Sanitary pumps and valves technologies are essential components in industries where cleanliness and safety are paramount, such as food and beverage, pharmaceuticals, and biotechnology. These technologies facilitate the movement and control of fluids while maintaining product integrity and complying with stringent health regulations. This article explores the key technologies in sanitary pumps and valves, highlighting their features, applications, and benefits.
Sanitary Pumps and Valves Industry Outlook
The global sanitary pumps and valves industry size is expected to grow from USD 2.1 billion in 2023 to USD 2.5 billion by 2028, at a CAGR of 3.6% during the forecast period. Sanitary pumps and valves play a key role in preventing slurries or liquids from contamination. These pumps and valves are made of non-corrosive materials, which help prevent alcoholic beverages, nonalcoholic beverages, dairy products, and processed food from viruses, bacteria, chemical substances, and parasites. This functionality has increased the demand for sanitary pumps and valves across various industries.
1. Hygienic Design Principles in Sanitary Pumps and Valves
The primary focus of sanitary pumps and valves technologies is hygiene. Manufacturers incorporate specific design principles to minimize contamination risks:
- Smooth Surfaces: Equipment is designed with smooth surfaces to reduce the likelihood of bacteria adhering. By eliminating rough textures, the risk of cross-contamination during processing is minimized. Smooth surfaces facilitate easier cleaning, ensuring no residue remains after washing.
- Minimal Crevices: Sanitary pumps and valves are constructed to eliminate crevices and dead legs, which can harbor bacteria. This design consideration is crucial in maintaining product safety and quality, as any retained fluid can lead to spoilage or contamination.
- Easy-to-Clean Materials: Materials like stainless steel (commonly 304 or 316L grade) are favored for their resistance to corrosion and ease of cleaning. Manufacturers often apply specialized coatings to enhance these properties, ensuring long-lasting hygiene.
2. Smart Technology Integration in Sanitary Pumps and Valves
The integration of smart technologies into sanitary pumps and valves is revolutionizing their operation and efficiency:
- IoT Connectivity: Many modern sanitary pumps and valves come equipped with Internet of Things (IoT) capabilities, allowing for real-time monitoring and data collection. This connectivity enables operators to track performance metrics, ensuring optimal performance.
- Predictive Maintenance: By analyzing data from sensors, manufacturers can implement predictive maintenance strategies, allowing for early detection of potential issues. This reduces downtime and maintenance costs, ultimately enhancing system reliability.
- Remote Monitoring: Smart technologies provide the flexibility to manage sanitary systems remotely. This capability is particularly valuable in environments with multiple processing lines, allowing for centralized oversight and quicker response to anomalies.
3. Energy Efficiency Technologies in Sanitary Pumps and Valves
Energy consumption is a critical consideration in modern manufacturing processes. Innovations in sanitary pumps and valves technologies address this concern:
- Variable Frequency Drives (VFDs): VFDs allow for precise control of pump speed and flow rates, enabling efficient operation based on real-time demand. This reduces energy consumption and minimizes wear on equipment.
- Energy Recovery Systems: Some advanced sanitary pumps incorporate energy recovery technologies that capture and reuse energy within the system. These systems significantly lower the overall energy footprint of operations.
- Optimized Hydraulic Designs: Manufacturers are developing pumps and valves with optimized hydraulic designs to minimize friction losses and maximize performance, further contributing to energy savings.
Download PDF Brochure @ https://www.marketsandmarkets.com/pdfdownloadNew.asp?id=165107743
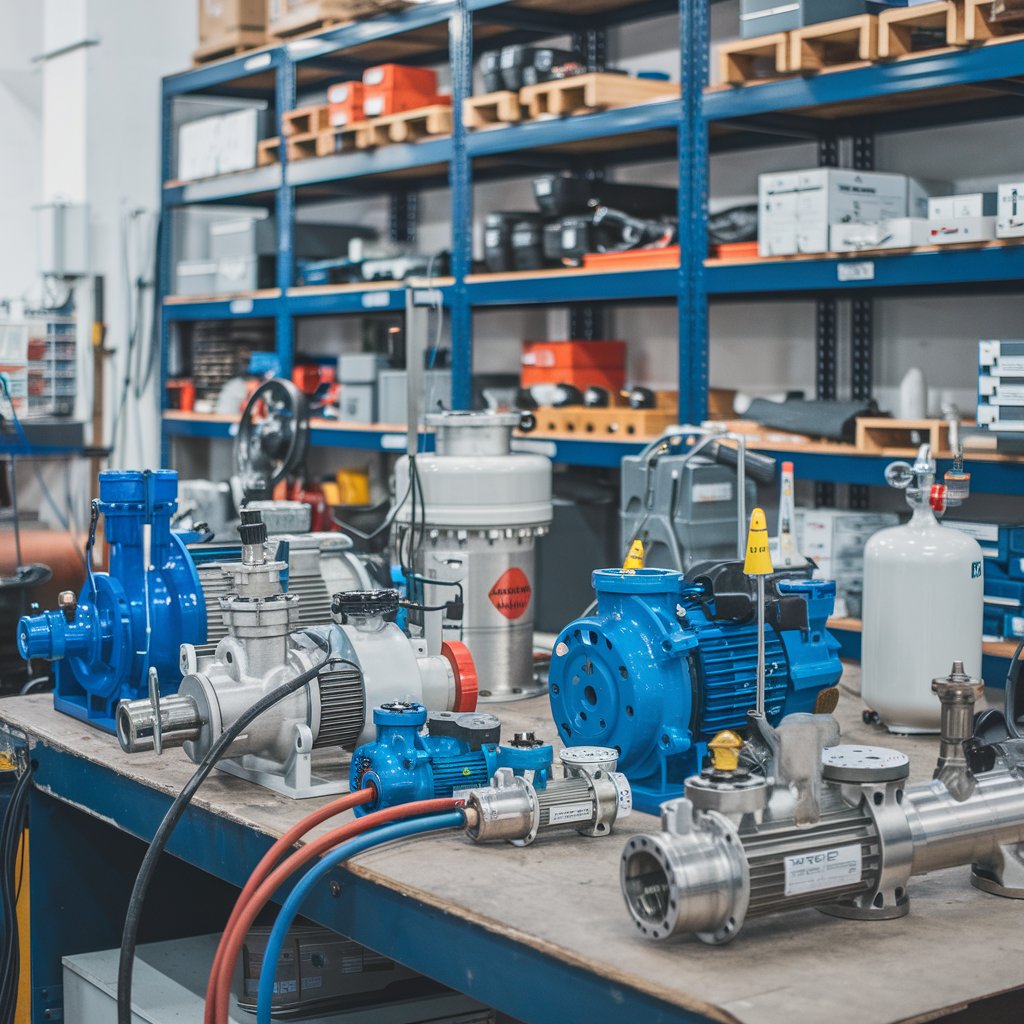
4. Advanced Materials and Coatings in Sanitary Pumps and Valves
