In today’s fast-paced industrial environment, companies are increasingly turning to technological innovations to enhance their operational efficiency and ensure product quality. One such innovation is the integration of Artificial Intelligence (AI) and the Internet of Things (IoT) into Non-Destructive Testing (NDT) and inspection processes. These technologies are reshaping the NDT landscape, transforming the way industries approach quality control, asset management, and safety compliance.
AI and IoT are at the forefront of a digital transformation in the NDT market, offering more precise, real-time, and predictive insights than traditional methods. As industries worldwide recognize the potential of these technologies, the global NDT market is undergoing a profound shift, enabling safer, smarter, and more efficient operations across various sectors.
The NDT and inspection industry is expected to reach USD 18.4 billion by 2029 from 11.6 billion in 2024, at a CAGR of 9.6% during the 2024-2029 period
The Role of NDT in Industrial Quality Control
Non-Destructive Testing (NDT) is a crucial process in modern industrial quality control, providing a method for evaluating the integrity, structure, and composition of materials without causing damage. NDT methods, such as ultrasonic testing, X-ray inspection, eddy current testing, and visual inspection, help identify potential defects in critical assets, ensuring they perform optimally and comply with safety standards.
From aerospace and automotive to oil & gas and infrastructure, NDT is essential for detecting internal flaws like cracks, corrosion, and weld defects in materials that could otherwise go unnoticed. The ability to perform inspections without compromising the integrity of the components is what makes NDT indispensable for industries where safety, reliability, and compliance are non-negotiable.
However, despite its critical role, traditional NDT methods often rely heavily on manual labor, can be time-consuming, and may involve significant human error. This is where AI and IoT come into play, dramatically enhancing the speed, accuracy, and predictive capabilities of NDT systems.
The Impact of AI on NDT and Inspection
Artificial Intelligence is driving a revolution in NDT by improving defect detection, automating the analysis of inspection data, and optimizing overall inspection workflows. AI-powered systems are capable of processing vast amounts of data from inspection tools, learning from historical data, and applying algorithms that detect even the most subtle defects or anomalies.
Key AI-driven advancements include:
Automated Image Recognition and Analysis AI-enabled inspection systems can analyze images or videos captured during NDT inspections with greater precision than the human eye. Using machine learning algorithms, these systems can identify cracks, corrosion, and other defects by comparing real-time data against vast databases of known defect patterns. This significantly reduces human error and enhances the consistency and reliability of inspections.
Predictive Maintenance AI’s ability to process historical and real-time data makes predictive maintenance a reality in NDT. By analyzing sensor data, AI can predict the likelihood of equipment failure before it occurs, helping industries implement proactive maintenance strategies. This reduces downtime, prevents unexpected breakdowns, and optimizes asset performance.
Improved Accuracy and Efficiency Machine learning algorithms improve the accuracy of defect detection by continuously learning from data. This means AI systems become smarter over time, improving their performance and reducing false positives or negatives. Faster data analysis and automated decision-making lead to quicker inspection processes, which is especially critical in high-stakes industries like aerospace and oil & gas.
Download PDF Brochure @ https://www.marketsandmarkets.com/pdfdownloadNew.asp?id=882
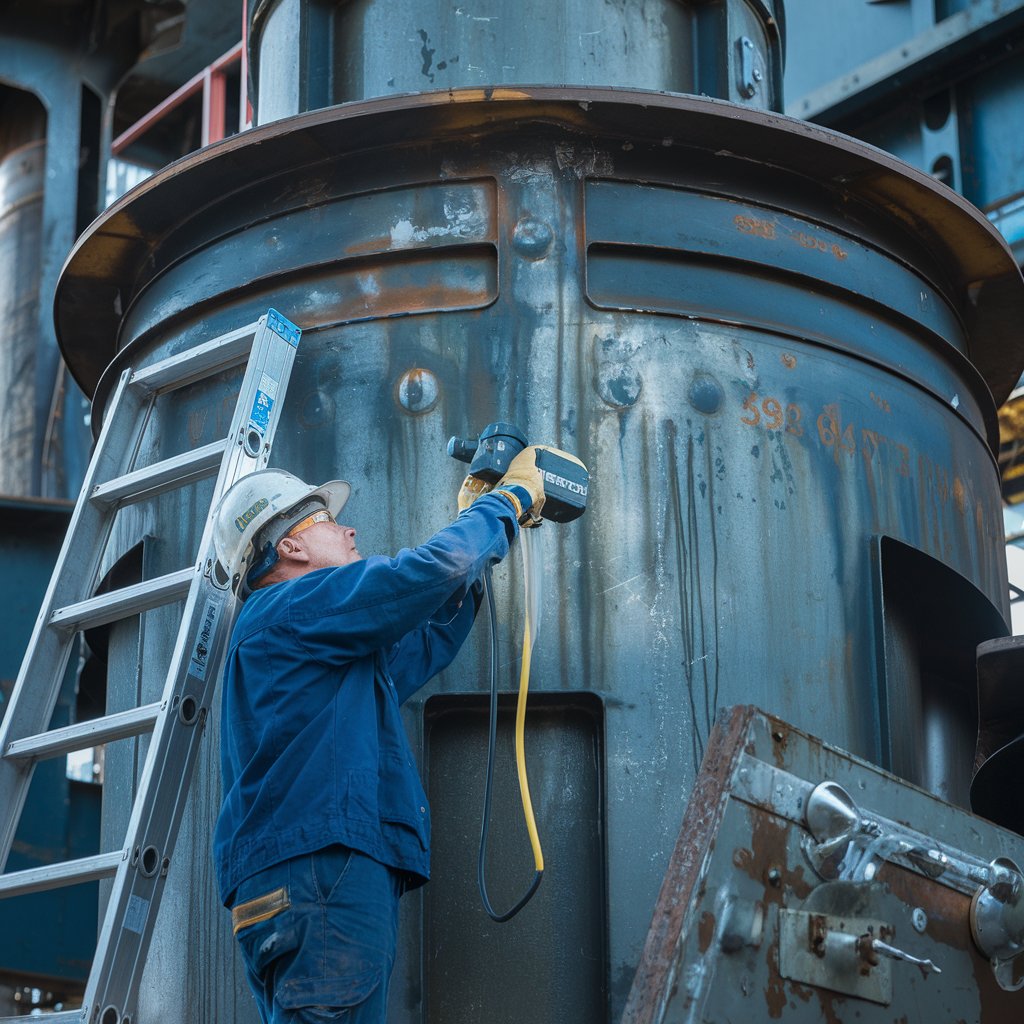
How IoT is Transforming NDT Inspections
The Internet of Things (IoT) plays a key role in connecting NDT tools, equipment, and assets in real-time, enabling continuous monitoring and remote inspections. IoT devices embedded in machinery, structures, and infrastructure are capable of collecting a wide range of data, including temperature, pressure, vibration, and acoustic signals, which can be used for NDT purposes.
