The U.S. Non-Destructive Testing (NDT) market is witnessing significant growth, driven by the rapid adoption of advanced technologies in the fields of ultrasonic, radiographic, and magnetic testing. These methods play a critical role in ensuring the integrity and safety of materials and structures across industries like aerospace, oil and gas, manufacturing, construction, and energy. As demand for more accurate, efficient, and cost-effective inspection solutions increases, the U.S. NDT market is evolving with cutting-edge innovations and techniques.
Non-destructive testing is essential for inspecting the condition of materials without causing damage. By enabling engineers to detect flaws, cracks, and potential failures in components, NDT helps businesses prevent catastrophic breakdowns, reduce maintenance costs, and improve overall safety standards. As the need for preventive maintenance, asset integrity, and quality control grows, the market is being shaped by advancements in key testing technologies like ultrasonic testing (UT), radiographic testing (RT), and magnetic particle testing (MPT).
1. Ultrasonic Testing (UT): A Leap Forward in Precision
Ultrasonic Testing (UT) is one of the most commonly used methods for inspecting materials, especially metals, for internal flaws and discontinuities. By emitting high-frequency sound waves into a material, UT detects defects based on the reflection of sound waves from internal surfaces. Advances in digital ultrasonic testing and phased array ultrasound (PAUT) technologies have significantly enhanced the precision, speed, and versatility of UT.
The growing demand for aerospace components, pressure vessels, and pipeline systems has accelerated the adoption of advanced UT technologies. For example, PAUT allows for high-resolution inspection of complex geometries, such as welded joints, which are critical for the oil and gas and nuclear energy sectors. Additionally, automated ultrasonic testing systems are reducing human error and improving operational efficiency by streamlining inspections and providing real-time feedback to technicians.
Moreover, with the rise of Industry 4.0 and the Internet of Things (IoT), ultrasonic testing equipment is becoming increasingly connected, allowing for remote monitoring and data analytics. This enables predictive maintenance and better decision-making by offering insights into the health of machinery, pipelines, and infrastructure.
2. Radiographic Testing (RT): A Cornerstone of Structural Integrity
Radiographic Testing (RT) involves the use of X-rays or gamma rays to inspect the internal structure of materials. This technique is especially effective for detecting internal flaws such as cracks, voids, and inclusions in thick-walled components, making it a staple in industries like aerospace, energy, and automotive.
In recent years, digital radiography (DR) and computed tomography (CT) have revolutionized the way RT is performed. Unlike traditional film-based radiography, digital radiography provides faster results with enhanced image quality. Additionally, DR reduces radiation exposure and allows for immediate image review, which speeds up the inspection process.
One of the biggest advantages of digital radiography is its ability to create highly detailed images of complex structures, which is critical for industries that rely on highly engineered components. In nuclear power plants, for example, RT is used extensively to inspect the integrity of critical systems and ensure compliance with stringent safety standards. Similarly, in aerospace, where the precision of parts is paramount, RT ensures that internal defects, even those invisible to the naked eye, are identified before they become critical issues.
The development of 3D X-ray imaging and advanced CT scanning is pushing the boundaries of RT even further, enabling inspectors to create a comprehensive 3D model of an object’s internal structure. This allows for more accurate assessments of part conditions and opens up new possibilities for non-destructive inspection across industries.
Download PDF Brochure @ https://www.marketsandmarkets.com/pdfdownloadNew.asp?id=882