The choice of materials in sanitary pumps and valves technologies is critical for ensuring performance and longevity:
- Corrosion-Resistant Materials: High-grade stainless steel is standard, but innovations are leading to the use of advanced alloys and composites that offer superior resistance to corrosion and chemical attack, extending equipment lifespan.
- Anti-Fouling Coatings: Innovative coatings prevent the buildup of residues on pump and valve surfaces, reducing cleaning frequency and improving system efficiency. These coatings ensure smoother operation and easier maintenance.
- Biocompatible Materials: In pharmaceutical and biotech applications, the use of biocompatible materials ensures that products remain safe and effective, meeting regulatory requirements.
5. Modular and Customizable Solutions in Sanitary Pumps and Valves
The need for flexibility in manufacturing processes is driving demand for modular and customizable sanitary pumps and valves:
- Modular Designs: Modular components allow for easy configuration and integration into existing systems. This adaptability enables manufacturers to modify and scale operations efficiently.
- Custom Features: Many suppliers offer customization options to meet specific process requirements, including tailored flow rates and pressure ratings. This ensures that the equipment fits seamlessly into diverse applications.
6. Regulatory Compliance and Validation in Sanitary Pumps and Valves
Sanitary pumps and valves technologies must adhere to stringent regulatory standards to ensure product safety and quality:
- Validation Support: Many manufacturers provide documentation and support for validation processes, ensuring that their equipment meets industry regulations. This support is crucial for companies operating in regulated environments.
- Cleaning-in-Place (CIP) Solutions: CIP technologies allow for efficient cleaning of sanitary systems without disassembly, ensuring thorough sanitation and compliance with health standards.
- Traceability Features: Advanced sanitary systems are equipped with features that enhance traceability, facilitating compliance with food safety and pharmaceutical regulations.
Sanitary pumps and valves technologies are essential for maintaining hygiene, efficiency, and compliance in critical industries. With innovations such as smart technology integration, energy efficiency improvements, advanced materials, and customizable solutions, these systems are evolving to meet the demands of modern manufacturing processes. As industries continue to prioritize safety and sustainability, the role of sanitary pumps and valves will be increasingly vital in ensuring the integrity of products and processes. Embracing these technologies will not only enhance operational performance but also contribute to a safer and more efficient future for the food and beverage, pharmaceutical, and biotech sectors
FAQ Sanitary Pumps and Valves Industry :
What technologies are currently being used in sanitary pumps and valves?
Key technologies include hygienic design principles, smart technology integration (like IoT for real-time monitoring), energy efficiency features (such as variable frequency drives), advanced materials (including corrosion-resistant alloys), and modular and customizable solutions.
Why is hygiene important in sanitary pumps and valves?
Hygiene is crucial in these industries to prevent contamination and ensure product safety. Sanitary pumps and valves are designed to facilitate thorough cleaning and minimize the risk of bacterial growth, which is essential for compliance with health regulations.
How do smart technologies enhance sanitary pumps and valves?
Smart technologies enable real-time monitoring and data collection, allowing operators to track performance metrics such as flow rates and pressure. This leads to improved operational efficiency, predictive maintenance, and remote monitoring capabilities.
What are the benefits of energy efficiency in sanitary pumps and valves?
Energy efficiency reduces operational costs and minimizes the environmental impact. Technologies like variable frequency drives allow for precise control of flow rates, leading to significant energy savings and reduced wear on equipment.