Collaborative robots, or cobots, are transforming industries by working alongside human operators to enhance efficiency and safety. Unlike traditional robots that operate in isolation, cobots are designed to interact seamlessly with people. Here’s a closer look at the key technologies driving the evolution of collaborative robots.
The Collaborative Robot industry size is projected to grow from USD 1.9 billion in 2024 and is estimated to reach USD 11.8 billion by 2030; it is expected to grow at a Compound Annual Growth Rate (CAGR) of 35.2% from 2024 to 2030. The growth of the Collaborative Robot industry is driven by higher return on investment than traditional industrial robotic systems; increased demand in e-commerce and logistics sectors; significant benefits in businesses of all sizes; easy programming of cobots.
Technologies Behind Collaborative Robots :
1. Sensor Technologies
Enhancing Perception and Safety
Sensor technologies are integral to the functionality of cobots, enabling them to perceive their surroundings and react accordingly. These sensors play a critical role in ensuring safe and effective interactions between robots and humans.
Proximity Sensors: These sensors detect nearby objects, allowing cobots to navigate safely around humans and obstacles. By continuously monitoring the environment, they can adjust their movements in real-time, preventing collisions and ensuring that they operate safely in shared spaces.
Force/Torque Sensors: These sensors measure the forces exerted during interactions, helping to prevent injuries when a cobot comes into contact with a human. For instance, if a worker inadvertently touches the cobot, the force sensor can detect this and prompt the robot to stop or slow down, significantly reducing the risk of accidents.
Vision Systems: Advanced cameras and visual sensors provide cobots with the ability to recognize objects, read labels, and navigate complex environments. This capability is essential for tasks such as quality control, where visual inspection of products is necessary. The integration of vision systems allows cobots to perform a wide range of functions that require a high level of precision and adaptability.
These sensor technologies enable cobots to operate safely and efficiently in dynamic settings, making them suitable for various applications, from manufacturing to healthcare.
2. Artificial Intelligence
Smart Adaptation and Learning
Artificial intelligence (AI) is a game-changer for collaborative robots, allowing them to learn from their experiences and adapt to new tasks. The integration of AI significantly enhances the autonomy and functionality of cobots.
Machine Learning: Cobots equipped with machine learning algorithms can analyze data from past tasks to improve their performance over time. For example, if a cobot struggles with a particular assembly task, machine learning can help it adjust its approach based on previous outcomes, leading to fewer errors and greater efficiency.
Computer Vision: AI-powered vision systems enable cobots to identify and classify objects accurately. This capability allows them to interact with different components or products effectively, which is crucial in environments like assembly lines where precision is key. By using deep learning techniques, cobots can recognize objects under varying conditions, enhancing their versatility.
Natural Language Processing: Some collaborative robots are being developed with the ability to understand voice commands, thanks to advancements in natural language processing. This feature enables human operators to communicate with cobots more intuitively, making it easier to issue commands and adjustments without the need for complex programming.
AI integration not only enhances the autonomy of collaborative robots but also enables them to perform more complex tasks, making them invaluable in diverse industrial settings.
Download PDF Brochure @
https://www.marketsandmarkets.com/pdfdownloadNew.asp?id=194541294
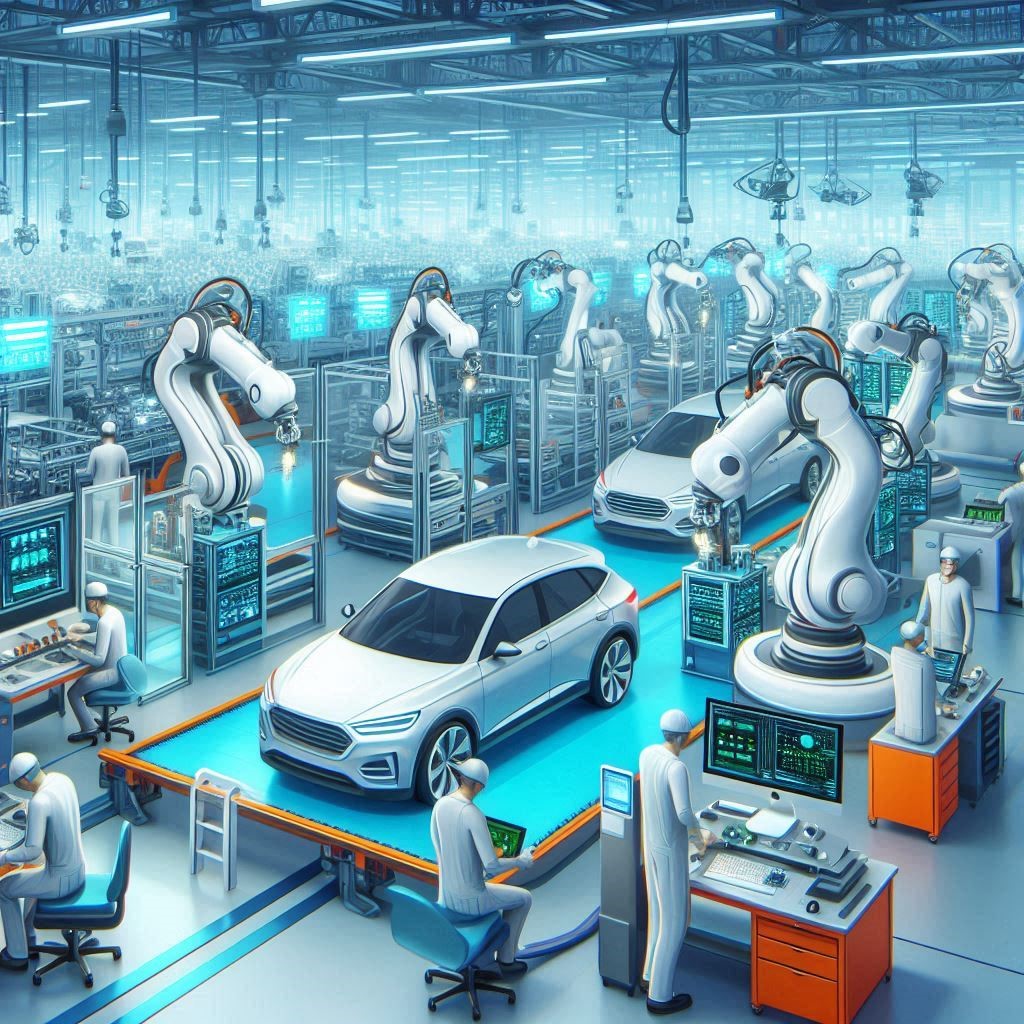
3. Safety Features
Prioritizing Human Safety
Safety is a fundamental consideration in the design and operation of collaborative robots. Unlike traditional industrial robots that often require physical barriers, cobots are engineered with features that prioritize human safety.