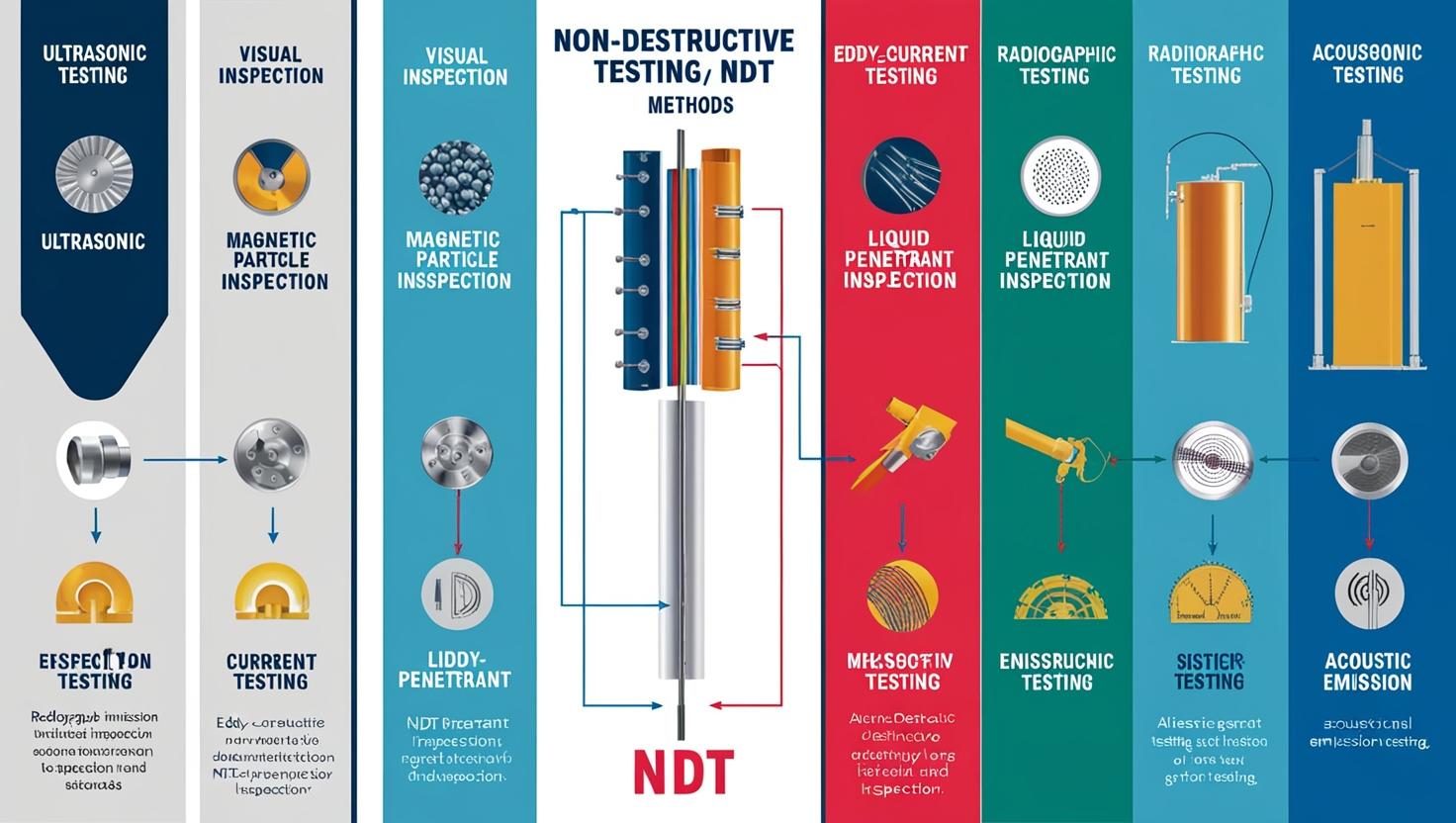
3. Magnetic Particle Testing (MPT): Enhancing Surface Integrity
Magnetic Particle Testing (MPT) is a non-destructive testing method used to detect surface and near-surface defects in ferromagnetic materials such as steel. MPT works by magnetizing a part and applying fine magnetic particles to its surface. If there are any surface cracks or imperfections, the particles will accumulate at the defect, making it visible under UV or white light.
Advancements in high-sensitivity magnetic particle testing and portable MPT devices are fueling the market’s growth. Modern MPT systems are more sensitive than ever before, allowing inspectors to detect even the smallest surface anomalies. These improvements are particularly beneficial for sectors like automotive manufacturing, railways, and construction, where surface defects can lead to serious safety hazards and costly failures if left undetected.
Portable MPT systems, which use battery-operated and handheld units, are enabling field inspections in remote locations. This flexibility is essential for inspecting equipment in hard-to-reach areas, such as oil rigs, wind turbines, and power plants. The ability to conduct these tests on-site, rather than sending components back to a lab for inspection, reduces downtime and enhances overall operational efficiency.
Key Market Drivers and Trends
Several factors are driving the growth of the U.S. NDT market, with advancements in ultrasonic, radiographic, and magnetic testing technologies at the forefront:
1. Stricter Safety Regulations
As industries continue to face increasing pressure to meet stringent safety standards, NDT technologies are becoming essential for preventing accidents and ensuring compliance. In sectors like aerospace, oil and gas, and nuclear energy, NDT testing is a mandatory part of regular safety inspections. New regulations and guidelines are pushing companies to adopt the latest NDT technologies to stay compliant and avoid costly fines or shutdowns.
2. Aging Infrastructure
The U.S. is home to many aging infrastructures, such as bridges, pipelines, and power plants, that require constant monitoring and maintenance. NDT methods like UT, RT, and MPT play a key role in assessing the structural integrity of these aging systems and detecting defects before they result in catastrophic failures. The need for more effective and efficient ways to assess the health of infrastructure is fueling demand for advanced NDT technologies.
3. Adoption of Automation and Robotics
The increasing use of robotics and automation in NDT inspections is transforming the industry. Automated systems can conduct inspections more consistently and efficiently, reducing the risk of human error and increasing the throughput of inspections. Drones equipped with ultrasonic testing and radiographic imaging capabilities are also being used for remote inspections of hard-to-reach areas, such as offshore oil platforms or high-rise buildings.
4. Emerging Applications in Additive Manufacturing
As additive manufacturing (3D printing) continues to grow, ensuring the quality of 3D-printed parts has become a priority. NDT methods like ultrasonic testing and radiographic imaging are now being applied to inspect 3D-printed components for internal defects or inconsistencies, ensuring that these parts meet stringent quality standards.
The U.S. NDT market is experiencing a surge in demand, driven by advancements in ultrasonic, radiographic, and magnetic testing technologies. These methods are playing an increasingly important role in ensuring the integrity, safety, and longevity of critical components across industries like aerospace, energy, automotive, and manufacturing.
With innovations in digital radiography, phased array ultrasound, and robotic inspections, the market is set to continue evolving, offering businesses more efficient, precise, and cost-effective solutions to meet the growing demands for non-destructive testing. As industries strive to minimize downtime, reduce maintenance costs, and enhance safety, NDT technologies will remain an essential part of industrial operations for years to come.