one of the major driver of the market.
Applications of Piezoelectric Devices in Aerospace
The aerospace industry is heavily focused on weight reduction, power efficiency, and the optimization of materials and systems. Piezoelectric devices offer numerous advantages in achieving these goals, with applications spanning from structural health monitoring to energy harvesting and active vibration control.
1. Structural Health Monitoring
One of the key uses of piezoelectric materials in aerospace is for structural health monitoring (SHM). Airplanes, spacecraft, and other aerospace vehicles are subject to constant stress from forces such as wind, turbulence, and vibration. Detecting damage or wear in critical components early can be crucial for safety, performance, and maintenance scheduling.
Piezoelectric sensors are embedded into structures (such as wings, fuselages, and engines) to continuously monitor stress, strain, and potential damage. When mechanical stress is applied to a piezoelectric material, it generates a voltage, which can be measured and used to detect cracks, deformations, or other issues in the structure. This continuous monitoring can prevent costly repairs and ensure safety by catching faults before they become catastrophic.
- Example: A piezoelectric sensor embedded in the wing structure of an aircraft can detect tiny deformations or cracks in real-time. If the sensor detects a strain beyond a threshold, it sends an alert to the pilot or maintenance team, ensuring immediate action is taken.
2. Active Vibration Control
In aircraft, vibrations from engines, airflows, and other mechanical components can cause discomfort for passengers, affect operational efficiency, and even lead to mechanical wear over time. Piezoelectric devices are increasingly used for active vibration control to reduce these unwanted vibrations.
By embedding piezoelectric materials in critical parts of the aircraft, such as the wings, control surfaces, or cockpit interiors, it’s possible to counteract vibrations using active damping. These piezoelectric systems can detect vibrations in real-time and generate opposing forces that reduce or eliminate the disruptive effects of vibrations, improving both comfort and structural integrity.
- Example: A piezoelectric actuator can be attached to the tail of an aircraft. It would continuously monitor vibrations caused by engine operation and produce counteracting forces to stabilize the aircraft, reducing stress on the structure and improving fuel efficiency.
3. Energy Harvesting for Autonomous Systems
Autonomous systems in aerospace, such as drones and satellites, require efficient power sources to operate in remote environments. Piezoelectric energy harvesting is increasingly used in aerospace applications to generate electrical power from vibrations and motion, extending the operational lifespan of these systems.
Drones, for example, experience vibrations from their motors and propellers. By integrating piezoelectric devices into the drone’s structure, these vibrations can be converted into usable electrical energy to power sensors, communication systems, or even the drone’s own flight control systems. This reduces reliance on traditional battery power, which is often limited and requires frequent recharging.
- Example: Piezoelectric energy harvesters embedded in the fuselage of a drone could capture the energy from engine vibrations and convert it into electricity, which can be stored and used to power the drone’s internal electronics or navigation systems, enabling longer flight times and more autonomy.
Download PDF Brochure @ https://www.marketsandmarkets.com/pdfdownloadNew.asp?id=256019882
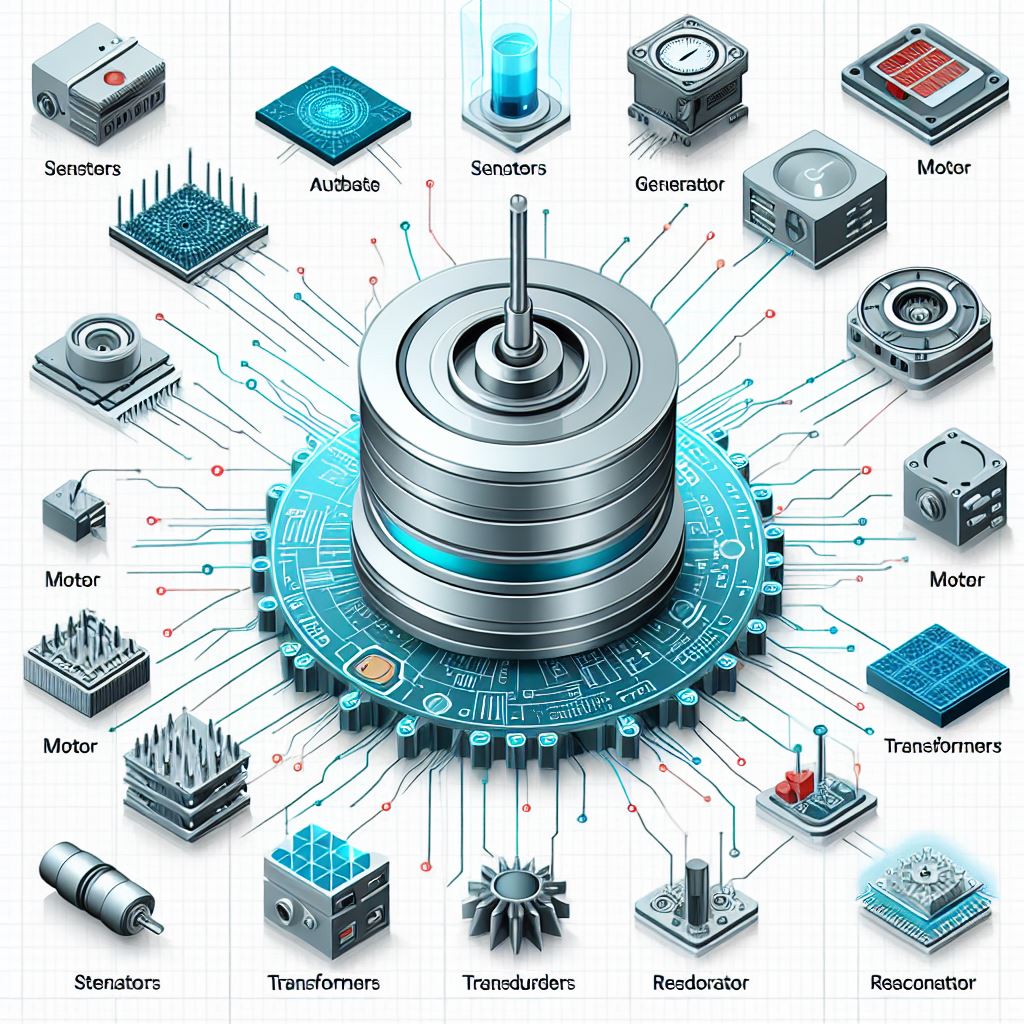
Applications of Piezoelectric Devices in Defense
The defense industry relies on high-performance materials and systems for critical applications, including weaponry, communication, navigation, and surveillance. Piezoelectric devices offer a range of capabilities that meet the high demands of defense systems, enabling better control, energy efficiency, and safety.