Speed and Force Limitations: Cobots are programmed to operate at reduced speeds when in proximity to humans. This limitation minimizes the risk of injury by ensuring that the robot’s movements are predictable and controlled. If a worker enters the robot’s workspace, the cobot can adjust its speed or even halt its operations entirely.
Emergency Stop Mechanisms: Equipped with emergency stop buttons and sensors, cobots can immediately halt operations if a human unexpectedly enters their workspace. This feature is crucial for maintaining a safe environment, as it allows for quick responses to potential hazards.
Compliance with Safety Standards: Many collaborative robots are designed to meet international safety standards, such as ISO 10218 and ISO/TS 15066. Compliance with these standards ensures that cobots adhere to rigorous safety protocols, providing peace of mind for operators and businesses.
These safety features make collaborative robots suitable for environments where humans and robots interact frequently, fostering a culture of safety in the workplace.
4. Programming and Integration
Streamlined Usability
Advancements in programming and integration have made collaborative robots more user-friendly and easier to deploy in existing workflows. These improvements are essential for businesses looking to enhance their automation capabilities without extensive downtime or training.
Intuitive Programming Interfaces: Modern cobots often come equipped with user-friendly graphical programming interfaces. These interfaces allow operators with minimal coding experience to set up and configure robots easily. The drag-and-drop functionality simplifies the programming process, enabling quicker adjustments to tasks and workflows.
Simulation Tools: Software simulation tools enable users to visualize and test robot movements in a virtual environment before deployment. This capability reduces the risk of errors and optimizes workflows by allowing operators to identify potential issues and make adjustments before actual implementation.
Seamless Integration: Collaborative robots can be integrated into existing manufacturing systems with minimal disruption. Their ability to work alongside human workers and other machines enhances overall operational efficiency, allowing businesses to leverage automation without extensive reconfiguration of their workflows.
These advancements facilitate the quick adoption of collaborative robots across various industries, making them an attractive option for businesses seeking to improve productivity.
5. Human-Robot Interaction Models
Fostering Effective Collaboration
Effective human-robot interaction (HRI) is essential for successful collaboration between cobots and human workers. A well-designed HRI model enhances productivity and ensures that both parties can work together safely and efficiently.
Communication Protocols: Establishing clear communication methods is vital for effective collaboration. Cobots may use visual signals, sounds, or tactile feedback to convey information to human operators, ensuring that both parties understand each other’s actions and intentions.
Shared Workspaces: Cobots are designed to operate in close proximity to human workers. Effective HRI models ensure that both can perform their tasks without interfering with one another. This shared workspace concept allows for greater flexibility in workflows and task assignments.
Adaptive Learning: future of Cobots can be programmed to learn from human behavior and adapt to individual work styles. By observing how human operators perform tasks, cobots can adjust their actions to better align with human preferences, leading to more effective collaboration.
Robust HRI models not only enhance productivity but also create a safer and more comfortable working environment for human workers, fostering a positive relationship between humans and robots.
Key Collaborative Robot Companies are
- Universal Robots A/S (Denmark),
- FANUC CORPORATION (Japan),
- ABB (Switzerland),
- TECHMAN ROBOT INC. (Taiwan), and
- AUBO (BEIJING)
- ROBOTICS TECHNOLOGY CO., LTD (China),
- KUKA AG (Germany),
- Doosan Robotics Inc. (South Korea),
- Denso Corporation (South Korea),
- YASKAWA ELECTRIC CORPORATION (Japan),
- Rethink Robotics GmBH (Germany) among others.