The Industrial Automation (IA) sector has been undergoing a transformation in recent years, driven by advances in technology that enhance efficiency, precision, and decision-making. One of the most vital components in this revolution is the Digital Signal Processor (DSP). DSPs are integral in improving automation systems’ performance by enabling real-time data processing and analysis. As industries increasingly rely on sensors, smart devices, and machine learning algorithms, DSPs play a critical role in streamlining operations, reducing downtime, and enhancing product quality.
In this article, we explore how Digital Signal Processors are influencing the Industrial Automation industry and driving innovation across a variety of applications.
Understanding Digital Signal Processors (DSPs)
A Digital Signal Processor (DSP) is a specialized microprocessor designed specifically for the manipulation of signals, including sound, images, and other data forms. Unlike general-purpose processors, DSPs are optimized for mathematical operations and are highly efficient at processing large volumes of data in real-time. This makes them ideal for industrial applications where speed, accuracy, and reliability are critical.
In industrial automation, DSPs typically work alongside programmable logic controllers (PLCs), sensors, and control systems to process signals from machinery, sensors, and other devices, enabling real-time feedback and adjustments in the production process.
The Digital Signal Processor Market growth is projected to grow from USD 10.1 billion in 2024 and is estimated to reach USD 14.7 billion by 2029; it is expected to grow at a Compound Annual Growth Rate (CAGR) of 7.8% from 2024 to 2029. The growth of the Digital Signal Processor industry is driven by surging adoption of Internet of Things (IoT) and connected devices; increasing trend of digital signal processing in automotive industry; improvements in 5G technology and development of advanced communication infrastructure; and rising demand for Voice over Internet Protocol (VoIP) and Internet Protocol (IP) video services.
Key Applications of DSPs in Industrial Automation
- Real-Time Process Control DSPs are essential in real-time process control systems, such as those used in manufacturing plants and production lines. They process signals from various sensors (e.g., temperature, pressure, flow rate) to provide instantaneous feedback to control systems. This ensures that machines and production processes operate within predefined parameters, improving efficiency and product consistency.Example: In a chemical plant, DSPs can process data from temperature and pressure sensors in real-time, adjusting the flow of raw materials to optimize the reaction process, leading to better product quality and energy savings.
- Predictive Maintenance Predictive maintenance is one of the most significant advancements in the industrial automation industry, and DSPs play a pivotal role in enabling it. By processing data from sensors embedded in machinery, DSPs can identify signs of wear and tear or impending failure before they result in significant damage or downtime.Example: DSPs can analyze vibration signals from motors and other rotating machinery to detect abnormalities such as imbalance, misalignment, or bearing failure. By detecting these issues early, companies can schedule maintenance proactively, reducing downtime and maintenance costs.
- Image and Vision Processing Machine vision systems rely on DSPs for image processing and pattern recognition. In industrial automation, machine vision is used for quality control, defect detection, and object tracking. DSPs process high-resolution images from cameras or other optical devices to detect flaws or anomalies in products moving through the production line.Example: In a quality inspection system, DSPs process images of products to identify defects, such as scratches, dents, or color inconsistencies. This enables automated sorting and rejection of defective items, maintaining high production standards and reducing waste.
- Sensor Fusion and Data Integration Industrial automation systems often rely on multiple sensors to monitor various parameters like temperature, pressure, humidity, and vibration. DSPs facilitate sensor fusion, where data from different sensors is combined to provide a more accurate and comprehensive picture of the system’s status.Example: In an automated assembly line, DSPs integrate data from vision sensors, temperature sensors, and force sensors to assess the quality of an assembly process. This fusion of data allows for more informed decision-making, ensuring that the assembly process is both precise and efficient.
- Signal Filtering and Noise Reduction In industrial environments, sensors and machinery often generate noisy or distorted signals that can interfere with data accuracy. DSPs are equipped with advanced filtering and noise reduction algorithms to clean up these signals, ensuring more reliable data.Example: In an automated welding process, DSPs process signals from welding equipment to eliminate electrical noise or irregularities that may affect the quality of the weld. This improves consistency and safety in the welding process.