1. Sensing and Monitoring Systems
In defense, piezoelectric sensors are used extensively for pressure, vibration, and acoustic sensing. These sensors can be embedded in a variety of military equipment, from tanks and armored vehicles to weapons and surveillance systems, providing real-time information about the condition of systems, environmental conditions, and potential threats.
- Example: Piezoelectric sensors placed inside a military vehicle can monitor vibration levels, which may indicate mechanical failures or issues with the vehicle’s components. Additionally, acoustic sensors made from piezoelectric materials can detect sounds of enemy movement or incoming artillery, giving soldiers real-time alerts.
2. Actuation Systems for Weaponry and Control Surfaces
In military aircraft, drones, and missiles, precise control is crucial for success in operations. Piezoelectric actuators can be used in control surfaces (such as ailerons, rudders, and flaps) to provide highly accurate and fast responses. These actuators can respond to electronic signals with minimal power requirements, offering precise control over flight paths or missile guidance systems.
- Example: Piezoelectric actuators could be integrated into the control systems of a missile to make real-time adjustments to its trajectory, ensuring maximum precision in targeting and mission success.
3. Underwater Applications:
Piezoelectric materials are also used in sonar systems and underwater sensors, providing a compact and efficient means of detecting vibrations and sound waves in marine environments. These systems are essential in defense for underwater surveillance, detecting submarines, or monitoring underwater infrastructures.
- Example: Piezoelectric transducers are commonly used in sonar systems to detect objects and measure distances underwater. The ability of piezoelectric materials to operate in harsh underwater conditions makes them ideal for naval defense applications, including submarines and marine surveillance systems.
Advantages of Piezoelectric Devices in Aerospace and Defense
- Lightweight and Compact: Piezoelectric devices are typically small and lightweight, which is a significant advantage in the aerospace and defense sectors where space and weight limitations are critical.
- Energy Efficiency: Piezoelectric devices are highly efficient at converting mechanical energy into electrical energy, making them valuable for autonomous systems where power consumption must be minimized.
- Real-time Monitoring: The ability to monitor mechanical stress, strain, and vibrations in real-time enables preventive maintenance, improved safety, and enhanced performance.
- Precision Control: Piezoelectric actuators offer extremely fast and accurate control over systems, crucial for aerospace and defense applications that require rapid response times.
- Durability: Piezoelectric materials are known for their robustness and durability in challenging environments, including extreme temperatures, pressure variations, and high-impact conditions, making them ideal for aerospace and defense applications.
Future Prospects of Piezoelectric Devices in Aerospace and Defense
The potential for piezoelectric devices in the aerospace and defense industries is vast and continues to grow as technology advances. Ongoing research into new piezoelectric materials, such as flexible polymers, lead-free ceramics, and nanomaterials, promises to enhance the efficiency and performance of piezoelectric systems.
Key developments to watch include:
- Integration with smart materials: Piezoelectric devices will be increasingly integrated with other smart materials (e.g., shape-memory alloys or self-healing materials) to create systems that can adapt and respond to dynamic environments.
- Miniaturization and energy efficiency: With the miniaturization of piezoelectric devices and advancements in energy storage technologies, these systems will become even more efficient, providing longer operational times for drones, satellites, and unmanned systems.
- Autonomous and hybrid systems: Piezoelectric devices will play a key role in the next-generation autonomous systems, enabling energy harvesting, sensing, and actuation functions without the need for frequent battery replacements.
Piezoelectric devices are poised to play an increasingly significant role in the aerospace and defense industries. By providing efficient solutions for energy harvesting, structural health monitoring, active vibration control, and precision actuation, these devices help to optimize performance, reduce weight, and improve reliability. As aerospace and defense technologies continue to evolve, piezoelectric materials will remain at the forefront of innovation, powering the next generation of autonomous, energy-efficient, and high-performance systems. With ongoing advancements in materials science and system integration, the future of piezoelectric devices in these industries looks promising, offering new possibilities for both military and civilian applications.