Key IoT-driven advancements include:
Real-time Data Collection and Remote Monitoring IoT-enabled sensors installed on industrial assets provide real-time data on equipment conditions, allowing for continuous and remote monitoring. This makes it possible to detect anomalies and potential issues at any moment, even in remote or hazardous locations, reducing the need for manual inspections.
Integration with Cloud Computing IoT sensors integrated with cloud computing platforms enable the centralized collection and analysis of inspection data. This provides engineers and operators with remote access to inspection results, allowing for quicker decision-making and the ability to monitor multiple assets simultaneously from anywhere in the world.
Continuous Monitoring and Condition-Based Monitoring (CBM) IoT-driven systems allow for continuous monitoring of asset health, enabling condition-based monitoring (CBM) instead of relying solely on scheduled inspections. This provides a more accurate, real-time understanding of an asset’s condition, leading to improved performance and reduced unplanned downtime.
Automation of Routine Inspections IoT-enabled robotic inspection systems can autonomously conduct inspections in hazardous or hard-to-reach locations. Drones, for example, equipped with IoT sensors, can inspect pipelines, bridges, and powerlines, transmitting inspection data in real-time to operators. This increases inspection efficiency and safety while reducing operational costs.
The Synergy Between AI and IoT in NDT
When combined, AI and IoT create a powerful synergy that elevates NDT inspections to new levels of sophistication. While IoT facilitates real-time data collection, AI analyzes and interprets that data, enabling industries to make more informed, data-driven decisions. This partnership unlocks new possibilities for predictive maintenance, operational optimization, and asset management.
How AI and IoT Work Together in NDT:
Automated Decision-Making With IoT devices continuously collecting data from sensors, AI algorithms can analyze this information in real-time, detecting anomalies, predicting failures, and making decisions automatically based on predefined thresholds. This reduces the need for manual intervention and ensures faster response times.
Integrated Monitoring Systems AI and IoT-enabled NDT systems can integrate with a centralized monitoring platform, allowing engineers to track assets and monitor the performance of various systems remotely. Data from multiple sources can be combined to create a comprehensive picture of asset health, enabling early identification of potential failures.
Predictive Analytics and Optimization IoT sensors provide the raw data, while AI applies predictive analytics to forecast asset behavior and potential failures. The system can then optimize maintenance schedules, predict repairs, and improve the overall lifecycle management of assets.
The Future of AI and IoT in NDT
As AI and IoT continue to evolve, their impact on the NDT industry is poised to grow exponentially. The adoption of these technologies will enable industries to achieve higher levels of automation, efficiency, and safety, paving the way for smarter, more connected industrial operations.
Further AI advancements will improve deep learning and image recognition capabilities, leading to even more precise defect detection and reduced reliance on human inspectors.
IoT sensors will become more sophisticated and cost-effective, allowing for greater data collection, longer battery life, and integration with next-generation communication networks like 5G.
Edge computing will allow for real-time processing of data directly at the source, reducing latency and enabling faster decision-making, which will be critical in industries like aerospace, automotive, and energy.
The integration of AI and IoT into NDT and inspection processes is revolutionizing the way industries approach quality control and asset management. By enhancing accuracy, reducing human error, enabling predictive maintenance, and improving operational efficiency, these technologies are reshaping the future of industrial inspections globally.
As the world moves toward smarter, more automated industries, the NDT market will continue to evolve with AI and IoT at its core, driving a new era of smart inspections that promise safer, more efficient, and more sustainable industrial operations.