Download PDF Brochure @ https://www.marketsandmarkets.com/pdfdownloadNew.asp?id=794
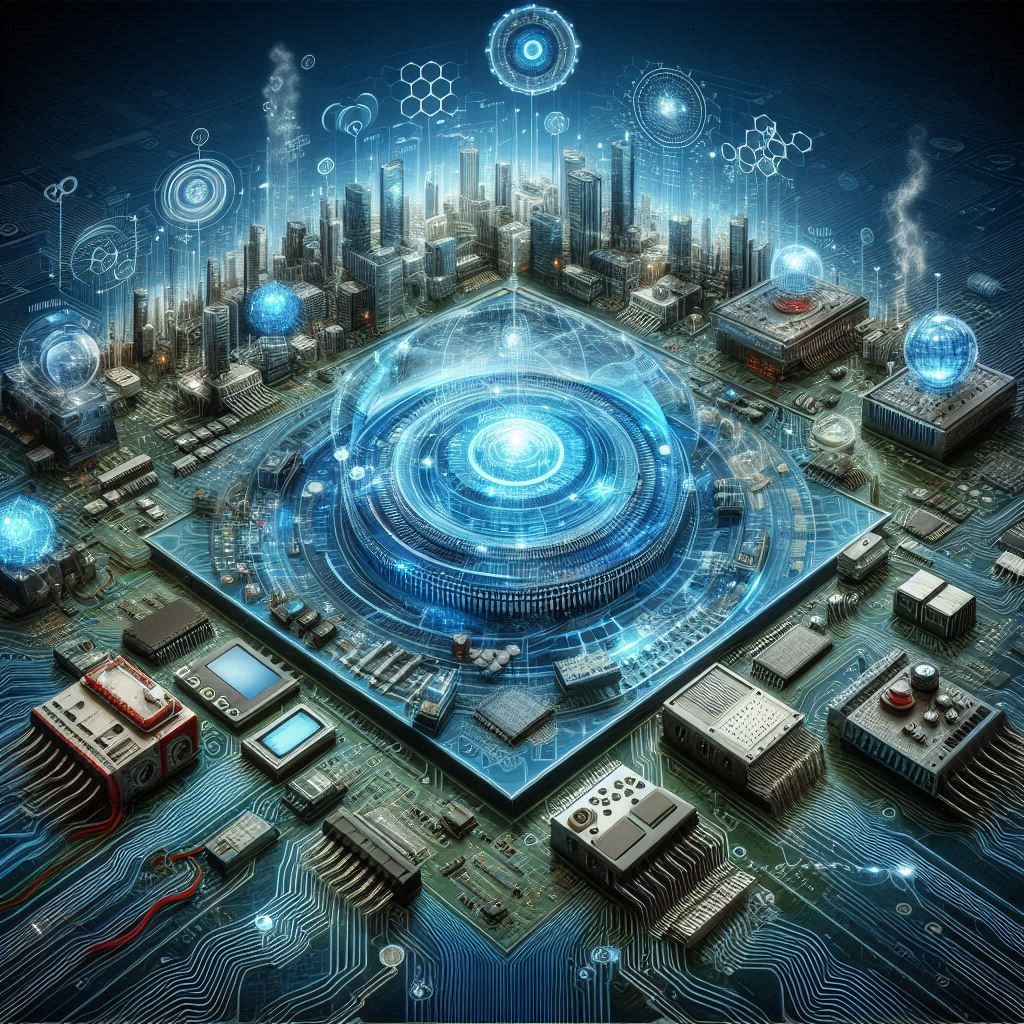
Benefits of DSPs in Industrial Automation
- Enhanced Efficiency and Accuracy DSPs improve the speed and accuracy of real-time data processing. In automated industrial environments, this translates into better control over processes, leading to increased production efficiency, minimized errors, and optimized resource usage.
- Lower Operational Costs By enabling predictive maintenance and minimizing downtime, DSPs help reduce the costs associated with unplanned machine failures. Furthermore, DSPs optimize energy consumption by fine-tuning equipment and production processes.
- Improved Product Quality DSPs contribute to higher product quality by enabling precise control over manufacturing parameters. Automated inspection and defect detection further ensure that only products meeting quality standards are produced.
- Scalability DSPs support scalable systems in industrial automation. As companies expand their production capacity or add new processes, DSPs can be integrated seamlessly into existing systems, ensuring that automation capabilities grow with the business.
Challenges and Future Outlook
While DSPs offer substantial benefits in industrial automation, there are a few challenges that must be addressed to fully unlock their potential:
- Complexity of Integration Integrating DSPs into existing automation systems can be complex, especially for companies with legacy systems. Specialized knowledge of signal processing and automation systems may be required to achieve seamless integration.
- High Initial Investment The initial cost of implementing DSP-based systems can be high, particularly for smaller companies or industries with tight budgets. However, the long-term cost savings through improved efficiency and predictive maintenance often outweigh the upfront costs.
- Evolving Standards and Protocols As the industry continues to adopt Industry 4.0 technologies, there is a growing need for standardization of protocols, communication interfaces, and data formats. DSPs must be adaptable to these evolving standards to ensure compatibility with future of DSP technologies.
Digital Signal Processors (DSPs) are playing an increasingly crucial role in the Industrial Automation industry, enabling businesses to enhance efficiency, improve product quality, and reduce operational costs. As industries continue to integrate smart sensors, AI algorithms, and IoT systems into their automation processes, DSPs will remain at the heart of these advancements.
By enabling real-time signal processing, predictive maintenance, and intelligent control systems, DSPs help companies meet the challenges of modern manufacturing while paving the way for future growth and innovation. As the Industrial Internet of Things (IIoT) and Industry 4.0 continue to evolve, DSPs will be key to driving the next wave of transformation in industrial automation.
FAQ: Digital Signal Processors in the Industrial Automation Industry
1. What is a Digital Signal Processor (DSP)?
A Digital Signal Processor (DSP) is a specialized microprocessor designed to handle and process signals, such as sound, images, and sensor data. Unlike general-purpose processors, DSPs are optimized for mathematical operations, making them ideal for real-time applications that require high-speed processing and accuracy, such as in industrial automation.
2. How does DSP enhance industrial automation?
In industrial automation, DSPs improve real-time process control, predictive maintenance, and machine vision systems. They process data from sensors to provide immediate feedback to control systems, ensuring optimal performance, minimizing downtime, and improving product quality in manufacturing processes.
3. What role does DSP play in predictive maintenance?
DSPs analyze data from equipment sensors in real time to detect early signs of mechanical issues, such as vibrations or temperature fluctuations, that could indicate potential failure. This allows companies to schedule maintenance proactively, preventing costly breakdowns and reducing unplanned downtime.
4. How is DSP used in machine vision systems?
In machine vision systems, DSPs process images captured by cameras to detect defects, track products, or inspect quality. They enable high-speed processing and analysis of image data, allowing for accurate, automated quality checks on production lines, leading to reduced defects and waste.